Understanding Sand Casting Materials An In-Depth Overview
Sand casting, one of the oldest and most versatile metal casting processes, relies heavily on the properties of various materials used in mold and core production. The choice of sand and other materials significantly influences the quality, accuracy, and efficiency of the casting process. This article delves into the key materials used in sand casting, their properties, and how they contribute to successful metal casting operations.
1. Sand Types The Foundation of Sand Casting
At the heart of the sand casting process is sand itself, primarily composed of silica (SiO2). The most common type used is green sand, which includes a mixture of sand, clay, water, and additives. Green sand is favored for its ability to retain moisture and provide good molding capabilities. The clay, usually bentonite, enhances the sand's binding properties, enabling it to hold its shape during the casting process.
In contrast, resin-bonded sand, such as phenolic resin, is another popular choice. This type of sand has improved dimensional accuracy and surface finish, mainly because it cures to a solid state when heat is applied. This curing process minimizes the risk of defects, making it suitable for high-precision applications.
2. Additives Enhancing Sand Properties
To tailor the properties of sand, various additives are introduced
. These can include- Clay As mentioned, clay acts as a binder in green sand. It helps in retaining moisture and providing structure to the sand mixture.
- Water Controlling the moisture content is critical. Too much water can lead to defects like gas porosity, while too little can cause the sand to crumble. An optimal balance ensures a strong mold.
- Coal Dust Often added to green sand to improve surface finish, coal dust can also enhance the mold's ability to withstand heat.
sand casting materials
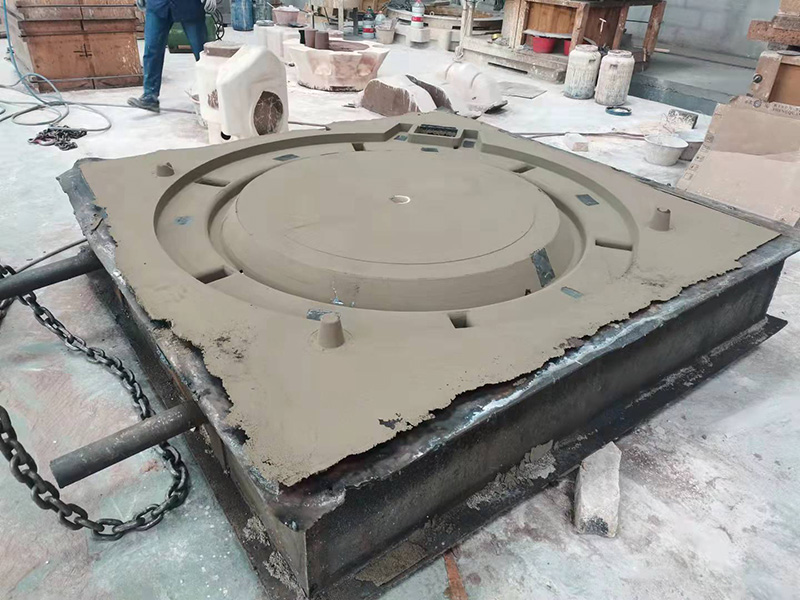
- Other Additives These may include materials like talc or various oils to improve flowability and minimize casting defects, especially in complex mold designs.
3. The Role of Cores in Sand Casting
Cores are used to create internal cavities in castings. They are typically made from sand as well, often with a different binder system to accommodate changes in temperature and provide strength. Core materials must withstand the molten metal's heat and pressure without deforming.
The choice of core sand also plays a crucial role in the final properties of the casting. For example, core sands may be mixed with oils or resin binders to enhance their strength and thermal stability, which is particularly advantageous for complex geometric designs.
4. Considerations for Metal Types
The type of metal being cast also influences the choice of sand and additives. For instance, when casting aluminum, the sand must be able to handle the metal's heat without breaking down or introducing impurities. Metals with high melting points, like bronze or steel, may require sand with enhanced thermal properties, often achieved through specific additives or a different sand composition entirely.
5. Environmental Impact and Innovations
Modern sand casting practices are increasingly focused on sustainability. Traditional sand casting generates significant waste, but new technologies aim to recycle sand and minimize environmental impact. Innovations in binders, such as inorganic and eco-friendly options, help reduce the reliance on petrochemical products, making the process more sustainable.
Conclusion
The materials used in sand casting play a pivotal role in determining the efficiency, quality, and environmental friendliness of the casting process. Understanding the properties and interactions of different sands, additives, and core materials allows engineers and manufacturers to optimize casting operations. As the industry continues to evolve, innovations in material science will likely lead to even more efficient and environmentally sustainable sand casting practices, ensuring that this ancient method remains relevant in modern manufacturing.
Post time:Th10 . 18, 2024 11:59
Next:Essential Elements of the Sand Casting Process for Effective Manufacturing