Applications of Sand Casting
Sand casting, one of the oldest metal casting processes, serves as a versatile and economical method of producing metal parts across various industries. Its simplicity and adaptability make it a preferred choice for both large-scale production runs and prototyping. This article explores several key applications of sand casting, highlighting its significance in different fields.
1. Automotive Industry
The automotive sector is one of the largest consumers of sand casting techniques. Critical components such as engine blocks, cylinder heads, and transmission housings are often produced using sand casting. The process allows for complex geometries and substantial component sizes which are essential for meeting the performance and durability requirements of modern vehicles. Furthermore, sand casting enables manufacturers to produce lightweight yet robust components, which is increasingly crucial as the automotive industry shifts towards electric and hybrid vehicles. The ability to easily incorporate design modifications through this technique also supports continuous improvement in automotive engineering.
2. Aerospace Engineering
In aerospace engineering, sand casting is utilized to manufacture lightweight and high-strength components, essential for aircraft performance and safety. Components such as brackets, housings, and complex shapes are often produced with this method. The aerospace industry demands high precision and quality, and while sand casting is less precise than other casting processes, technological advancements have improved the method’s accuracy. Moreover, sand casting allows for the use of high-performance alloys, which are vital in reducing vehicle weight and enhancing fuel efficiency.
The marine industry significantly benefits from sand casting due to the need for rust-resistant and durable materials. Components such as propellers, cleats, and various fittings are produced using sand casting, allowing for the incorporation of complex designs that can withstand harsh marine environments. The use of materials like aluminum and bronze in sand casting applications enhances resistance to corrosion and increases the longevity of the parts, making it an ideal solution for marine engineering.
applications of sand casting
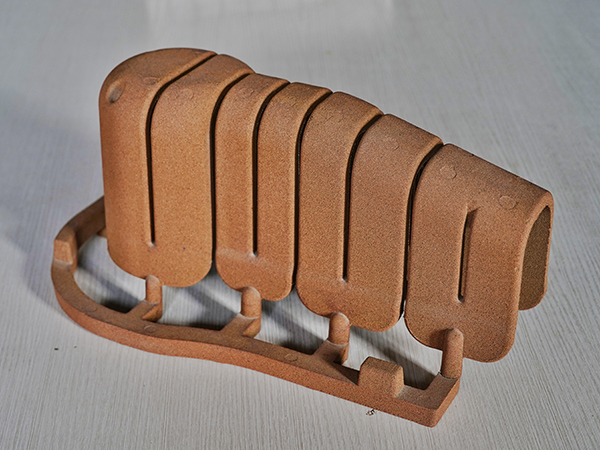
4. Industrial Machinery
Sand casting plays an integral role in producing components for industrial machinery. Equipment such as pumps, valves, and gearboxes often rely on sand cast parts for their construction. The process enables the production of sturdy, custom shapes that can handle significant stress and wear over time. Additionally, sand casting is economically viable for producing low to moderate quantities of machinery components, appealing to manufacturers seeking efficient production methods.
5. Art and Sculptures
Beyond industrial applications, sand casting also extends into the artistic domain. Artists and sculptors often utilize sand casting to create intricate metal sculptures, jewelry, and decorative pieces. The ability to replicate fine details through sand molds makes it a preferred method for artists wishing to produce unique works. The versatility of sand casting allows for the incorporation of various metals, enabling artists to achieve desired aesthetics and finishes.
6. Historical Reconstruction and Heritage Conservation
Sand casting has found a niche in historical reconstruction and heritage conservation projects. Experts utilize this technique to replicate historical artifacts or components that are no longer in production. By carefully studying original pieces, artisans can create accurate reproductions that preserve the integrity and authenticity of historical sites and artifacts. This application ensures the continuity of cultural heritage while allowing for educational opportunities.
Conclusion
The applications of sand casting are diverse, spanning industries from automotive and aerospace to art and historical preservation. Its adaptability, cost-effectiveness, and ability to produce complex geometries make it an enduringly popular choice for manufacturers and artists alike. As technology continues to evolve, the potential for sand casting processes will likely expand, offering new opportunities for innovation and improvement in both industrial and artistic domains. Understanding the advantages and capabilities of sand casting can pave the way for more sustainable and efficient production methods that meet the demands of modern engineering and design.
Post time:Th10 . 16, 2024 17:43
Next:الرمال 3D الطباعة