Understanding the Sand Casting Process
Sand casting, also known as sand mold casting, is a versatile and widely used manufacturing process that involves pouring molten metal into a sand-based mold to create complex shapes and components. This method is appreciated for its simplicity, cost-effectiveness, and ability to produce large parts or intricate designs without the need for specialized equipment. Here, we will delve into the intricacies of the sand casting process, its advantages, and its applications in various industries.
The Sand Casting Process
The sand casting process begins with the creation of a pattern, which is a replica of the final product
. Patterns can be made from various materials, including metal, wood, or plastic, and they are typically slightly larger than the final piece to account for the shrinkage that occurs during cooling. Once the pattern is prepared, the next step involves preparing the mold.The mold is created by mixing sand with a binding agent, often clay, and water to enhance its cohesiveness. This mixture is packed around the pattern in a two-part mold, known as the cope and drag. The sand is compressed to ensure that it holds the shape of the pattern when the pattern is removed. After the pattern is extracted, the mold halves are assembled, and any necessary channels for pouring and vents for gases are added.
Once the mold is ready, molten metal is poured into it. The temperature of the molten metal is typically high, often exceeding 1,000 degrees Celsius, depending on the type of metal being used. After the metal fills the mold cavity, it is allowed to cool and solidify. Cooling times vary based on the metal and the thickness of the part but usually take anywhere from a few minutes to several hours.
Once solidified, the sand mold is broken away, revealing the casting. The final step involves cleaning the casting, which includes removing any sand or unwanted material and performing any necessary machining to achieve the desired surface finish and dimensional accuracy.
sand casting process
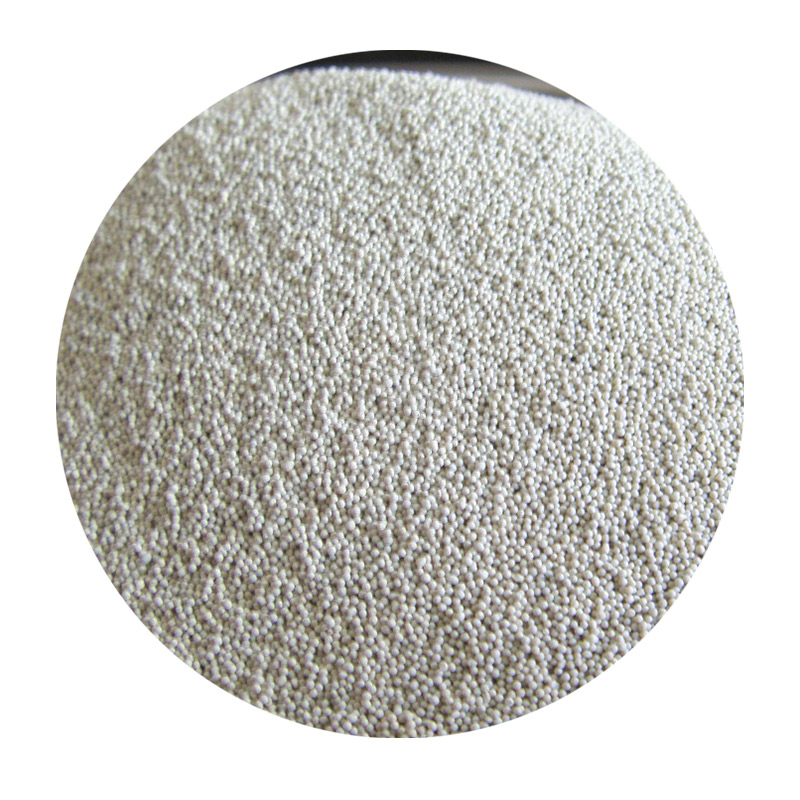
Advantages of Sand Casting
Sand casting offers numerous advantages, making it a popular choice for many manufacturing applications. Firstly, the cost of materials is relatively low, particularly for the sand, which can be reused multiple times. This makes sand casting an economically viable option for both small-scale and large-scale production.
Additionally, the process allows for great flexibility in design and production. Almost any metal that can be melted can be used in sand casting, including aluminum, copper, iron, and steel. This versatility makes it suitable for a wide range of applications, from automotive parts to intricate art pieces.
Moreover, sand casting can produce complex geometries with excellent surface finishes, which can reduce the need for secondary operations. The process is also capable of producing large parts that would be difficult or impossible to achieve with other casting methods.
Applications of Sand Casting
Sand casting is used across various industries, including automotive, aerospace, marine, and general manufacturing. It is commonly employed for producing engine blocks, transmission cases, and various other components where strength and precision are paramount. The art of sand casting has also found its place in artistic applications, allowing sculptors to create custom metal artworks.
In summary, the sand casting process is an essential method in the manufacturing landscape. Its simplicity, cost-effectiveness, and versatility make it an ideal choice for producing a wide variety of metal components, from functional machinery parts to artistic sculptures. As technology continues to evolve, sand casting will likely remain a staple due to its ability to adapt to modern manufacturing needs.
Post time:Th10 . 11, 2024 18:22
Next:sand caste