Types of Sand Casting
Sand casting is one of the most versatile and widely used methods for producing metal parts and components. This process involves creating a mold from sand and using it to cast a liquid metal into a desired shape. Due to its adaptability to various metals and alloys, different types of sand casting techniques have been developed to meet specific manufacturing requirements. In this article, we will explore the various types of sand casting, their unique characteristics, and their applications.
1. Green Sand Casting
Green sand casting is the most common type and involves a mixture of sand, clay, and water. The term green refers to the moisture content of the sand, which is not completely dried before use. This method is popular because it is economical and allows for the production of complex shapes with relatively good surface finishes. Green sand molds are easy to create, making it suitable for both small-scale and large-scale production. The casting process begins with the preparation of a pattern that is pressed into the sand to create a mold. Once the mold is formed, the liquid metal is poured in and allowed to cool and solidify.
Green sand casting is widely used in the automotive, aerospace, and manufacturing industries for producing a variety of parts ranging from engine blocks to decorative hardware.
2. Air Set Sand Casting
Air set sand casting, also known as no-bake sand casting, utilizes a mixture of sand and a binder that hardens at room temperature. The curing agent is often a catalyst that reacts with the binder to form a solid mold. This type of sand casting can produce more intricate and fine details compared to green sand casting. The primary advantage of air set sand casting is the ability to create molds of varying thickness without the need for moisture, which can lead to defects in the final casting.
Air set sand molds are typically used for casting aluminum, iron, and bronze and find applications in the marine and heavy equipment industries, among others.
3. Lost Foam Casting
Lost foam casting is a process in which a foam pattern is coated with sand and then heated to remove the foam. This method allows for the production of very complex shapes and is especially beneficial for producing intricate designs. The lost foam casting process minimizes the need for additional machining, as the foam pattern is typically very accurate.
types of sand casting
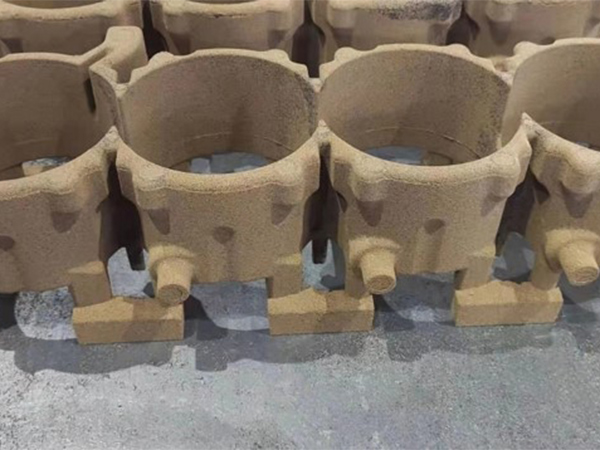
This method is particularly useful for casting materials such as aluminum and magnesium and is often utilized in the automotive industry for producing highly detailed components such as cylinder heads and engine blocks.
4
. Co2 Sand CastingCO2 sand casting uses a mixture of sand and sodium silicate as a binder, which is cured with carbon dioxide gas. This type of casting process produces very strong and reusable molds that are less susceptible to deformation compared to other types. CO2 sand casting is known for its excellent dimensional accuracy and surface finish, making it ideal for producing intricate parts with tight tolerances.
Its applications are prevalent in industries that require high precision, including aerospace, military, and a wide range of manufacturing sectors.
5. Resin Sand Casting
In resin sand casting, a phenolic resin is used as a binder, resulting in higher mold strength and improved dimensional stability. This method allows for better surface finishes and a reduction in the amount of sand required, making it an efficient choice for many manufacturers. The resin-coated sand produces molds that can withstand higher temperatures, making this method particularly useful for casting ferrous and non-ferrous metals.
Resin sand casting is widely applied in the automotive, machine-building, and aerospace industries due to its versatility and quality output.
Conclusion
Sand casting remains a fundamental process in the metalworking industry, with various types adapted to meet specific needs. Each method possesses distinct advantages and applications, from the cost-effective green sand casting to the precision-focused CO2 and resin sand casting techniques. Understanding these different types of sand casting allows manufacturers to select the right process for their production needs, ensuring efficiency and quality in their metal casting endeavors.
Post time:Th11 . 08, 2024 18:25
Next:sand castings