The Role of Ceramic Foundry Sand in Modern Casting Processes
In the realm of metalcasting, the selection of foundry materials plays a crucial role in defining the quality and efficiency of the casting process. Among these materials, ceramic foundry sand has emerged as a prominent choice due to its unique properties and benefits over traditional sand materials. This article explores the significance of ceramic foundry sand, its advantages, and its applications in modern casting practices.
Ceramic foundry sand is produced from high-purity minerals, typically consisting of spherical particles that display exceptional thermal and mechanical characteristics. Unlike conventional silica sand, ceramic sand boasts a higher thermal stability, which is vital during the casting process where extreme temperatures are involved. This thermal resistance minimizes the risks of deformity, breakage, and defects during metal solidification, resulting in higher quality castings with improved surface finishes.
One of the standout features of ceramic foundry sand is its excellent flowability. The spherical shape of the grains allows for optimal packing density, which enhances mold filling and improves the overall integrity of the mold. This property is essential for achieving detailed patterns and intricate designs, particularly in complex castings such as automotive components, aerospace parts, and precision toolings. Therefore, manufacturers utilizing ceramic foundry sand can produce castings that meet stringent dimensional tolerances and surface quality requirements.
Another significant advantage of ceramic foundry sand is its reusability. Traditional sand molds often degrade after a few uses, leading to increased material costs and waste generation. In contrast, ceramic sand can be reused multiple times without significant loss of quality or performance. This characteristic not only reduces the overall material expenses for foundries but also contributes to more sustainable practices in the casting industry by minimizing waste.
ceramic foundry sand
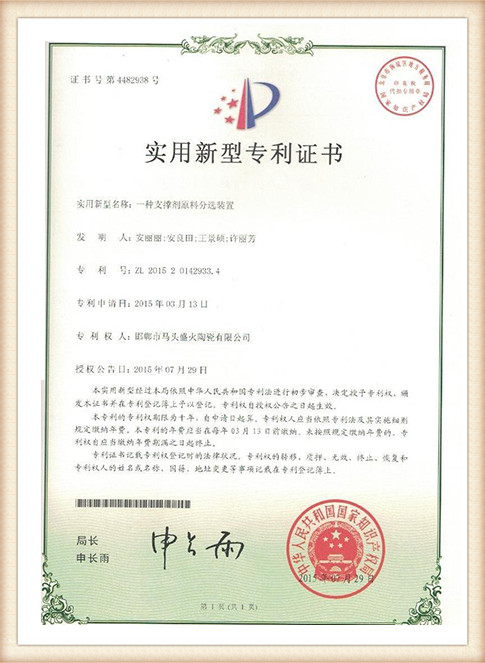
Moreover, ceramic foundry sand enhances the overall productivity of the casting process. Its superior performance leads to shorter cycle times, as the molds can be produced and stripped more efficiently. This speediness not only allows for more castings to be produced within a given timeframe but also enables manufacturers to respond to market demands more rapidly. In a competitive industry, this agility can be a significant competitive advantage.
While the benefits of ceramic foundry sand are substantial, it is essential to consider its cost. The initial investment in ceramic sand may be higher than that of traditional silica sand; however, the long-term savings from increased reusability, reduced defects, and improved casting quality often outweigh this initial expense. Many foundries have found that switching to ceramic sand results in a more cost-effective operation in the long run.
In terms of environmental impact, ceramic foundry sand is a more sustainable option compared to traditional materials. Its longevity and reusability contribute to decreased waste, which is increasingly important in an era leaning towards eco-friendly manufacturing processes. Additionally, ceramic sand does not contain harmful substances that could leach into the environment, aligning with the industry’s movement towards safer and cleaner production techniques.
In conclusion, ceramic foundry sand represents a significant advancement in the casting industry, offering numerous advantages over conventional sand materials. Its superior thermal stability, flowability, reusability, and sustainability make it an ideal choice for modern foundries aiming to enhance their production capabilities. As the demand for high-quality castings continues to rise, the adoption of ceramic foundry sand will likely play a critical role in the evolution of foundry practices, paving the way for innovative approaches and improved outcomes in metal casting.
Post time:11 月 . 25, 2024 04:03
Next:foundry sand used in construction