The Art and Science of Sand Casting Metal
Sand casting, also known as sand mold casting, is one of the oldest and most widely used metal casting processes. This technique involves creating a mold from a sand mixture, into which molten metal is poured to create a desired shape. Its versatility and simplicity make it an integral part of modern manufacturing, playing a pivotal role across various industries, from automotive to aerospace.
The Sand Casting Process
The sand casting process can be broken down into several key steps
1. Pattern Creation The first step in sand casting involves creating a pattern, which is a replica of the final product. Patterns can be made from various materials, including wood, metal, or plastic, depending on the complexity and scale of the object to be cast.
2. Mold Preparation The next step is preparing the sand mold. The most commonly used sand is silica sand, which is mixed with a binder, typically clay, to help it retain shape. The mixture is compacted around the pattern to form a mold, leaving a cavity in the shape of the object.
3. Pouring the Metal Once the mold is prepared, it is heated to remove moisture and then assembled. Molten metal is poured into the mold cavity, filling it completely. The temperature of the molten metal is crucial; it must be hot enough to flow easily into the mold but not so hot that it causes unwanted reactions with the sand.
4. Cooling and Solidification After the metal is poured, it is allowed to cool and solidify. This phase can vary in length depending on the size and thickness of the casting. Proper cooling is essential to avoid stresses that could lead to defects.
5. Mold Removal Once the metal has completely solidified, the sand mold is broken away to reveal the cast object. The sand can often be recycled and reused for future casts, making it a cost-effective choice.
6. Finishing Touches The final step involves cleaning the cast object and removing any excess material, such as gates and risers. This process may also include additional machining or surface treatments to achieve the desired finish.
Advantages of Sand Casting
Sand casting offers several key advantages over other casting processes
- Cost-Effectiveness Sand casting is relatively inexpensive, especially for low to medium production runs. The materials involved are affordable, and the process can be easily scaled.
sand cast metal
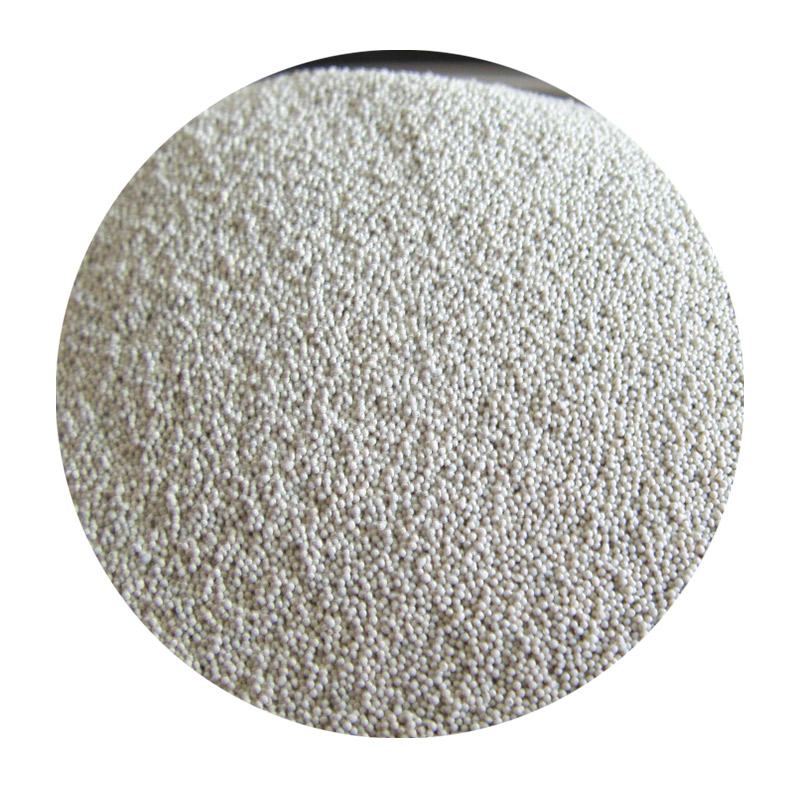
- Versatility This method can accommodate a wide range of metals, including aluminum, brass, iron, and steel. It is also suitable for producing complex shapes and large components, which may be challenging for other casting techniques.
- Reusability The sand used in molds can be recycled multiple times, reducing waste and making the process environmentally friendly to some extent
.- Tolerance Levels Sand casting generally allows for moderate tolerances, making it suitable for many industrial applications.
Limitations of Sand Casting
While sand casting has numerous advantages, it also has its limitations
- Surface Finish The finish quality of sand cast parts can be rough, often requiring additional processing such as grinding or machining.
- Dimensional Accuracy Compared to methods like investment casting, sand casting can have lower dimensional accuracy, which can be a concern for highly precise components.
- Labor-Intensive The process can be labor-intensive and may require skilled workers, especially in the pattern-making and mold preparation stages.
Applications of Sand Casting
Sand casting is employed across diverse sectors. In the automotive industry, for example, it is used to manufacture engine blocks, transmission cases, and various other components. The aerospace industry utilizes sand casting for turbine housings and other critical components, where precision and reliability are paramount. Additionally, the process is important in producing art pieces, sculptures, and intricate designs, showcasing its versatility beyond industrial applications.
Conclusion
Sand casting remains a foundational technique in metal manufacturing, balancing art and engineering. Its ability to produce complex shapes and accommodate various materials ensures its relevance in contemporary industry. As technology advances, innovations in sand casting methods continue to enhance its effectiveness and efficiency, ensuring that this ancient technique thrives in the modern world. Whether for functional components or decorative pieces, sand casting embodies both tradition and innovation in metalworking.
Post time:10 月 . 19, 2024 07:04
Next:الفروق بين صب الرمل وصب الاستثمارات في عمليات التصنيع