Understanding Sand Casting Tolerances A Comprehensive Guide
Sand casting is a widely used manufacturing process in which molten metal is poured into a sand mold to create complex shapes. This technique is favored for its versatility and cost-effectiveness, especially for producing components in small to medium production runs. However, one critical aspect that manufacturers must consider is the tolerance of the cast parts. Tolerances determine how much variation is acceptable in the dimensions of the finished product, and they play a significant role in the success of any casting project.
What are Tolerances in Sand Casting?
Tolerances refer to the permissible limits of variation in a physical dimension or measured value. In the context of sand casting, these tolerances are crucial for ensuring that the finished product fits properly with other components and performs as designed. There are several types of tolerances that engineers and designers must understand when working with sand casting
1. Dimensional Tolerances These are governed by the specific dimensions of the part, including length, width, height, and diameter. In sand casting, the dimensional tolerances can range from ±0.5 mm to ±5 mm or more, depending on the size and complexity of the part.
2. Geometric Tolerances These tolerances manage the shape and orientation of the features on the part. For example, flatness, roundness, and parallelism are all geometric tolerances that might need to be specified.
3. Surface Finish Tolerances The finish of the surface can greatly affect the performance and appearance of the final casting. Sand casting inherently produces rough surfaces due to the sand’s granular texture. Standard surface finish for sand cast parts can be rated between 125 to 250 microinches (3.2 to 6.3 micrometers), but finer finishes may be achieved with additional machining processes.
4. Weight Tolerances Ascast metal parts can have slight weight variations due to the pouring process. Depending on the part’s design, weight tolerance can range from ±0.5% to ±10%.
Factors Influencing Tolerance in Sand Casting
Several factors influence the tolerances achievable in sand casting. Understanding these variables is key to improving quality and performance
1. Mold Design The design of the mold greatly affects the dimensional accuracy of the cast part. Complex shapes may require more intricate mold designs, which can introduce variability.
sand casting tolerances
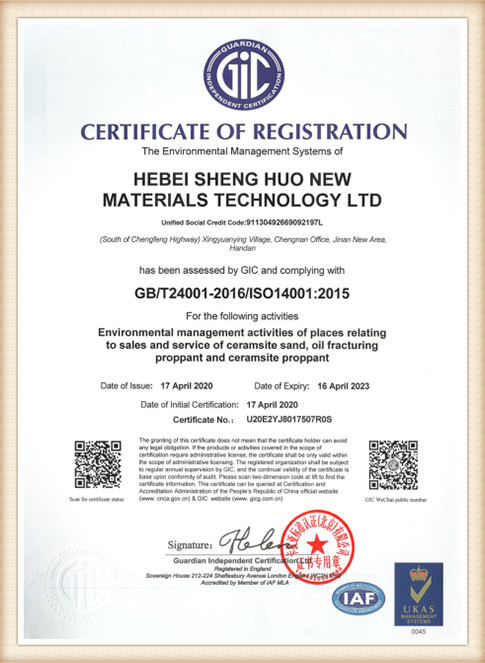
2. Material Selection The type of metal used affects how it flows into the mold and how it responds during the cooling process. Different metals shrink at different rates, impacting the final dimensions of the casting.
3. Cooling Rate The cooling rate of the molten metal is crucial. Rapid cooling can lead to thermal stresses and potential distortions, while slower cooling often yields more dimensionally stable parts.
4. Operator Skill The experience level of the foundry operators plays a significant role. Skilled operators can better control the pouring process, the mold quality, and the handling of the casting, reducing the risk of defects.
5. Post-Casting Processes Sometimes, tolerances can be improved through subsequent machining operations. However, this adds time and costs to the overall process.
Best Practices for Managing Tolerances
To achieve the highest quality results in sand casting, manufacturers can follow several best practices
- Clear Specifications Communicate precise tolerance requirements at the beginning of the project to avoid misunderstandings later in the process. - Simulation and Modeling Utilize computer-aided design (CAD) and simulation software to predict potential issues before physically creating molds and castings.
- Quality Control Implement rigorous quality checks throughout the casting process, including mold preparation, pouring, and final inspection.
- Invest in Training Regular training for operators can enhance skill levels, reduce errors, and ultimately improve the quality of the castings.
Conclusion
Managing tolerances in sand casting is essential for producing high-quality metal components that meet performance requirements. By understanding the various types of tolerances and the factors that influence them, manufacturers can enhance their casting processes. With careful planning, attention to detail, and commitment to quality, sand casting can continue to be a reliable method for creating intricate and precise parts across a variety of industries.
Post time:11 月 . 30, 2024 01:47
Next:Innovative Applications of 3D Printed Sand in Modern Construction and Design Techniques