The Properties of Foundry Sand A Comprehensive Overview
Foundry sand is a crucial material used in metal casting processes, serving as the molding medium that shapes molten metal into desired forms. The properties of foundry sand greatly influence the quality of the cast products, making it essential for foundries to select the appropriate sand type and maintain its characteristics throughout the casting process. This article explores the key properties of foundry sand, including its composition, thermal stability, permeability, and bonding capabilities.
1. Composition of Foundry Sand
The primary type of sand used in foundries is silica sand, predominantly composed of silicon dioxide (SiO2). This material is favored due to its high melting point, which allows it to withstand the heat generated during metal pouring without breaking down. Other minerals, such as clay and iron oxide, can be present in smaller quantities and may influence certain properties of the sand. For example, clay aids in the bonding of sand grains, while iron oxide can affect the color and thermal properties of the final cast.
One of the most critical properties of foundry sand is its thermal stability. During the casting process, the sand comes into contact with molten metal, which can reach temperatures of up to 1,600 °C (2,912 °F) depending on the metal being cast. Foundry sand must maintain its structural integrity under these extreme conditions. High thermal stability ensures that the sand does not fuse with the metal or collapse under heat stress, maintaining the accuracy of the mold.
3. Permeability
foundry sand properties
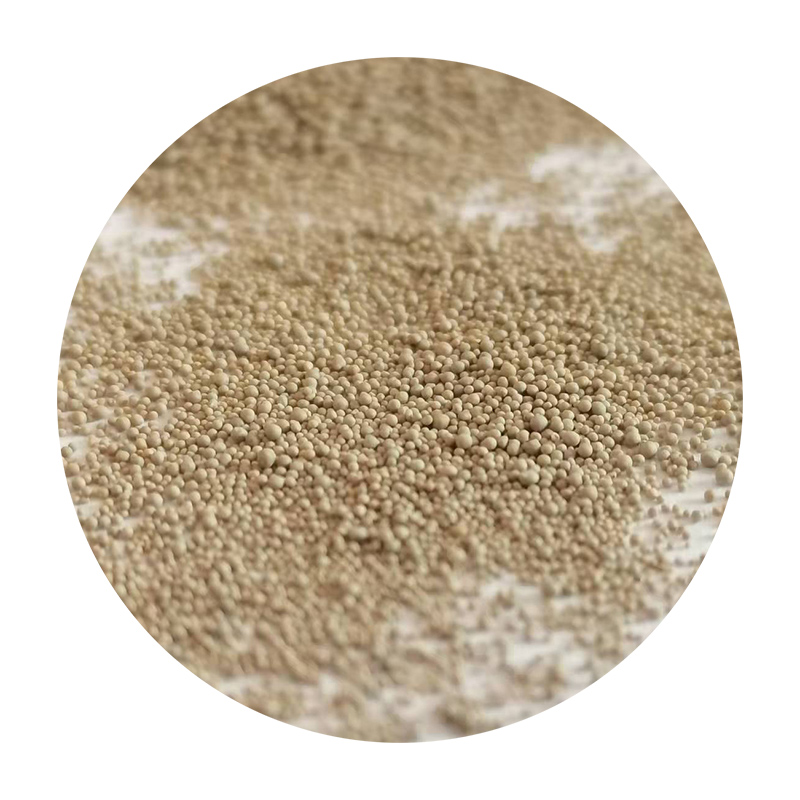
Permeability refers to the sand's ability to allow gases and air to pass through it. This property is vital during the casting process, as the molten metal releases gases that need to escape to prevent defects in the finished product, such as porosity or inclusions. Foundry sands typically require a specific permeability range, which can be adjusted by altering the composition or grain size of the sand. A balance must be struck, as too high permeability may lead to a weak mold, while too low permeability can trap gases.
4. Bonding Capabilities
The ability of foundry sand to hold together under stress is another essential property known as bonding or cohesiveness. Effective bonding ensures the mold retains its shape during the metal pouring process. This property is often enhanced through the addition of bonding agents such as clay or resin. For example, green sand, a mixture of silica sand, clay, and moisture, is commonly used due to its excellent bonding properties. In contrast, resin-bonded sands provide superior strength and thermal shock resistance, making them suitable for high-performance applications.
5. Recycling and Sustainability
In recent years, the foundry industry has faced increasing pressure to adopt sustainable practices. One such approach involves the recycling of foundry sand. Used sand can often be cleaned and reused, reducing waste and lowering operational costs. However, the recycled sand must be carefully assessed for its properties, ensuring it meets the necessary standards for performance in subsequent casting processes.
In conclusion, the properties of foundry sand play a vital role in the metal casting industry. Understanding factors such as composition, thermal stability, permeability, and bonding capabilities is essential for foundries to produce high-quality castings. As the industry moves towards more sustainable practices, effective management and recycling of foundry sand will become increasingly important for maintaining efficiency and environmental responsibility. By prioritizing these properties, foundries can optimize their processes and deliver superior products to meet market demands.
Post time:Th10 . 10, 2024 16:52
Next:Sand Casting Production Specialists for Customized Manufacturing Solutions and Quality Assurance