Understanding Sand Casting Types of Sand Used in the Process
Sand casting is one of the oldest and most versatile methods of metal casting, widely used across various industries such as automotive, aerospace, and manufacturing. The process involves creating a mold from sand, which is then filled with molten metal to create a desired shape. The quality of the final product heavily relies on the type of sand used in the casting process. In this article, we will explore the different types of sand used in sand casting and their unique properties.
1. Silica Sand
Silica sand is the most commonly used sand type in sand casting. Composed mainly of quartz, it possesses excellent thermal stability and permeability, making it suitable for creating intricate and detailed molds. The grains of silica sand are relatively uniform, which contributes to a smooth surface finish on the casted parts. However, silica sand generates dust, which poses health risks if inhaled, making proper handling and respiratory protection essential.
2. Green Sand
Green sand is a mixture of silica sand, clay, and water. This type of sand is called green not because of its color, but due to its moisture content. Green sand molds are highly malleable, allowing for easy shaping and the replication of complex designs. The clay in the mixture acts as a binding agent, ensuring that the mold holds its shape during the casting process. Green sand is particularly popular for producing large quantities of castings due to its cost-effectiveness and reusability; the sand can be reclaimed and reused after the casting is complete.
3. Resin Sand
sand casting sand types
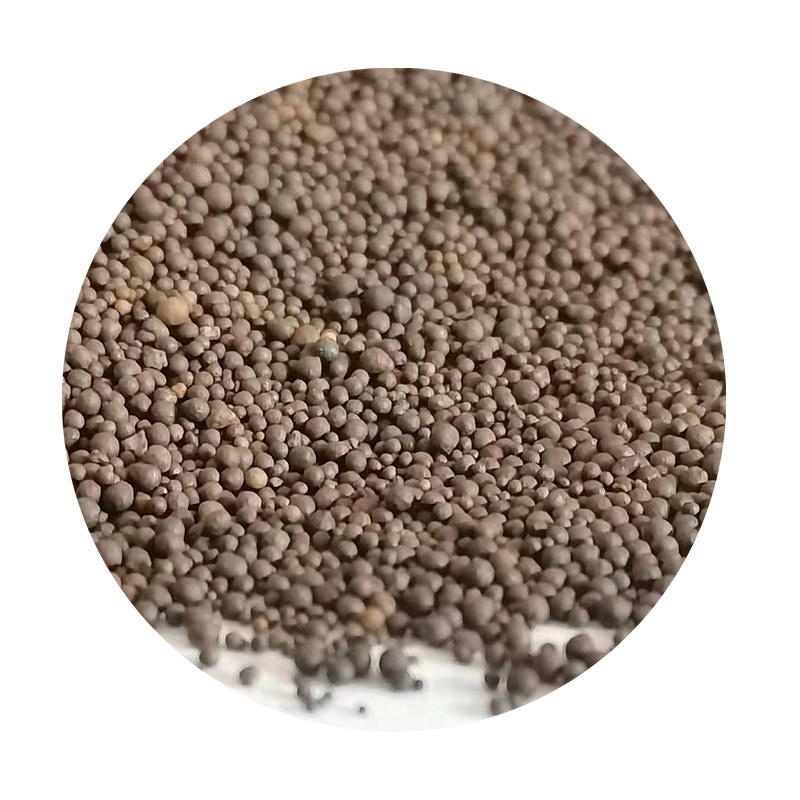
Resin sand is created by mixing silica sand with a thermosetting resin binder. This type of sand is known for its superior strength and dimensional accuracy when compared to traditional green sand. The resin hardens when heat is applied, resulting in molds that can withstand high metal pouring temperatures. Resin sand casting is ideal for industries requiring high-precision components, such as aerospace and medical device manufacturing. However, the use of resin sand can be more expensive due to the cost of the resin and the associated processes.
4. Sodium Silicate Sand
Sodium silicate sand, also known as water glass sand, is an eco-friendly option, consisting of silica sand mixed with sodium silicate. This mixture holds its shape without the added water that green sand requires. The binding agent in sodium silicate sand is activated by CO2 gas, causing the sand grains to harden upon exposure. This type of sand is known for producing molds with excellent surface finishes, making it suitable for casting small and intricate parts. Moreover, sodium silicate sand is reusable and generates less waste compared to other sand types.
5. Chromite Sand
Chromite sand is derived from chromium ore and is known for its high thermal conductivity and resistance to thermal shock. This type of sand is particularly beneficial for creating molds that will be subject to high-temperature metal pours. Chromite sand is often used in the foundry industry for casting ferrous metals and is preferred for its ability to impart a smooth finish on the final product. Its unique properties also help in reducing defects associated with thermal expansion.
Conclusion
Each type of sand used in sand casting has its own set of characteristics and applications. The choice of sand type depends on various factors, including the specific requirements of the casting process, cost considerations, and desired properties of the final product. Understanding these different sand types enables manufacturers to optimize their casting processes and produce high-quality metal components tailored to their clients’ needs. Whether employing silica sand for general use or opting for specialized sands like resin or chromite sand, the proper selection of sand plays a crucial role in the overall success of sand casting operations.
Post time:12 月 . 11, 2024 08:45
Next:Exploring 3D Printing Techniques Using Sand for Innovative Fill Solutions