The Importance of Casting Sand in Metal Production
Casting is a vital process in metal production, serving as a method for shaping and forming metal into desired products and components. At the heart of this process lies casting sand, a crucial material that plays an integral role in the creation of metal castings. Understanding the properties, types, and applications of casting sand can provide insights into its significance in the metallurgical industry.
Casting sand, also known as foundry sand, is primarily composed of silica. Its fine granules and ability to withstand high temperatures make it ideal for use in various casting processes, including sand casting. This method involves creating a mold from sand, which is then filled with molten metal. Once the metal cools and solidifies, the sand mold is broken away to reveal the finished product. The effectiveness of this process largely depends on the quality and characteristics of the casting sand used.
The Importance of Casting Sand in Metal Production
The performance of casting sand is influenced by several factors, including grain size, shape, and distribution. A well-graded sand will consist of a mix of different particle sizes, promoting better mold strength and stability. The roundness of the sand grains also affects how well they pack together, impacting the mold’s ability to hold shape under pressure from the molten metal. Hence, foundry engineers must carefully select and prepare casting sand to meet the specific demands of each casting project.
casting sand for metal
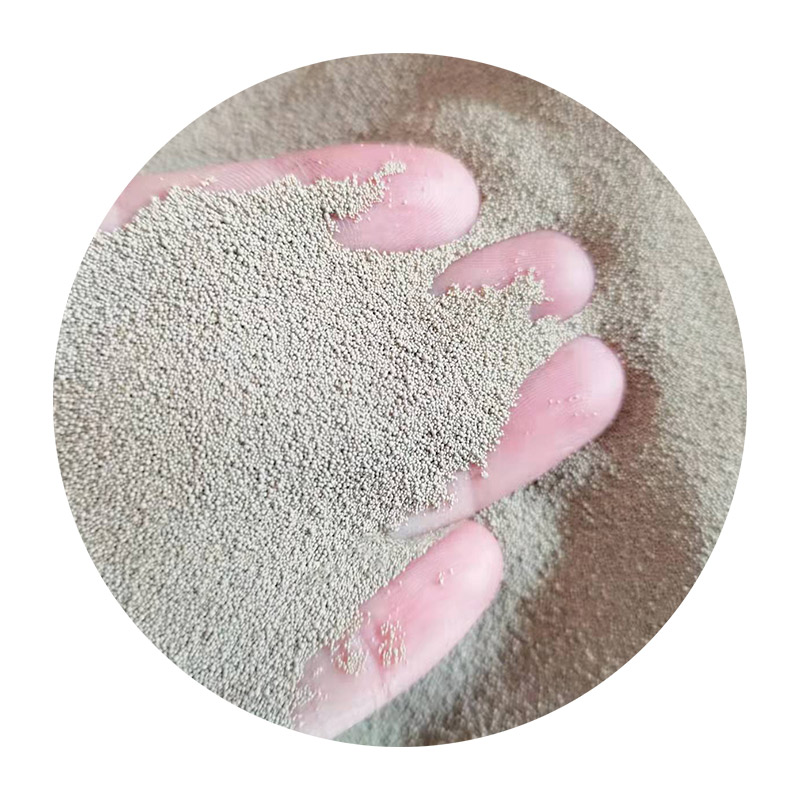
One of the most significant advantages of using casting sand is its reusability. After the casting process, the sand can often be reclaimed, cleaned, and reused for new molds. This not only reduces waste but also lowers material costs, making sand casting a more sustainable option in metal manufacturing. However, the reusability of the sand depends on its treatment and the quality of the castings produced. Properly managed reclamation systems can significantly extend the life of the sand, contributing to both economic and environmental benefits.
Casting sand also plays a critical role in influencing the surface finish and dimensional accuracy of the final metal product. The texture and temperature of the sand can affect the heat transfer during the solidification of the molten metal. A uniform and consistent sand mixture helps produce smoother surfaces and tighter tolerances, which are essential for components used in sensitive applications, such as automotive or aerospace industries.
In recent years, the industry has witnessed innovations in casting sand technology, including the development of eco-friendly binders and casting materials. As the demand for sustainable practices grows, the use of organic materials in the formulation of casting sand is being explored. These advances not only aim to enhance performance but also reduce the environmental impact of foundry operations.
In conclusion, casting sand is a fundamental element in the metal casting process, influencing various characteristics of the final product. Its unique properties, types, and ability to be reused make it an essential material in the metallurgy sector. Continued research and innovation in casting sand technology will further enhance its applications and sustainability, ensuring that it remains a cornerstone of metal production for years to come.
Post time:11 月 . 30, 2024 11:33
Next:Sustainable Solutions for Foundry Sand Recycling and Waste Management Strategies