Types of Foundry Sand
Foundry sand is a key component in the metal casting industry, providing the necessary properties for creating molds and cores. The selection of suitable sand is crucial, as it directly influences the quality of the final cast product. In this article, we will explore the various types of foundry sand, their characteristics, and their applications.
1. Silica Sand
Silica sand, or quartz sand, is one of the most commonly used foundry sands. It consists primarily of silicon dioxide (SiO2) and is favored for its high melting point and thermal stability. Silica sand can withstand the high temperatures involved in metal casting while maintaining its shape and strength. It offers good permeability, allowing gases to escape during the casting process, which minimizes defects. Additionally, silica sand can be chemically coated to enhance its binding properties.
2. Chromite Sand
Chromite sand is made from the naturally occurring mineral chromite, primarily composed of chromium oxide. It is well-known for its excellent thermal resistance and strength, making it suitable for casting ferrous and non-ferrous metals. One of the significant advantages of chromite sand is its low thermal expansion, which helps minimize shrinkage defects in the final cast products. Chromite sand is often used in the production of high-quality steel and iron castings due to its ability to withstand extreme temperatures.
3. Olivine Sand
Olivine sand is derived from the mineral olivine, a naturally occurring silicate mineral. This type of sand is characterized by its high melting point and is highly resistant to thermal shock. Olivine sand tends to have a greenish color and is often used for casting aluminum, brass, and other non-ferrous metals. Its unique properties, such as low thermal expansion and excellent chemical stability, make it ideal for high-performance applications in foundries.
types of foundry sand
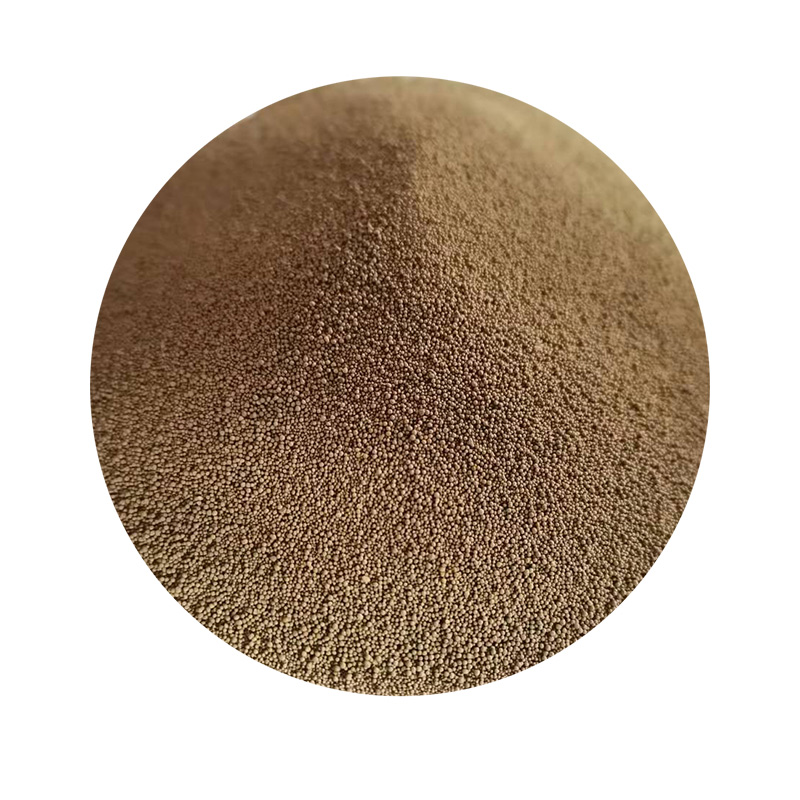
4. Zircon Sand
Zircon sand is composed of zirconium silicate and is recognized for its exceptional refractory properties. Its high melting point makes it suitable for casting metals at high temperatures. Zircon sand also has a low thermal expansion rate, which helps reduce mold and core distortion during the casting process. Additionally, it exhibits excellent resistance to chemical reactions, making it ideal for casting reactive metals like titanium. Due to its premium qualities, zircon sand is typically more expensive than other foundry sands.
5. Coal Dust
Coal dust is often used in the form of a blend with more traditional sands to improve the binding properties of the mold. While not a primary sand type, coal dust helps enhance the strength and thermal stability of the mold during the casting process. The carbon content also aids in the reduction of certain metal oxides, improving the quality of the resulting cast parts. This combination is particularly beneficial in ferrous metal casting applications.
6. Resin-Sand
Resin-sand systems involve a mixture of traditional foundry sand and thermosetting resins. These resins bind the sand grains together, providing increased strength and durability. The primary advantage of resin-sand systems is their ability to produce complex shapes with precision and smooth surface finishes. They are often used in investment casting and in the production of intricate components with tight tolerances.
Conclusion
The choice of foundry sand is crucial for achieving optimal casting results. Each type of sand has its unique set of properties that make it suitable for specific applications in the foundry industry. Silica sand remains the industry standard, while specialized sands like chromite, olivine, zircon, and resin-sand systems offer unique benefits for high-performance casting. As innovation continues to evolve in the foundry industry, the selection of foundry sand will play a pivotal role in enhancing casting quality, efficiency, and overall production capabilities. Understanding the types of foundry sand available allows manufacturers to make informed choices that align with their production needs and objectives.
Post time:Nov . 24, 2024 04:51
Next:foundry sand recycling