Foundry Sand Specifications A Comprehensive Guide
Foundry sand is a crucial material in the metal casting industry, used to create molds and cores for shaping molten metal into desired forms. The specification of foundry sand plays a vital role in determining the quality of the cast products. Understanding the standards and characteristics of foundry sand can significantly impact the efficiency of foundry operations and the performance of the final castings. This article outlines the primary specifications of foundry sand, including its types, properties, and testing methods.
Types of Foundry Sand
There are primarily three types of sand used in foundries silica sand, zircon sand, and chromite sand. Among these, silica sand is the most common due to its availability and cost-effectiveness. Silica sand consists primarily of silicon dioxide (SiO2) and can be found in varying grades, ranging from fine to coarse particles. The grain shape, size distribution, and roundness of the sand grains influence the mold's strength and permeability.
Zircon sand, derived from zirconium silicate, is known for its high thermal stability and refractoriness. Although it is more expensive, its unique properties make it suitable for casting high-temperature metals. Chromite sand, another specialized sand, is used for ferrous and non-ferrous metal castings. It provides a lower thermal expansion rate and excellent resistance to metal penetration, making it ideal for precision casting applications.
Key Properties of Foundry Sand
The properties that are essential for foundry sand can be classified into mechanical, thermal, and chemical characteristics
1. Grain Shape and Size The shape of the sand grains affects the mold's strength and its ability to withstand the pressure of molten metal. Angular grains provide better interlocking, enhancing the strength of the mold. The grain size distribution is critical too; a well-graded sand can fill gaps efficiently, leading to better mold integrity.
2. Permeability This refers to the sand's ability to allow gases to escape during the pouring of metal into the mold. Adequate permeability prevents defects like gas porosity in the castings. It is influenced by grain size, shape, and the binding materials used.
3. Thermal Conductivity Foundry sand must possess good thermal conductivity to facilitate the heat dissipation of molten metal. This property affects the cooling rates, influencing the microstructure and mechanical properties of the final product.
foundry sand specifications
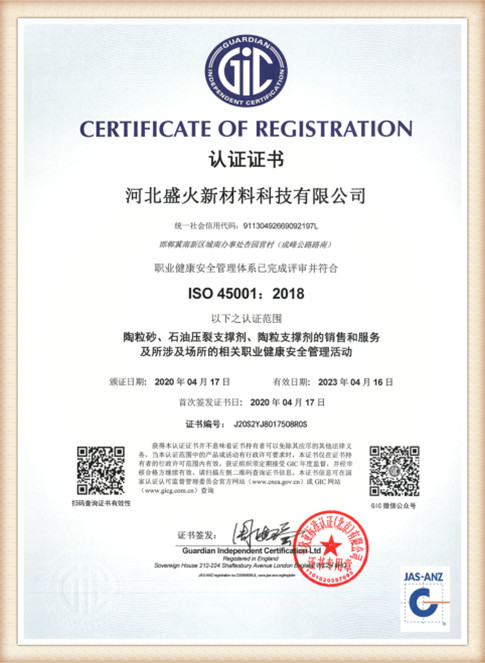
4. Moisture Content Maintaining an optimal moisture level in sand is crucial for effective molding. Too much moisture can lead to steam generation during casting, resulting in defects such as blowholes, while too little can make molds prone to cracking.
5. Chemical Composition The presence of impurities can negatively affect the quality of castings. For example, iron content in silica sand should be minimal, as it can alter the chemical properties of the molten metal. Understanding the chemical makeup is essential for maintaining the desired characteristics of the final product.
Testing Methods for Foundry Sand
To ensure that foundry sand meets the necessary specifications, various testing methods are employed
- Sieve Analysis This test determines the grain size distribution of the sand, ensuring it meets the specifications for mold making.
- Permeability Testing By employing standardized permeability tests, foundries can measure the sand's ability to allow gases to escape, which is essential for preventing casting defects.
- Moisture Content Analysis Regular checks for moisture content help in maintaining the ideal conditions necessary for molding activity.
- Green Compression Strength This test assesses the strength of the sand when it is in a moist state, providing insights into how the mold will perform under the pressure of molten metal.
Conclusion
In conclusion, the specifications of foundry sand are of paramount importance for the efficiency and quality of metal casting processes. Understanding the different types of foundry sand, their key properties, and the associated testing methods enables foundries to optimize their operations and produce high-quality castings. As the foundry industry continues to evolve, adhering to these specifications will ensure excellence in manufacturing and contribute to the advancement of technology in casting applications.
Post time:10 月 . 11, 2024 17:31
Next:Achieve Flawless 3D Prints with a Smooth Finish and No Sanding Required