Understanding the Density of Foundry Sand
Foundry sand plays a crucial role in the metal casting industry, serving as a fundamental component in the production of metal parts. The properties of foundry sand, particularly its density, are essential in determining its suitability for various casting processes. In this article, we will delve into the significance of foundry sand density, how it is measured, and its impact on casting quality.
What is Foundry Sand?
Foundry sand is a high-quality silica sand that is used in the casting process. It is specifically designed for molding and core-making applications in foundries. The primary function of foundry sand is to form the mold cavity that shapes the final product. Due to its ability to withstand high temperatures and its excellent refractory properties, foundry sand is a preferred material for many casting methods, including green sand casting, air set sand casting, and resin-coated sand casting.
Importance of Density
Density, defined as mass per unit volume, is a critical property of foundry sand. The density of sand influences its flowability, compaction, and thermal stability during the casting process. A higher density generally enhances the strength and integrity of the mold, while a lower density may lead to defects such as sand erosion or mold collapse.
Moreover, the density of foundry sand affects the specific gravity of the mold, which in turn influences the cooling rates of the molten metal. For instance, a denser sand mix can absorb more heat, prolonging the time it takes for the metal to cool, thus allowing for better casting detail and minimizing the chances of thermal shock. In contrast, lighter sands may lead to faster cooling, potentially resulting in inferior surface finishes or internal defects due to inconsistent cooling rates.
density of foundry sand
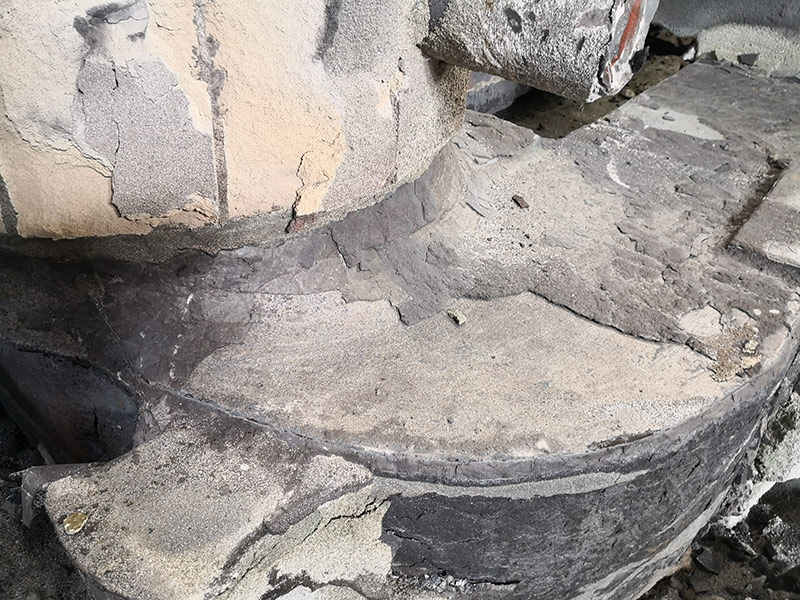
Measuring Density of Foundry Sand
The density of foundry sand can be measured using several methods. One common approach involves measuring the weight of a known volume of dry sand. This can be done using a volumetric flask or a specific density measurement apparatus. The mass is recorded, and the density is calculated by dividing the mass by the volume.
Another method, which can provide more detailed information about the sand's characteristics, is the use of specialized equipment that can assess the bulk density and specific gravity under various conditions. This helps in determining how the sand behaves when subjected to different processes in casting.
Factors Affecting Density
Several factors can influence the density of foundry sand. The grain shape, size distribution, moisture content, and the additives used in the sand mixture all play a significant role. Spherical grains, for example, tend to pack more efficiently, resulting in a higher density compared to angular grains. Similarly, adding binders can increase the overall density of the sand mixture, which may enhance its performance during casting.
Conclusion
In conclusion, the density of foundry sand is a vital attribute that influences the quality and efficiency of the metal casting process. Understanding and controlling the density of foundry sand can significantly improve the casting's integrity and surface quality. For foundries aiming to enhance their casting processes, regular monitoring and adjustment of sand density should be an integral part of their operational protocols. By doing so, they can achieve better product consistency and reduce defects, ultimately leading to more successful casting outcomes.
Post time:9 月 . 22, 2024 10:14
Next:can you sand a 3d print