The Steel Sand Casting Process A Comprehensive Overview
Steel sand casting is a traditional yet widely adopted manufacturing process that plays a crucial role in producing metal components across various industries. This method combines the strength of steel with the versatility of sand molds to create precision-engineered parts for machinery, automotive components, and various structural applications. Understanding the steel sand casting process involves breaking down its stages, advantages, and applications.
The Process
The steel sand casting process begins with the preparation of a pattern, which is a replica of the final product. Patterns are typically made from materials like wood, metal, or plastic and are designed to create a mold cavity that reflects the desired shape of the casting. Once the pattern is complete, it is coated with a release agent to facilitate easy removal from the mold.
Next, the molding sand is prepared. This sand is mixed with a binding agent, commonly clay, and water to enhance its cohesiveness. The sand mixture is then packed around the pattern to form two halves of a mold — the cope (top half) and the drag (bottom half). Once the sand is firmly compacted, the pattern is removed, leaving behind a hollow cavity that mimics the desired component's shape.
Once the mold is ready, it is coated with a fine layer of sand to smooth the inner surface and improve the casting finish. After that, the cope and drag are reassembled, and channels called risers and gates are created to facilitate the flow of molten steel and allow for any gas to escape during the pouring process.
The next critical step is to melt the steel. This is typically done in an induction furnace that ensures the steel reaches the appropriate temperature for pouring. Once the molten steel is ready, it is poured into the mold cavity through the gates, filling the void and taking on the mold's shape.
steel sand casting process
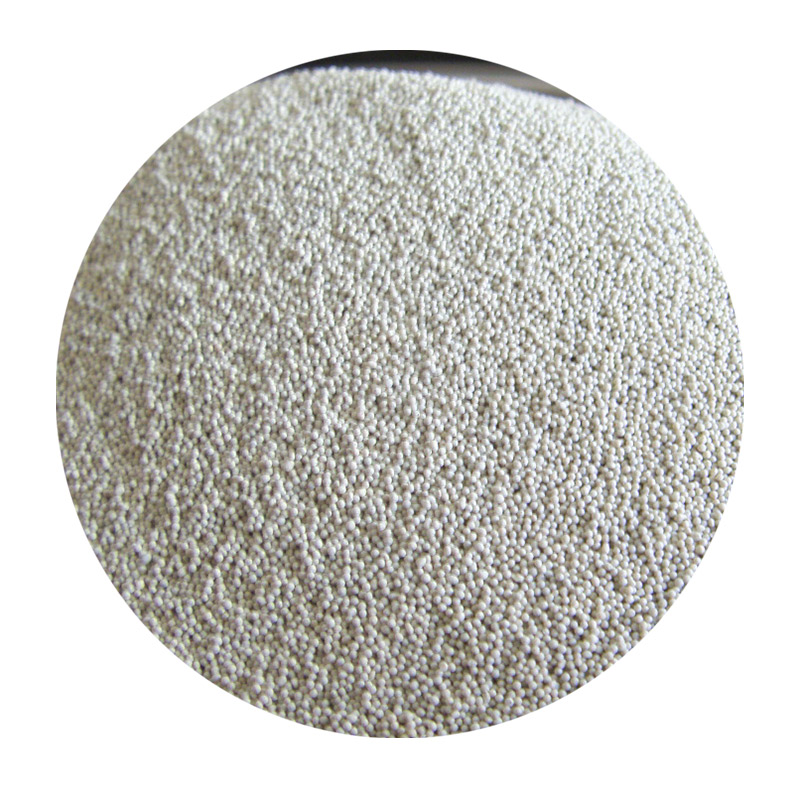
After allowing the steel to cool and solidify, the mold is broken apart to reveal the casting. At this point, the cast component is still surrounded by excess material, such as the risers and gates, which need to be removed. This is followed by processes such as cleaning, machining, and finishing to enhance the component's physical properties and appearance.
Advantages of Steel Sand Casting
One of the primary advantages of steel sand casting is its ability to produce complex shapes that would be difficult or impossible to achieve through other manufacturing methods. The flexibility of sand molds allows for modifications during design without significant additional costs. Moreover, sand casting can accommodate a wide range of steel grades and alloys, making it suitable for various applications.
Additionally, the process is cost-effective for low to medium production volumes, as tooling costs are relatively low compared to other casting methods. This affordability makes it a favorable choice for small manufacturers and startups looking to create high-quality components without a hefty investment.
Applications
Steel sand casting is utilized in numerous fields due to its adaptability and efficiency. Common applications include the production of engine components, gears, frames, and structural parts for machinery and vehicles. The aerospace and defense industries also benefit from this process, as it allows for the production of castings that meet stringent safety and performance standards.
In conclusion, the steel sand casting process is a vital manufacturing technique that combines age-old practices with modern advancements to produce durable and complex components across various sectors. Its versatility and cost-effectiveness ensure its continued relevance in the manufacturing landscape, making it an essential method for engineers and designers worldwide.
Post time:Th11 . 27, 2024 13:41
Next:Exploring the Diverse Applications of Sand Casting in Modern Manufacturing Techniques