Different Types of Foundry Sand
Foundries are critical to metal casting operations, and one of the key materials used in these processes is foundry sand. Foundry sand has unique characteristics that make it ideal for creating the molds required for metal casting. Various types of foundry sands have distinct properties and applications, catering to specific needs in the casting process. This article explores the different types of foundry sand, their characteristics, and their uses in the metal casting industry.
1. Silica Sand
Silica sand is one of the most commonly used types of foundry sand. It is composed mainly of silicon dioxide (SiO2) and is known for its high strength and thermal stability, making it ideal for high-temperature applications. Silica sand provides excellent surface finish and dimensional accuracy to the castings. It is versatile and used in both ferrous and non-ferrous metal casting environments. However, it must be used with caution, as inhalation of silica dust can lead to serious health issues.
2. Green Sand
Green sand, often referred to as clay-bound sand, is another popular choice in the foundry industry. It is made from silica sand mixed with a small percentage of clay, water, and various additives. The moisture content in green sand gives it a greenish color, hence the name. This type of sand has excellent moldability and can retain a high level of shape accuracy during casting. Green sand is widely used for casting iron, aluminum, and other non-ferrous metals due to its excellent performance and cost-effectiveness.
3. Resin Coated Sand
different types of foundry sand
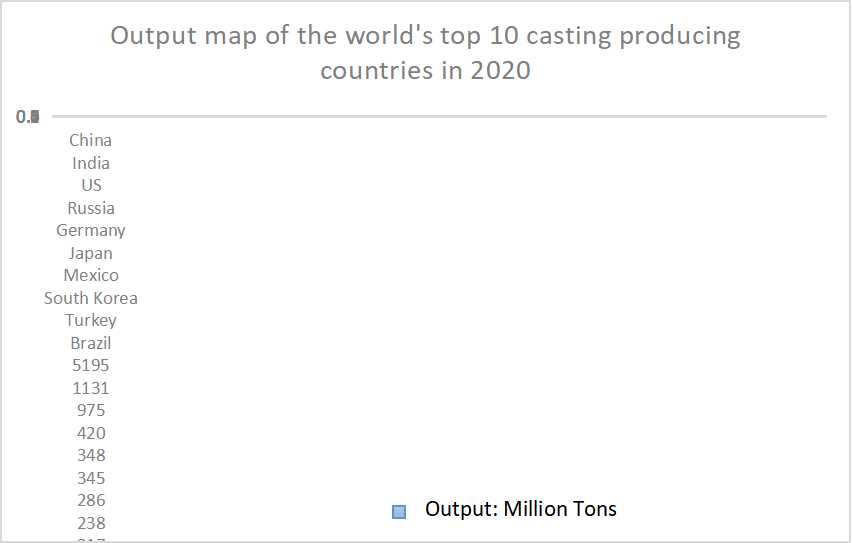
Resin-coated sand incorporates a thermosetting resin binder that enhances the properties of conventional sand. The process involves coating silica sand grains with a mixture of resin and hardeners, which improves the sand's strength and reduces the amount of binder needed in the casting process. Resin-coated sand is known for producing high-precision molds with smooth surfaces and excellent dimensional accuracy. It is often used in the manufacturing of complex parts and in applications where a high-quality finish is required.
4. Oil Sand
Oil sand, also known as petroleum coke sand, is another type of foundry sand that combines silica sand and oil as a binder. The oil acts as a binder, providing additional strength and durability to the mold. Oil sand is particularly recognized for its ability to withstand higher temperatures, making it suitable for casting ferrous metals. The use of oil sand results in reduced thermal expansion, which minimizes defects in the final castings.
5. Specialty Sands
Apart from the conventional types, there are various specialty sands used in specific applications. For example, zircon sand is highly valued for its exceptional thermal stability and is often used in investment casting. Chromite sand, with its unique resistance to thermal shock, is commonly employed in steel casting processes. Each specialty sand possesses characteristics that make it suitable for particular casting requirements, ensuring high-quality outputs.
Conclusion
The choice of foundry sand significantly impacts the quality and efficiency of the casting process. Understanding the different types of foundry sand—silica, green, resin-coated, oil sand, and specialty sands—allows foundry engineers to make informed decisions based on the specific needs of their operations. Each type of sand offers unique advantages, and selecting the right one is crucial for optimizing the casting process, minimizing defects, and ensuring the production of high-quality metal components. As technology advances, the development of new sand formulations continues to enhance the capabilities of foundries, paving the way for innovative applications in metal casting.
Post time:Th11 . 24, 2024 19:21
Next:sand in cast