Furan Resin Sand Casting A Comprehensive Overview
Furan resin sand casting is a widely used manufacturing process in foundries and metalworking industries. This technique leverages the unique properties of furan resin, a synthetic resin derived from furfural, to create high-quality sand molds for casting metals. The process has gained popularity for its efficiency, cost-effectiveness, and ability to produce intricate designs with excellent surface finishes.
One of the primary advantages of furan resin sand casting is its thermal stability. Furan resin withstands high temperatures, making it ideal for casting operations that involve molten metals, such as aluminum, iron, and steel. The resin-bonded sand molds can endure the intense heat without deforming or losing their shape, resulting in precise and repeatable castings. Furthermore, furan resin exhibits low thermal expansion, which minimizes the risk of dimensional inaccuracies and defects in the final product.
The process begins with the preparation of the sand mixture, which typically includes sand, furan resin, and hardening agents. The choice of sand is crucial, as it influences the mold's strength and surface finish. Silica sand is commonly used due to its availability and compatibility with furan resin. The resin is mixed with the sand in specific proportions, often around 2-5% by weight, depending on the desired properties of the mold. Additionally, various catalysts can be added to accelerate the curing process, allowing for quicker production cycles.
furan resin sand casting
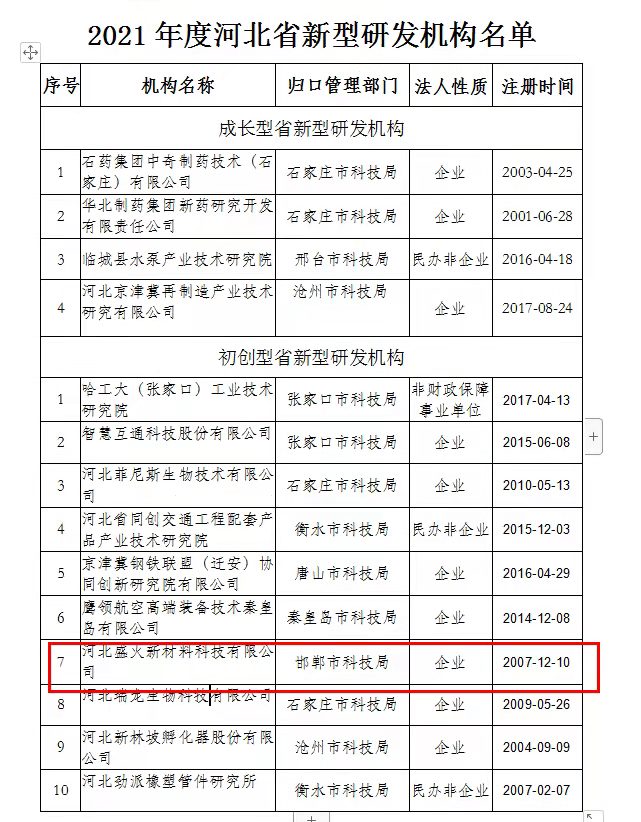
Once the sand mixture is prepared, it is formed into molds using either manual or automated techniques. The molding process involves packing the sand mixture around a pattern that represents the desired shape of the finished casting. After the mold is formed, it is subjected to heat or chemical reactions that activate the furan resin, causing it to harden and bind the sand particles together. This hardening process can take anywhere from a few minutes to several hours, depending on the specific formulation and environmental conditions.
The resulting molds are remarkably durable and can withstand multiple casting cycles. This longevity contributes to the cost-effectiveness of furan resin sand casting, as foundries can produce high volumes of castings without the need for frequent mold replacements. Moreover, the smooth surface finish achieved with furan resin reduces the need for extensive post-casting machining, thereby speeding up production times and lowering overall costs.
However, there are some considerations when using furan resin sand casting. The furan resin can release volatile organic compounds (VOCs) during the curing process, which may pose health and environmental concerns. Therefore, foundries must implement adequate ventilation systems and safety measures to protect workers and minimize emissions. Additionally, the initial investment for furan resin and the associated equipment may be higher than traditional sand casting methods, but the long-term benefits often outweigh these costs.
In conclusion, furan resin sand casting is a versatile and efficient manufacturing method that offers numerous advantages for producing high-quality metal castings. With its ability to create detailed designs and withstand high temperatures, it remains a popular choice in the metalworking industry. As technology evolves and environmental regulations tighten, further advancements in furan resin formulations and casting techniques are anticipated, enhancing the sustainability and efficiency of this established process.
Post time:Th9 . 04, 2024 18:10
Next:Sand Casting - Precision Sand Molding for Quality Metal Parts