Precision Sand Casting An Essential Technique for High-Quality Metal Components
Precision sand casting is a manufacturing process that plays a pivotal role in producing high-quality metal components. This method utilizes a sand mold to accurately replicate intricate designs and features, making it a preferred choice in various industries such as automotive, aerospace, and machinery manufacturing. The process combines traditional casting techniques with modern technology to achieve superior results in both accuracy and efficiency.
Understanding the Process
The precision sand casting process begins with the creation of a pattern, typically made from metal, wood, or plastic. This pattern serves as a replica of the final component and is used to create the sand mold. The pattern is placed in a molding box, and sand is packed around it, often mixed with a binder to enhance strength and stability. After the sand is compacted around the pattern, the mold is carefully opened, and the pattern is removed, leaving a detailed cavity that reflects the desired component's shape.
Once the mold is complete, molten metal is poured into the cavity. The choice of metal is crucial; materials such as aluminum, cast iron, and brass are commonly used due to their excellent casting properties. After cooling, the mold is broken away, revealing the cast component, which often requires additional finishing processes like machining, grinding, or surface treatment to achieve the desired quality and specifications.
Advantages of Precision Sand Casting
One of the most significant advantages of precision sand casting is its versatility. This method can produce complex geometries and intricate designs that might be challenging to achieve with other manufacturing methods. Additionally, the use of sand allows for the production of large components that require considerable weight tolerance, which is often essential in industrial applications.
Moreover, precision sand casting is particularly cost-effective for low to medium production runs
. The initial investment in tooling is relatively low compared to other methods like die casting or investment casting, making it an ideal choice for prototype development or small batch production. Additionally, the flexibility of the process allows for rapid adjustments, enabling manufacturers to tailor designs quickly based on customer feedback or performance testing.precision sand casting
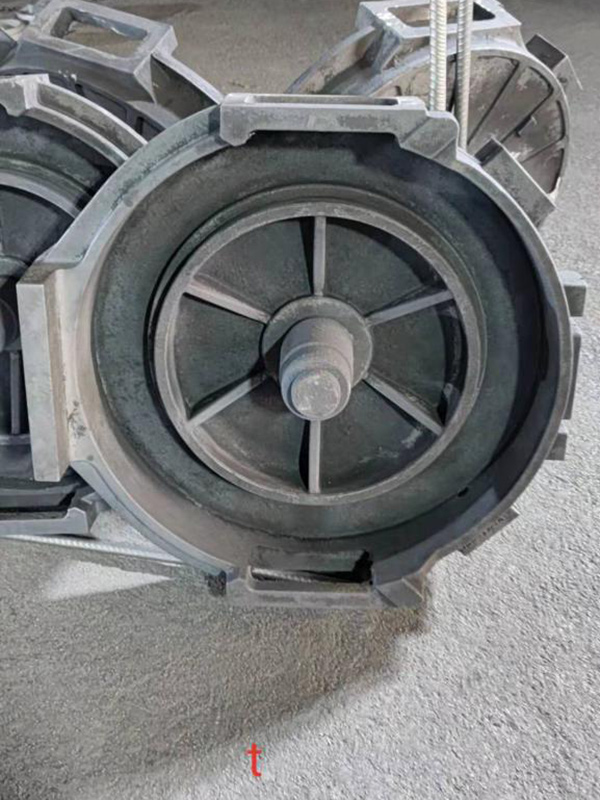
Precision and Surface Finish
The precision aspect of sand casting is significantly enhanced through careful control of the process. Modern advancements in technology, such as computer-aided design (CAD) and computer numerical control (CNC) machines, have improved the accuracy of patterns and molds. This ensures that the final products meet stringent tolerances required by many industries. The ability to produce castings with impressive dimensional accuracy reduces the need for extensive post-processing, which saves time and costs.
Surface finish is another critical factor in precision sand casting. Advanced techniques such as sandblasting, shot peening, and polishing can be employed to achieve the desired surface quality. Additionally, the choice of sand type and grain size can also influence the surface roughness of the final product, allowing manufacturers to fine-tune their processes according to the specific requirements of their customers.
Applications in Various Industries
Precision sand casting is employed across several sectors due to its adaptability and efficiency. In the automotive industry, it is utilized for making engine blocks, transmission housings, and various other components that require high strength and intricate details. In aerospace, precision castings are critical for producing lightweight yet durable parts that can withstand extreme conditions.
Furthermore, the industrial machinery sector relies heavily on precision sand casting for equipment parts, fittings, and fixtures. The ability to create customized components quickly and efficiently makes this method particularly useful in a market that demands rapid turnaround times and high-quality outputs.
Conclusion
In conclusion, precision sand casting stands out as a vital manufacturing process that combines accuracy, versatility, and cost-effectiveness. As industries continue to evolve and the demand for high-quality components increases, this method will undoubtedly play a crucial role in meeting these challenges. With ongoing advancements in technology and materials, precision sand casting is poised to remain a cornerstone of modern manufacturing, providing solutions that cater to the ever-growing needs of diverse sectors.
Post time:11 月 . 30, 2024 06:10
Next:Exploring the Benefits of Sand Casting in Modern Foundry Practices