Types of Sand Casting Processes
Sand casting is one of the oldest and most widely used manufacturing processes in the metalworking industry. It involves creating a mold from sand, into which molten metal is poured to produce a desired shape. The versatility and cost-effectiveness of sand casting make it a popular choice for producing complex metal parts in various industries, including automotive, aerospace, and machinery. This article explores the different types of sand casting processes, their applications, and advantages.
1. Green Sand Casting
Green sand casting is the most traditional method of sand casting. In this process, a mixture of sand, clay, and water is used to create the mold. The term green refers to the fact that the mold is not baked or hardened before pouring the metal. The clay helps bind the sand particles together, allowing for a high-quality mold that can retain fine details.
Advantages - Cost-effective due to the use of inexpensive materials. - Quick to set up and produce molds. - Excellent for high-volume production.
Green sand casting is often used for making engine blocks, housings, and large components in the automotive industry.
2. Dry Sand Casting
In dry sand casting, the sand mixture is baked or heated to remove moisture, creating a more rigid and durable mold. This method is particularly useful for producing large and complex shapes that require higher dimensional accuracy. The dry sand mold is often coated with a release agent to ensure that the casting can be easily removed once the metal has cooled and solidified.
Advantages - Higher dimensional accuracy compared to green sand casting. - Improved surface finish on the final product. - Better suitability for intricate designs.
Dry sand casting is often used in applications where precision is critical, such as aerospace components and intricate machinery parts.
3. No-Bake Sand Casting
No-bake sand casting eliminates the need for baking by using a resin binder that hardens at room temperature. The sand and resin mixture is packed around a pattern, and the heat of the molten metal cures the resin during casting. This method allows for the production of highly detailed molds with smooth finishes.
types of sand casting process
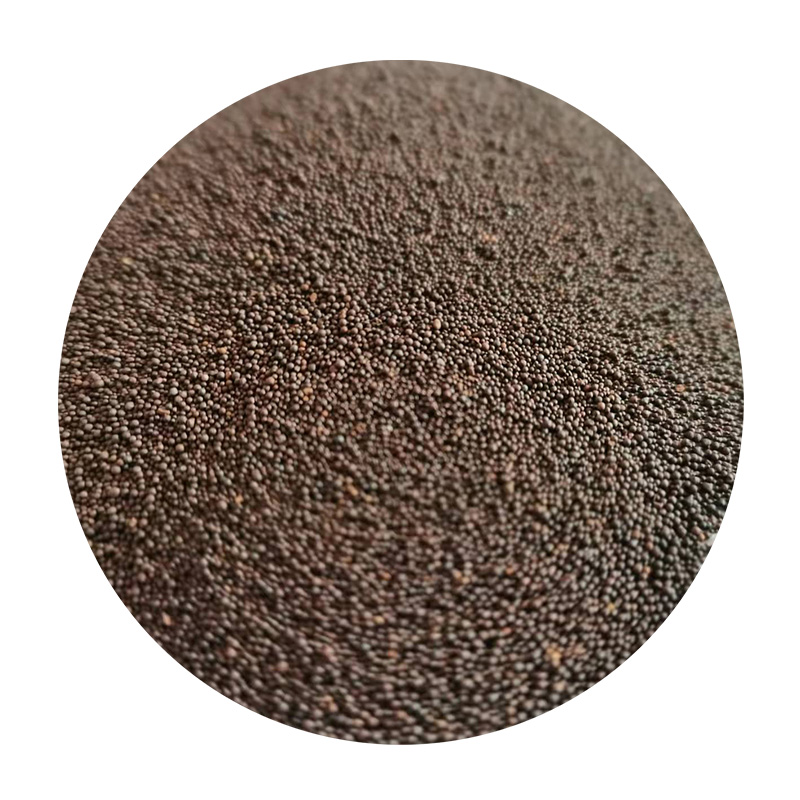
Advantages - Excellent surface quality and detail accuracy. - Ideal for producing small to medium-sized runs of complex parts. - Shorter lead times compared to traditional methods.
No-bake sand casting is used for producing intricate components like brackets, gears, and various automotive parts.
4. Lost Foam Casting
Lost foam casting is a unique sand casting method that uses a foam pattern instead of a traditional metal or wooden pattern. The foam pattern is coated with a refractory material and then surrounded by sand. When molten metal is poured into the mold, it vaporizes the foam, creating a cavity in the shape of the original pattern.
Advantages - Allows for complex geometries and excellent surface finishes. - Eliminates the need for ejector pins or draft angles. - Reduced processing times and costs.
Lost foam casting is commonly employed in automotive applications, particularly for producing engine parts and other components with intricate shapes.
5. Shell Mold Casting
Shell mold casting involves creating a mold from a thermosetting resin and sand mixture. This process produces a thin-walled, rigid mold. The pattern is heated, and the resin-sand mixture is applied to it, forming a shell. Once the shell solidifies, the two halves are joined to form a mold.
Advantages - High dimensional accuracy and repeatability. - Smooth surface finish, reducing the need for machining. - Suitable for both high-volume and low-volume production.
Shell mold casting is often utilized for manufacturing high-precision parts such as valves, gears, and automotive components.
Conclusion
Sand casting remains a staple of the metalworking industry due to its adaptability and cost-effectiveness. Understanding the various types of sand casting processes allows manufacturers to select the most appropriate method for their specific needs. Whether it's green sand, dry sand, no-bake, lost foam, or shell mold casting, each process offers unique advantages that can lead to the efficient production of high-quality metal components. As technologies evolve, these methods continue to adapt, ensuring that sand casting remains relevant in modern manufacturing.
Post time:Nov . 11, 2024 04:54
Next:Effective Techniques for Sanding Stainless Steel Surfaces Smoothly and Efficiently