The Emergence of 3D Printed Sand Casting A Revolution in Manufacturing
In recent years, the manufacturing industry has undergone significant transformations, driven by advances in technology and the quest for more efficient, sustainable production methods. One of the most innovative developments in this arena is 3D printed sand casting, a technique that is reshaping traditional manufacturing practices and offering numerous benefits to industries ranging from automotive to aerospace.
Understanding 3D Printed Sand Casting
At its core, sand casting is a process wherein molten metal is poured into a mold made of sand to create a desired shape. Traditionally, creating these molds required significant time and labor, as each design needed to be crafted manually. However, with the advent of 3D printing technology, sand casting has become far more efficient. Instead of relying on hand-crafted molds, manufacturers can now design complex patterns digitally, which can then be 3D printed using specially formulated sand.
The 3D printing process begins with a digital model of the desired part, created using Computer-Aided Design (CAD) software. This model is then sliced into layers, allowing the 3D printer to build the mold layer by layer. The sand is printed with a binding agent, which allows the particles to stick together and form a solid mold once the printing is complete. This method dramatically reduces the lead time associated with mold creation and allows for more intricate designs that would be difficult or impossible to achieve with traditional methods.
Advantages of 3D Printed Sand Casting
1. Reduced Lead Times One of the most significant benefits of 3D printed sand casting is the reduction in lead times. Traditional molds can take weeks to produce, whereas 3D printed molds can be completed in a matter of hours. This accelerated timeline allows manufacturers to bring products to market faster, enhancing their competitiveness.
3d printed sand casting
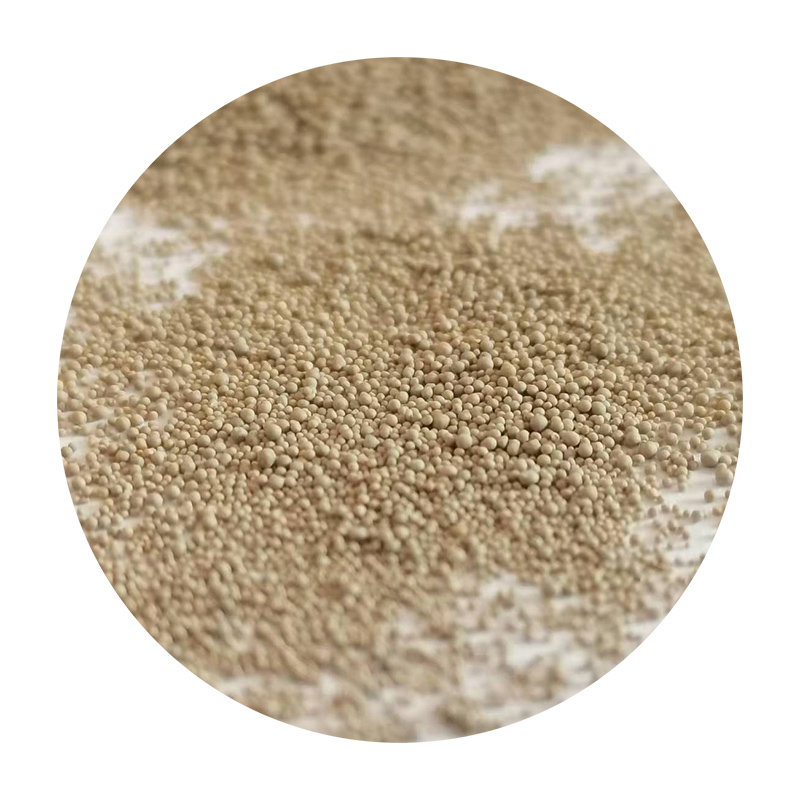
2. Cost Efficiency While the initial investment in 3D printing technology may be substantial, the long-term savings can be significant. By reducing the amount of material waste and enabling more efficient designs, manufacturers can lower production costs. Moreover, the ability to quickly produce molds for small production runs makes it economically viable to test new products without a substantial financial commitment.
3. Design Flexibility The freedom to create complex geometries is another compelling advantage. With traditional sand casting, complex designs often require additional tooling or may be infeasible altogether. However, 3D printing allows for intricate designs, such as lattice structures and lightweight designs, promoting innovations in product development.
4. Sustainability As the world pivots towards sustainable manufacturing practices, 3D printed sand casting presents an environmentally friendly alternative. The process generates less waste compared to traditional methods, and many companies are moving towards using recyclable or biodegradable binding agents. Furthermore, the efficiency of the process contributes to reducing energy consumption.
Challenges and Future Prospects
Despite its numerous advantages, the implementation of 3D printed sand casting does come with challenges. For instance, there may be limitations in the types of materials that can be used, and the initial costs for the required machinery can be high. Additionally, the full market acceptance of this technology requires ongoing education and training for engineers and technicians.
Looking ahead, the future of 3D printed sand casting appears promising. Research and development in materials and printing technologies continue to evolve, enhancing the capabilities and performance of printed molds. As industries increasingly look for efficiencies and ways to innovate, it is likely that 3D printed sand casting will play an integral role in shaping the next generation of manufacturing processes.
In conclusion, 3D printed sand casting represents a significant advancement in manufacturing technology. By marrying traditional casting methods with cutting-edge 3D printing capabilities, manufacturers can enjoy heightened efficiency, cost savings, and creative freedom. As this technology continues to mature, it will undoubtedly drive further innovation across various industries, marking a new era in the world of production and design.
Post time:12 月 . 17, 2024 01:06
Next:different types of foundry sand