The Difference Between Die Casting and Sand Casting
Casting is a fundamental manufacturing process that involves pouring molten metal into a mold to form desired shapes. Two of the most commonly used casting techniques are die casting and sand casting. Each method has its own unique properties, advantages, and disadvantages, making them suitable for different applications. This article explores the key differences between die casting and sand casting.
Process Overview
Die casting involves forcing molten metal under high pressure into a mold cavity made from metal, typically steel or aluminum. The molds are reusable and designed for high precision, allowing for intricate shapes and excellent surface finishes. This process is primarily used for high-volume production due to its speed and efficiency.
In contrast, sand casting utilizes a mold made from a mixture of sand, clay, and water. The sand mold is generally a one-time use, and the process involves creating a pattern of the object in the sand, removing the pattern, and then pouring molten metal into the cavity. While it is slower and often less precise than die casting, sand casting is more versatile and can accommodate a wider variety of materials.
Material Limitations
One of the significant differences between the two methods lies in the types of metals that can be used. Die casting is best suited for non-ferrous metals such as aluminum, zinc, and magnesium, offering high strength-to-weight ratios and great corrosion resistance. These metals can withstand high pressures, making die casting ideal for automobile and electronic parts.
On the other hand, sand casting can be used with a broader range of materials, including ferrous metals like cast iron and steel, as well as non-ferrous metals. This versatility allows sand casting to be utilized for various applications, including engine blocks, large castings, and complex shapes.
difference between die casting and sand casting
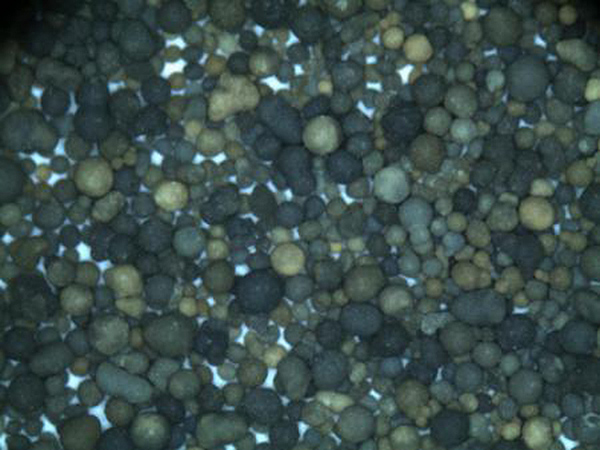
Cost Considerations
The cost structure of die casting and sand casting also differs significantly. Die casting requires heavy initial investments in mold production, which can be expensive due to the precision and durability required. However, for high-volume production runs, the cost per unit decreases significantly, making die casting economically favorable in such scenarios.
Conversely, sand casting generally has lower initial costs, as the molds can be made quickly and do not require the same level of precision. However, the cost per unit remains relatively high for low-volume production due to longer lead times and labor intensiveness. It is often more economical for smaller production runs and larger parts.
Surface Finish and Tolerance
Another critical distinction lies in the surface finish and tolerances achievable by each method. Die casting typically results in better surface finishes and tighter tolerances due to the nature of the tooling and the precision of the process. This makes die casting suitable for parts that require a smooth appearance and precise dimensions.
In contrast, sand casting tends to produce rougher surfaces and less precise dimensions. While subsequent machining can improve the finish and tolerances, it adds to the manufacturing time and cost. Thus, sand casting is often chosen for applications where the final part does not need high cosmetic or dimensional precision.
Conclusion
In summary, the choice between die casting and sand casting depends on several factors including the application, material requirements, production volume, and budget. Die casting excels in high-volume production of intricate, precise parts with non-ferrous metals, while sand casting offers versatility and is better suited for larger, simpler shapes, especially with ferrous metals. Understanding these differences can help manufacturers make informed decisions about which casting method to employ for their projects.
Post time:11 月 . 29, 2024 23:19
Next:Understanding the Properties and Applications of Sand Cast Iron in Modern Manufacturing