The Dry Sand Casting Process A Comprehensive Overview
Dry sand casting, also known as green sand casting, is a traditional metal casting process that has been employed in various industries for centuries. This method primarily utilizes dry sand as the mold material, offering a unique combination of advantages and challenges for manufacturers. As the demand for precision components continues to grow across automotive, aerospace, and machinery sectors, understanding the dry sand casting process becomes increasingly important.
The Basics of Dry Sand Casting
In dry sand casting, the mold is created using a mixture of sand, clay, and water, where the sand is typically a fine grain and is classified as dry due to the low moisture content. The sand mixture is compacted around a pattern that represents the object to be cast. Once the mold is formed, it is baked in an oven to harden, producing a rigid mold that can withstand the molten metal's heat. The main ingredients in dry sand casting include
1. Sand The primary material, usually silica, provides the bulk structure for the mold. 2. Clay Acting as a binder, clay helps in holding the sand grains together. 3. Water Although minimal, water aids the clay's binding ability and affects the sand's properties.
The Dry Sand Preparation Process
The preparation of dry sand involves mixing the sand with a specific percentage of clay and water. The optimal ratio is crucial; too much water can lead to mold deformation, while too little can result in poor binding and mold integrity. The mixture is then processed to ensure uniformity, which is key to achieving high-quality molds.
Once prepared, the sand is meticulously packed around the pattern. Energy is applied to compact the sand, ensuring that it takes the shape of the pattern accurately. After packing, the mold is typically subjected to heat, which hardens the sand through the bonding action of the clay. The curing process enhances the mold's strength and stability, making it capable of withstanding high temperatures during pouring.
Pouring and Metal Solidification
dry sand casting process
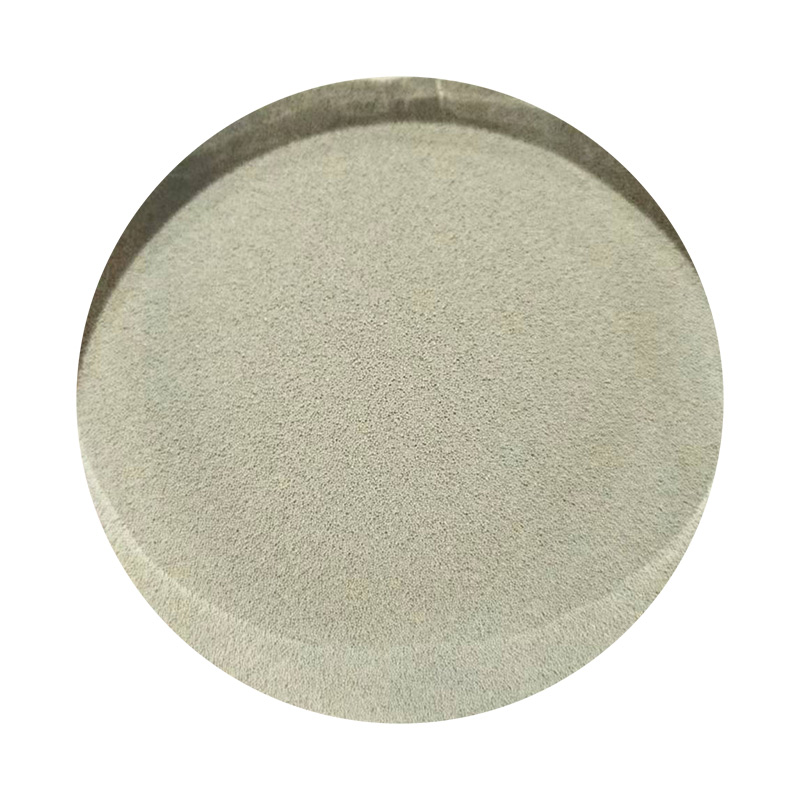
After the mold has hardened, it's ready for metal pouring. The mold halves are assembled, and molten metal is carefully poured into the cavity formed by the mold. Once the metal cools and solidifies, the mold is broken open to reveal the casting. The time taken for this process can vary based on the metal used, the size of the casting, and the cooling rate.
Advantages of Dry Sand Casting
The dry sand casting process offers several advantages that make it a popular choice for many applications
1. High Surface Finish The dry sand provides a smoother finish compared to traditional green sand casting, reducing the need for further machining. 2. Temperature Resistance Hardened dry sand molds can withstand higher pouring temperatures, making them suitable for various metals. 3. Reusability Molds can be reused multiple times, depending on the design and intricacy of the casting. 4. Accuracy The higher density of dry sand molds allows for more precise dimensions and reduces the potential for defects in the final product.
Challenges and Limitations
Despite its advantages, dry sand casting is not without challenges. The process can be labor-intensive, requiring skilled labor for both the preparation of the molds and the metal pouring. Additionally, the cost of raw materials for dry sand casting can be higher than that of other methods, such as green sand casting. Furthermore, the process may not be suitable for very intricate designs or undercuts, limiting its application in some contexts.
Conclusion
The dry sand casting process is a vital technique in the metal casting industry, providing a balance between quality and efficiency. With its ability to produce high-quality castings, it plays a significant role in the production of components for various industries. While challenges exist, ongoing advancements in technology and materials are expected to enhance the capabilities of dry sand casting, ensuring its relevance in the ever-evolving landscape of manufacturing. Understanding this process not only enriches the knowledge of those in the industry but also opens up pathways for innovation and improvement in metal casting practices.
Post time:11 月 . 20, 2024 17:14
Next:golden sands development