Understanding Sand Casting A Comprehensive Overview
Sand casting, also known as sand molded casting, is one of the oldest and most widely used metal casting processes. It involves creating a mold from a mixture of sand and a binder, into which molten metal is poured to produce a specific component. This method has been utilized for centuries due to its adaptability, cost-effectiveness, and capability to produce complex shapes with great precision.
Understanding Sand Casting A Comprehensive Overview
Creating the mold involves a process called ramming, where the sand mixture is tightly packed around a pattern that resembles the final product. Patterns can be made from various materials, including wood, metal, or plastic, and are often larger than the final piece to account for shrinkage as the metal cools. After the mold halves are prepared, they are assembled, and any necessary cores—shaped sand structures used to create internal cavities—are added.
sand casting 101
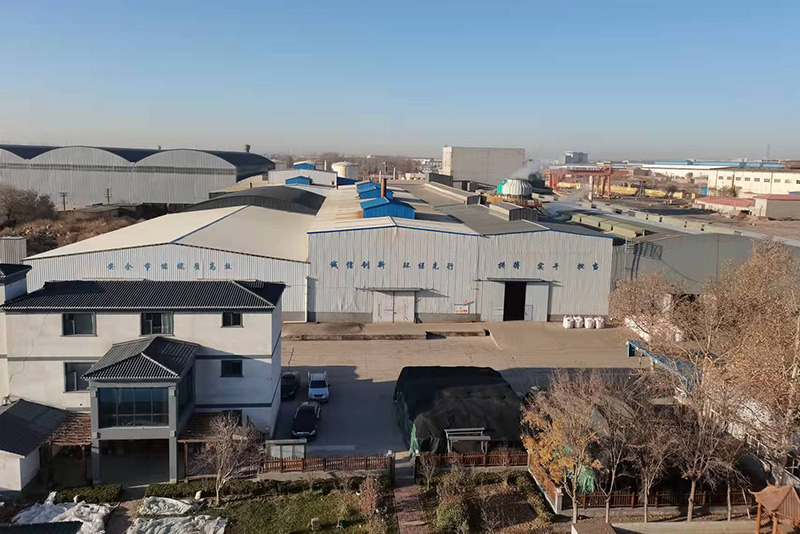
Once everything is in place, the molten metal is poured into the mold through a sprue. The high-temperature metal fills the cavity, taking on the shape defined by the mold. Cooling time varies depending on the type of metal used and the size of the casting, but once solidified, the mold is broken away to reveal the finished part. This can be done through various methods, including hand-breaking or using a vibration technique to loosen the sand.
One of the significant advantages of sand casting is its versatility. It can accommodate a wide range of metals, including iron, aluminum, and bronze. The process is also capable of producing both small and large components, making it suitable for everything from small machine parts to large components for the automotive and aerospace industries. Additionally, sand casting can yield intricate designs, allowing manufacturers to produce complex shapes with varying wall thicknesses, unlike other mass production methods.
Despite its many benefits, sand casting does have some limitations. The surface finish of sand castings is generally rough compared to other casting methods, which may require additional machining or finishing processes to meet aesthetic and functional requirements. The dimensional accuracy of sand castings can also be less precise than other techniques, particularly for very intricate or tight-tolerance applications.
In conclusion, sand casting remains a key process within the manufacturing sector for its unique advantages and wide applicability. As technology progresses, advancements in sand casting techniques, including 3D printing patterns and more efficient binder systems, continue to enhance its efficiency and effectiveness, ensuring its relevance in modern manufacturing. Whether for prototyping or mass production, sand casting is a foundational technique that demonstrates the enduring importance of traditional metalworking methods in contemporary engineering.
Post time:10 月 . 31, 2024 21:02
Next:Innovative Techniques in Ceramic Sand Casting for Enhanced Molding and Casting Performance