Custom Sand Casting An Overview
Sand casting, a time-honored metalworking process, has emerged as one of the most versatile and cost-effective methods for producing intricate metal parts. Among its various applications, custom sand casting stands out as a particularly valuable technique, enabling manufacturers to create tailored components that meet specific design requirements. With its adaptability and efficiency, custom sand casting is increasingly favored in various industries, ranging from automotive to aerospace.
At its core, the sand casting process involves creating a mold from a pattern, which is typically made of metal or plastic. This pattern is shaped to reflect the exact dimensions and details of the desired final product. Once the pattern is prepared, it is placed in a container known as a flask, which is then filled with sand bonded by a binding agent, usually clay. The sand is compacted around the pattern, forming a mold cavity. After sufficient curing time, the sand is removed, revealing the mold.
A crucial advantage of custom sand casting is its adaptability to create complex shapes and sizes, making it ideal for both low and high production runs. Manufacturers can quickly shift from one design to another, minimizing downtime and allowing for rapid prototyping. This flexibility is particularly beneficial in industries that require innovative designs and rapid development cycles.
Another compelling benefit of custom sand casting is the variety of metals that can be cast
. From aluminum and iron to bronze and magnesium, the process accommodates an array of materials, each imparting distinctive mechanical properties to the final product. This versatility allows engineers to select the most appropriate metal for their application, ensuring optimal performance under the specific conditions the component will encounter.custom sand casting
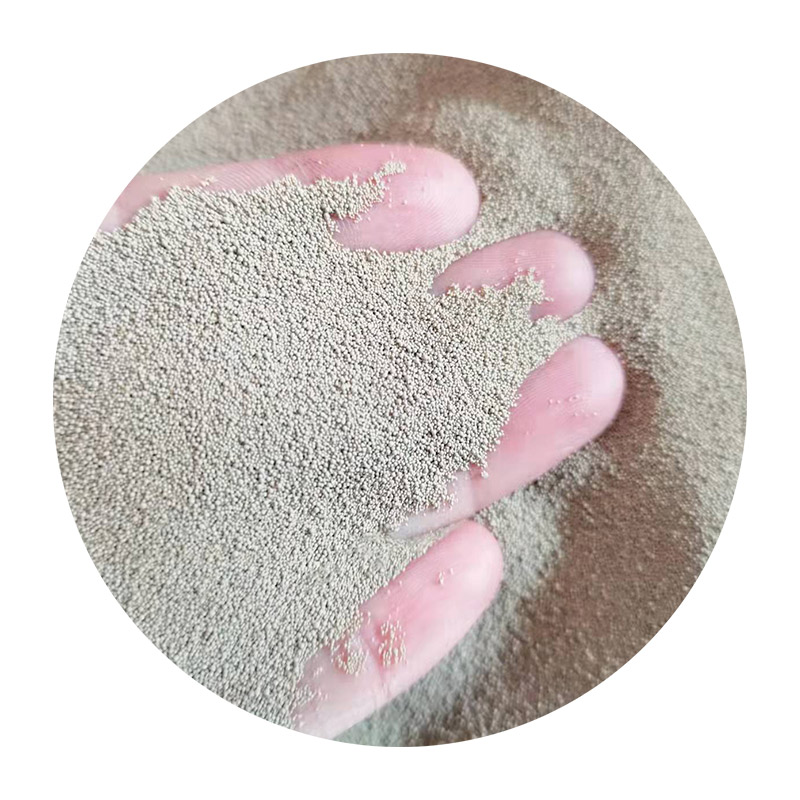
The custom sand casting process also supports intricate design features, such as thin walls, detailed engravings, and internal channels. Utilizing advanced techniques like 3D modeling and computer-aided design (CAD), engineers can create highly detailed patterns that translate to precision molds. As a result, manufacturers can produce components that not only meet functional requirements but also aesthetic considerations.
However, while the benefits of custom sand casting are substantial, there are also challenges to consider. The quality of the mold can significantly influence the final product. Ensuring there are no imperfections, such as inclusions or defects in the mold, is critical for achieving high-quality castings. Additionally, the sand mixture's composition must be carefully controlled to balance strength and flexibility, contributing to mold durability and ease of release.
Moreover, post-casting processes, such as machining and surface finishing, may be necessary to achieve precise tolerances and desired surface characteristics. Although these additional steps can increase production time and costs, they are sometimes unavoidable given the intricacies of custom designs. Consequently, manufacturers often need to strike a balance between the benefits of sand casting and the potential need for further processing.
The economic benefits of custom sand casting cannot be overlooked. Compared to other manufacturing processes, such as die casting or investment casting, sand casting often entails lower tooling costs. This is especially advantageous for small to medium-sized businesses that require low-volume production runs. Therefore, custom sand casting serves as an accessible option for businesses seeking to bring innovative products to market without incurring exorbitant expenses.
In conclusion, custom sand casting is a versatile and effective method for producing high-quality metal components tailored to specific design requirements. Its ability to accommodate complex designs and a variety of metals makes it an invaluable tool across numerous industries. While challenges such as mold quality and post-casting processes exist, the overall benefits, including cost-effectiveness and flexibility, make custom sand casting a preferred choice for manufacturers striving for innovation and excellence. As technology continues to evolve, the potential for advancements in custom sand casting processes promises even greater possibilities for the future of metalworking.
Post time:12 月 . 13, 2024 15:43
Next:3d print sand