Resin Coated Sand Suppliers An Essential Component in Modern Foundries
In the ever-evolving landscape of manufacturing and foundry processes, resin-coated sand has emerged as a vital component in the production of high-quality metal castings. This specialized sand is used for casting processes, primarily due to its superior strength, dimensional stability, and ability to produce intricate shapes. The demand for resin-coated sand has led to a rise in suppliers that cater to foundries across various industries. In this article, we will explore the role of resin-coated sand suppliers, the benefits of resin-coated sand, and key considerations for foundries when selecting a supplier.
Understanding Resin-Coated Sand
Resin-coated sand is created by covering silica sand with a resin, typically composed of phenolic or urethane compounds. This process enhances the sand's properties, allowing it to withstand the rigors of the casting process. One of the primary benefits of resin-coated sand is its ability to maintain the desired shape of the mold without deforming during the pouring of molten metal. This translates to higher precision in the final product, reducing the need for post-casting machining, which otherwise would add to production costs and time.
The Role of Suppliers
Suppliers of resin-coated sand are critical to the foundry industry. They not only provide the necessary materials but also offer expertise and support to their customers. A reliable supplier can be a partner in ensuring that the foundry's processes run smoothly. This includes providing timely deliveries, consistent material quality, and technical support when required.
Moreover, many suppliers are investing in research and development to create new formulations of resin-coated sand that can enhance performance further. As foundries demand more from their materials, such as improved thermal resistance or reduction in emissions, suppliers are adapting and innovating to meet these needs.
Benefits of Resin-Coated Sand
resin coated sand suppliers
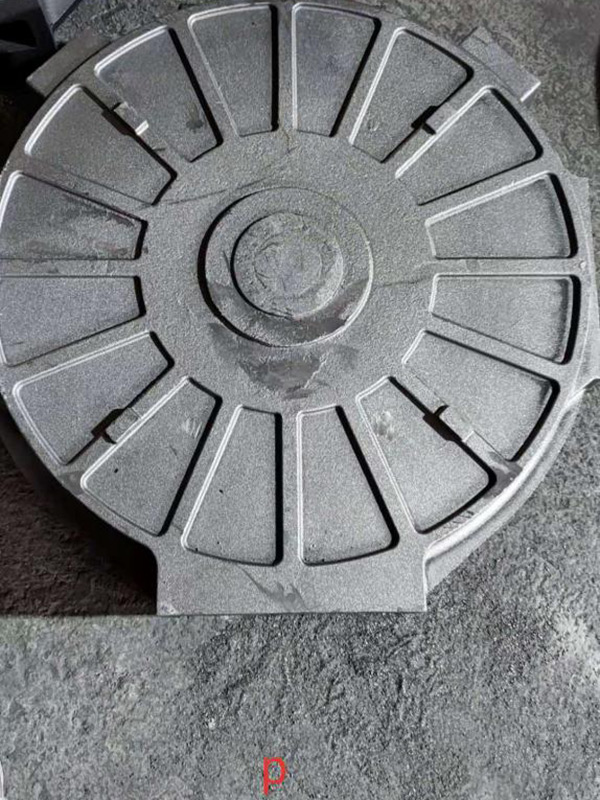
2. Versatility This type of sand can be used in various casting processes, including shell molding and no-bake processes, making it suitable for diverse applications.
3. Reduced Defects The superior mechanical properties reduce the chances of defects such as sand burn-on, which can occur with traditional sands during the casting process.
4. Environmentally Friendly Options Many suppliers are now offering eco-friendly resin-coated sands that reduce volatile organic compounds (VOCs) emissions, aligning with the industry’s movement toward sustainability.
Selecting the Right Supplier
For foundries looking to source resin-coated sand, several factors should be considered when selecting a supplier. It is crucial to evaluate the supplier's reputation and market experience. Established suppliers often have a proven track record of quality and reliability. Additionally, the range of products offered, technical support, and the ability to customize solutions for specific casting needs are vital considerations. Finally, price should also be a factor, but it should not be the sole determining factor; quality and service are equally important.
In conclusion, resin-coated sand suppliers play a pivotal role in the foundry industry. They provide essential materials that enable the production of high-quality castings while contributing to advancements in material technology. As foundries continue to evolve, the partnership with the right supplier will be crucial for maintaining competitiveness and meeting the demands of an increasingly complex marketplace.
Post time:10 月 . 04, 2024 12:01
Next:foundry sand definition