Facing Sand in Foundry An Essential Element in Metal Casting
In the realm of metal casting, facing sand plays an indispensable role in ensuring high-quality mold production and ultimately, superior castings. Understanding its properties, applications, and importance is crucial for foundry operations aiming to enhance productivity and produce defect-free castings.
What is Facing Sand?
Facing sand is a fine, high-quality sand used to create the surface layer of a mold. Its primary purpose is to form the part of the mold that comes into direct contact with molten metal. This layer is often composed of a special mixture that provides superior finish to the casting surface, minimizes defects, and enhances the overall structural integrity of the cast piece. The characteristics of facing sand are critical—its grain size, shape, and thermal properties influence the final product's quality.
Properties of Facing Sand
1. Grain Size and Shape Fine and spherical grains are preferred as they form a compact layer and provide a smooth surface finish. Uniform particle size contributes to better molding and reduces the likelihood of surface imperfections in the final product.
2. Thermal Stability Facing sand must withstand high temperatures without breaking down or reacting adversely with the molten metal. It often contains additives that enhance its thermal stability and allow it to endure the casting process without significant erosion.
3. Bonding Agents While facing sands are primarily made of silica, they may include clays and synthetic polymers to improve their binding properties. These agents help hold the grain together and promote a strong mold surface that can withstand the forces exerted during casting.
facing sand in foundry
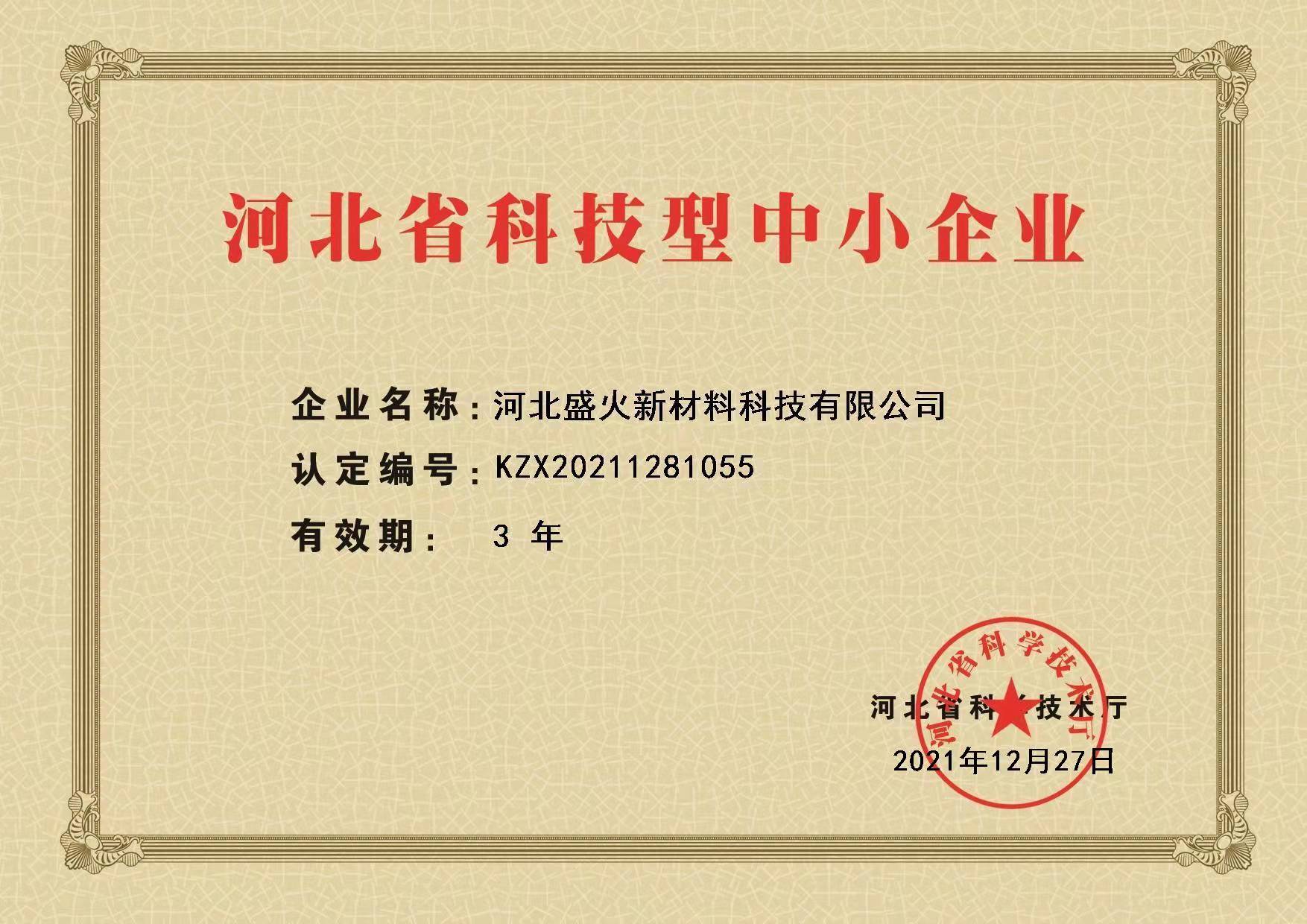
4. Moisture Content The right amount of moisture is crucial since excessive moisture can lead to steam generation, resulting in defects like blowholes. Conversely, insufficient moisture may hinder proper mold formation.
The Role of Facing Sand in Casting Quality
Facing sand is essential in determining the quality of a casting. A well-prepared facing sand layer aids in achieving the desired surface finish and dimensional accuracy. It plays a key role in preventing common casting defects such as sand inclusion, surface roughness, and dimensional inconsistencies.
When molten metal is poured into a mold, it initially interacts with the facing sand. A quality facing sand will impart its properties to the casting surface, thus reducing the roughness and enhancing the aesthetic qualities of the finished product. Furthermore, the thermal characteristics of the sand influence how heat is transferred from the molten metal, impacting solidification rates and, ultimately, mechanical properties like strength and ductility.
Selection of Facing Sand
Choosing the right facing sand involves understanding the specific requirements of the foundry's operations and the types of alloys being cast. Foundries often conduct extensive testing to evaluate various sands for their performance characteristics in relation to different metals, ensuring compatibility and optimal results.
Conclusion
In summary, facing sand is a critical component in the foundry industry, greatly influencing the casting process and the quality of the final products. By selecting appropriate sand types and understanding their properties, foundries can significantly improve casting qualities and operational efficiency. As technology progresses, innovations in facing sand formulations continue to emerge, promising to enhance foundry capabilities and improve the overall manufacturing process. Adopting these advancements can lead to better performance, reduced costs, and higher customer satisfaction in the competitive landscape of metal casting.
Post time:Dec . 07, 2024 09:55
Next:sand 3d