The Evolution of Sand Casting Companies Innovations and Trends
Sand casting, one of the oldest and most versatile manufacturing processes, has evolved significantly over the years. As industries diversify and demand for precision grows, sand casting companies are adapting by adopting innovative technologies and refining their processes. This article explores the landscape of sand casting companies, their technological advancements, and the trends shaping the future of this essential manufacturing technique.
Understanding Sand Casting
At its core, sand casting involves creating a mold from sand, which is then used to cast molten metal into a desired shape. It is widely used due to its cost-effectiveness, ability to produce complex shapes, and the variety of metals that can be cast, including aluminum, iron, and bronze. As industries such as automotive, aerospace, and sculpture continue to expand, the demand for sand casting remains robust.
Technological Advancements
Recent innovations have transformed how sand casting companies operate. The introduction of computer-aided design (CAD) and computer-aided manufacturing (CAM) has allowed for greater precision. These tools enable engineers to create detailed designs, which can be directly translated into molds with high accuracy. Moreover, advancements in 3D printing technology are revolutionizing the production of sand molds, reducing lead times and material wastage.
3D printing in sand casting, often referred to as 3D sand printing, allows for the creation of intricate molds that would be difficult or impossible to achieve through traditional methods. This process not only enhances precision but also significantly shortens the production cycle, allowing companies to meet the growing demand for rapid prototyping and low-volume production.
Automated systems are also becoming commonplace in sand casting facilities. Robotic arms are employed for tasks such as pouring molten metal, which minimizes human error and improves safety. Automation solutions streamline production processes, increase efficiency, and allow companies to maintain high standards of quality control.
Sustainability Practices
sand casting companies
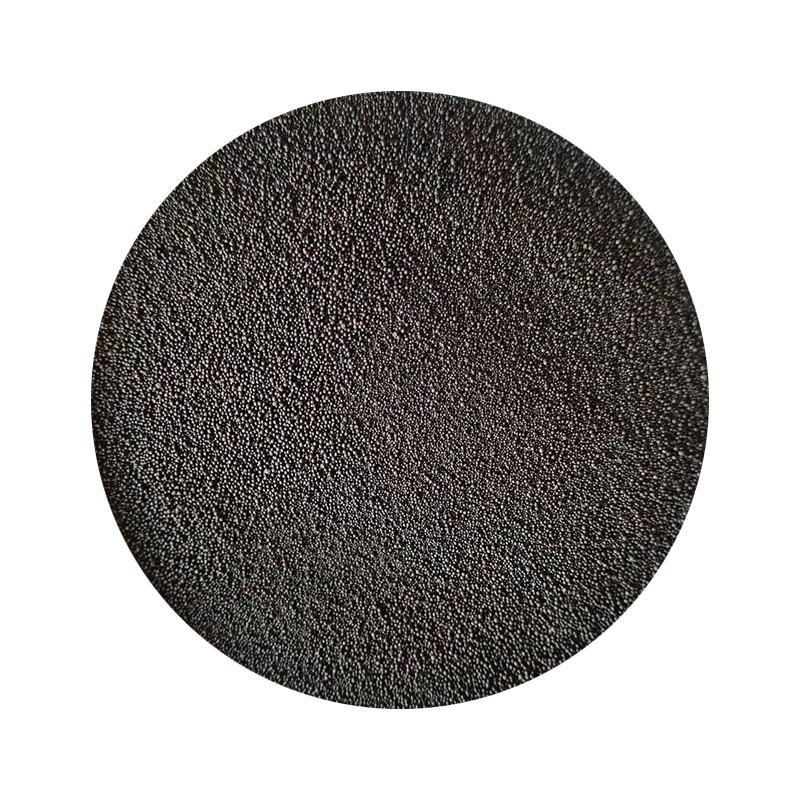
As environmental concerns continue to rise, sand casting companies are implementing sustainable practices. Many are focusing on recycling sand used in the casting process, reducing waste and conserving resources. Companies are also exploring eco-friendly binders to replace traditional chemical binders, thereby lowering harmful emissions during production.
The shift towards electric furnaces instead of traditional gas-fired furnaces is another trend aimed at reducing the carbon footprint. Electric furnaces offer greater energy efficiency and reduced emissions. By investing in sustainable technologies, sand casting companies not only comply with regulatory requirements but also appeal to environmentally conscious consumers.
Industry Trends
The future of sand casting is influenced by several key trends. First, the demand for lightweight components, especially in the automotive and aerospace sectors, is driving the use of sand casting. Innovations in aluminum and magnesium alloys enable the production of lighter, yet strong parts, crucial for fuel efficiency and performance.
Second, the rise of the Internet of Things (IoT) is permeating the manufacturing landscape, including sand casting. Smart factories equipped with IoT devices can monitor production processes in real-time, ensuring optimal performance and timely maintenance of equipment. This connectivity allows companies to be more agile, quickly adapting to changes in production demands or addressing potential quality issues before they escalate.
Lastly, a skilled workforce remains vital to the success of sand casting companies. As technology evolves, there is a growing need for workers who are proficient in both traditional casting methods and new technologies. Companies are investing in training programs to equip their workforce with the necessary skills to thrive in this dynamic environment.
Conclusion
Sand casting companies are at the forefront of a manufacturing revolution, integrating advanced technologies and sustainable practices to meet the evolving needs of various industries. As the process continues to adapt, the potential for efficiency, precision, and sustainability in sand casting is closer than ever, promising a bright future for this time-honored technique. The journey of sand casting, from its ancient roots to a modern manufacturing powerhouse, underscores the industry's resilience and capacity for innovation.
Post time:Nov . 12, 2024 08:30
Next:resin coated sand manufacturing process