Sand Casting Services An Overview
Sand casting, also known as sand mold casting, is a widely used metal casting process that involves creating a mold from a mixture of sand, clay, and water. This technique is renowned for its versatility and cost-effectiveness, making it a preferred choice for a variety of industries, including automotive, aerospace, and even art. In this article, we'll delve into the intricacies of sand casting services, exploring its benefits, applications, and the various steps involved in the process.
What is Sand Casting?
At its core, sand casting is a process where sand is used to create a mold for the metal that will be poured into it. The primary materials used in sand casting include silica sand, which is a fine, granular material, and bonding agents like clay and water, which help the sand particles stick together to form a stable mold. This process can produce intricate shapes and designs, making it ideal for both simple and complex parts.
Benefits of Sand Casting
One of the significant advantages of sand casting is its ability to accommodate a wide range of metals, including aluminum, bronze, iron, and steel. This versatility allows manufacturers to select the material that best fits their specific requirements. Sand casting also allows for the production of large and bulky components without the need for excessive investment in expensive molds, as the sand molds can be reused.
Additionally, sand casting offers excellent dimensional accuracy and surface finish. Though the surface finish is generally rougher compared to other casting methods, it can be improved through additional machining processes if required. This method also facilitates the production of components in various sizes, which can be especially beneficial in industries like automotive and aerospace, where parts can vary significantly in dimension.
Applications of Sand Casting
Sand casting is employed in various applications across multiple industries. In the automotive sector, it is used to create engine blocks, transmission cases, and a range of other components. The aerospace industry benefits from sand casting in the production of intricate designs and high-strength parts needed for aircraft and spacecraft. Furthermore, the artistic community often utilizes sand casting to produce sculptures and decorative items, showcasing the technique's creative potential.
The Sand Casting Process
sand casting services
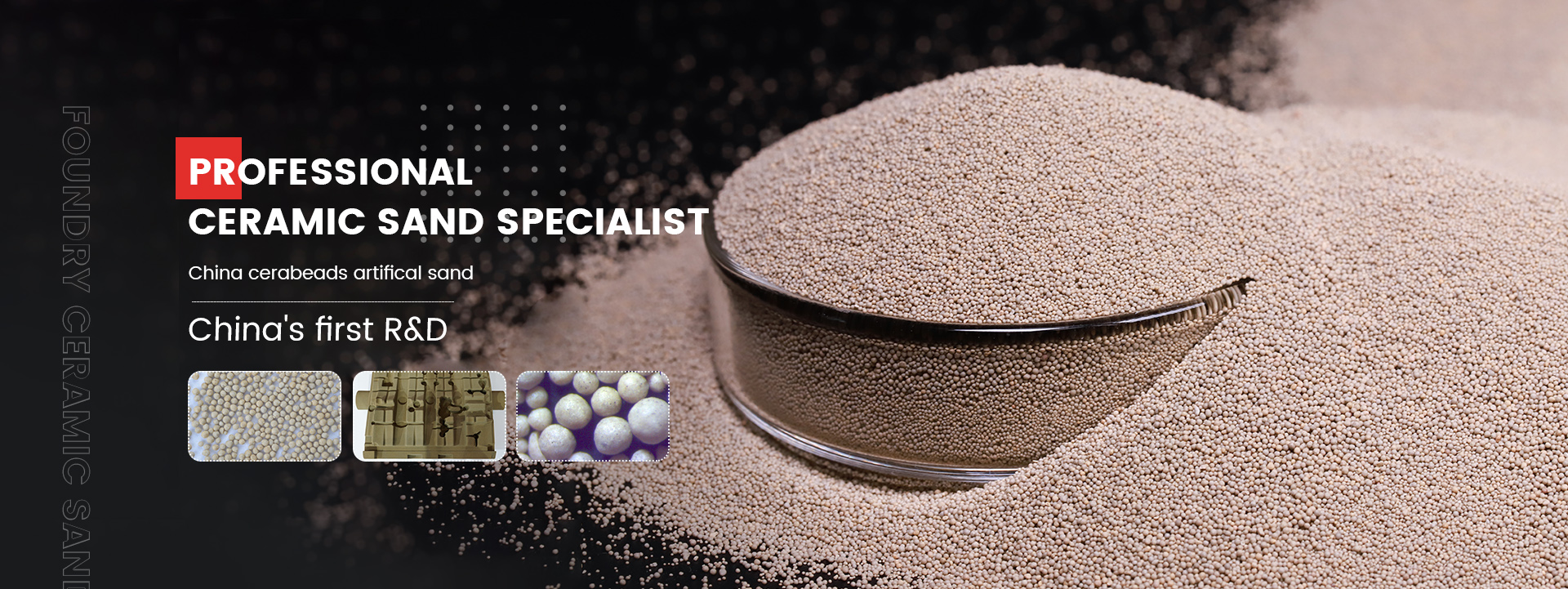
The sand casting process consists of several key steps
1. Pattern Making A pattern, usually made from wood or metal, is created in the shape of the desired final product. This pattern will be used to shape the sand mold.
2. Mold Preparation The sand mixture is packed around the pattern to form two halves of the mold. The pattern is then removed, leaving a cavity in the sand that replicates the desired shape.
3. Core Making If the part requires internal cavities, cores made from sand are created and placed inside the mold.
4. Pouring Molten metal is poured into the mold cavity through a pouring system, filling the space formed by the pattern.
5. Cooling After the metal has cooled and solidified, the mold is broken apart to retrieve the cast part.
6. Finishing The cast part may require additional processes, such as machining, to achieve the desired surface finish and dimensional accuracy.
Conclusion
Sand casting services provide a reliable, efficient, and adaptable way to manufacture metal parts for various applications. Its combination of cost-effectiveness, versatility, and ability to produce complex geometries makes it a favored choice among manufacturers. Whether for industrial use or artistic purposes, sand casting remains a fundamental method in the world of metal fabrication, highlighting its enduring significance in modern production practices. As technology continues to evolve, sand casting services are likely to adapt and improve, further enhancing their role in the manufacturing sector.
Post time:9 月 . 22, 2024 21:18
Next:coated sand casting