The Art and Science of Sanding Ceramic A Comprehensive Guide
Sanding ceramics is an essential process in the world of pottery and ceramic crafting. Whether you are an artist looking to perfect your creations or a DIY enthusiast trying to refurbish ceramic items, understanding the techniques and materials involved in sanding ceramics can significantly enhance your results. This article delves into the art and science of sanding ceramic surfaces, highlighting its importance, methods, and best practices.
Why Sand Ceramic?
Ceramics, whether they are handcrafted pottery, tiles, or porcelain collectibles, often require sanding for multiple reasons. Firstly, sanding helps to smooth out rough edges, which not only improves the aesthetics of the piece but also makes it more comfortable to handle. Secondly, it allows for better adhesion when applying glazes or paints, ensuring that the finishes bond effectively to the surface. Lastly, sanding can help remove imperfections such as fingerprints, scratches, or inconsistencies that may detract from the overall appearance of the ceramic.
Types of Sanding Techniques
1. Manual Sanding This traditional method involves using sandpaper or sanding blocks. Start with a coarser grit sandpaper (around 60-80 grit) to remove large imperfections and gradually progress to finer grits (200-400 grit) for a smoother finish. When sanding, always work in a circular motion to avoid creating visible grooves on the surface.
2. Power Sanding For larger projects or when dealing with harder ceramics, power sanders can be a time-saving tool. Orbital sanders or rotary tools equipped with sanding discs can provide a uniform finish. However, caution is required to avoid overheating the ceramic, which can lead to cracking or unwanted changes in color.
3. Wet Sanding This technique involves using water to lubricate the sandpaper. Wet sanding is particularly useful for delicate ceramics as it reduces the amount of dust generated and decreases the risk of scratching the surface. It is advisable to start with a medium grit and gradually move to finer grits, rinsing the piece regularly to prevent buildup.
sanding ceramic
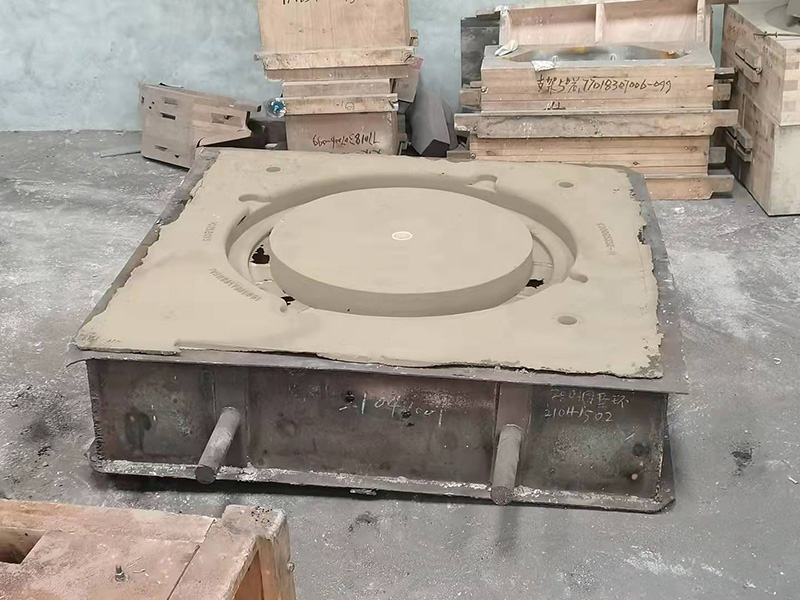
Choosing the Right Sandpaper
The grit of the sandpaper plays a crucial role in the sanding process. Coarser grits (below 100) are suitable for heavy material removal, while medium grits (100-200) are ideal for smoothing out surfaces. Fine grits (200 and above) are perfect for achieving a polished finish. When selecting sandpaper, consider the type of ceramic you are working with; for instance, porcelain may require finer grit compared to stoneware.
Safety Considerations
Sanding ceramics can create fine dust particles that are harmful when inhaled, so proper safety gear is essential. Always wear a dust mask or respirator to protect your lungs, and goggles to safeguard your eyes from flying debris. Ensuring proper ventilation in your workspace can also help mitigate dust exposure.
Finishing Touches
After sanding, it’s vital to clean the ceramic thoroughly to remove any residual dust or particles. Use a damp cloth or sponge and allow the piece to dry completely before applying any primer, paint, or glaze. This step will ensure that the final finish adheres properly and achieves the desired look.
Conclusion
Sanding ceramic is both an art and a science that enhances the quality and aesthetics of ceramic pieces. Whether you’re polishing a vase or preparing a tile for decorating, the techniques outlined in this guide will help you achieve a professional finish. With the right tools, techniques, and safety measures, anyone can master the art of sanding ceramic. Embrace this essential skill in your ceramic projects, and watch as your creations transform into stunning works of art.
Post time:12 月 . 12, 2024 19:39
Next:sand cast metal