Sand Casting Procedure A Comprehensive Overview
Sand casting is one of the oldest and most widely used metal casting processes. It involves creating a mold from a sand mixture to shape molten metal into desired forms. This technique has proven to be efficient and cost-effective for producing complex shapes and large parts. In this article, we will delve into the detailed procedure of sand casting, highlighting its key steps, materials, and essential considerations.
Step 1 Pattern Creation
The first step in the sand casting process is the creation of a pattern. A pattern is a replica of the final product, typically made from materials like wood, metal, or plastic. It is crucial that the pattern is slightly larger than the desired final product, accounting for shrinkage that occurs as the molten metal cools and solidifies. Patterns can be made in various styles solid patterns, split patterns, or expandable patterns, depending on the complexity of the part being cast.
Step 2 Mold Preparation
Once the pattern is ready, the next step involves preparing the mold. This is accomplished by packing sand around the pattern. The sand used in sand casting consists of fine, granular silica mixed with a bonding agent, usually clay or resin. The mixture is moistened to improve its cohesiveness.
There are two types of molds in sand casting green sand molds, which use moist sand and are reusable, and dry sand molds, which use a sand mixture that is heated and hardens as it cools. Regardless of the type, the sand needs to be compacted tightly around the pattern to create a strong and stable mold.
Step 3 Core Making
For more complex castings that require internal features or cavities, cores are used. Cores are made from sand mixtures and are placed in the mold to form these internal shapes. Similar to the primary mold, the cores need to be designed with proper ventilation to allow gases to escape during the pouring of molten metal.
Step 4 Mold Assembly
sand casting procedure
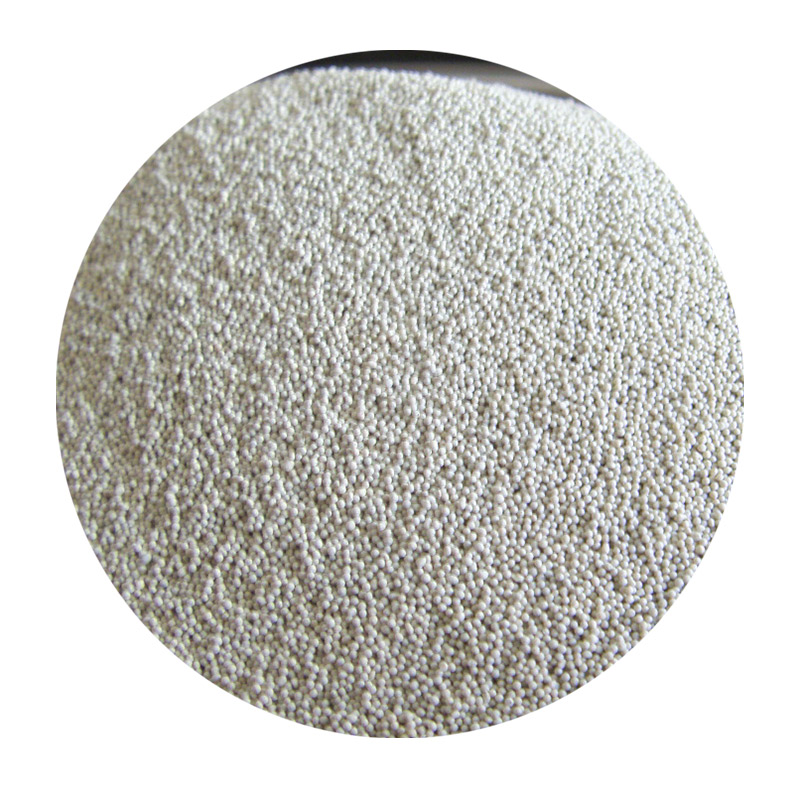
After preparing the mold and cores, the next step involves assembling them. This step requires careful alignment of the mold halves to ensure that the design specifications are met and that there are no gaps where molten metal can leak or incorrectly fill the mold.
Step 5 Pouring the Metal
With the mold assembled and ready, molten metal is poured into it. The type of metal used varies widely depending on the casting application, but common metals include aluminum, iron, and brass. The pouring temperature depends on the metal's melting point, and it is crucial to achieve a uniform temperature for optimal results.
Care must be taken during the pouring process to prevent defects such as air pockets, inclusions, or cold shuts. Proper pouring techniques and equipment, including ladles and pouring shrouds, can help to manage the flow of molten metal effectively.
Step 6 Cooling and Solidification
Once the molten metal is poured into the mold, it is allowed to cool and solidify. The cooling time varies based on the type of metal and the thickness of the casting. It is essential to monitor the cooling process to avoid issues like cracking or warping, which can lead to defects in the final product.
Step 7 Mold Removal and Finishing
After the metal has cooled, the mold is broken away, and the casting is removed. This step may involve breaking or shaking out the mold material. Once the metal piece is free, it often requires additional finishing processes to achieve the desired surface finish and dimensions. These may include machining, grinding, or sandblasting, depending on the application.
Conclusion
Sand casting is a versatile and effective method for producing a wide range of metal components. Its detailed procedure, from pattern creation to finishing, requires careful consideration at each step to ensure high-quality results. As industries continue to evolve, sand casting remains a popular choice for manufacturers looking to create complex designs while maintaining cost efficiency and precision. Through advancements in technology and materials, the future of sand casting is bright, promising improved capabilities and further innovations in metal casting processes.
Post time:9 月 . 28, 2024 12:47
Next:3d sand casting