The Future of Manufacturing 3D Printed Sand Casting
In recent years, the manufacturing sector has been undergoing a transformative shift towards adopting advanced technologies. Among these innovations, 3D printing has emerged as a game-changer, particularly in the field of sand casting. This novel approach blends traditional casting techniques with modern 3D printing technologies, offering numerous advantages in terms of efficiency, cost-effectiveness, and design flexibility.
Traditional sand casting has served industries for centuries, allowing manufacturers to produce intricate metal components. However, it comes with its own set of challenges, including longer lead times, high labor costs, and constraints on design complexity. The introduction of 3D printed sand casting addresses many of these issues, revolutionizing the way manufacturers approach mold-making.
The Future of Manufacturing 3D Printed Sand Casting
Furthermore, the cost savings associated with 3D printed sand casting are significant. Traditional molds can be expensive to create, especially for low-volume production runs. By utilizing 3D printing, manufacturers can produce molds without the high upfront costs associated with traditional tooling. This is particularly beneficial for small and medium-sized enterprises (SMEs) that might struggle to justify large investments in custom molds. Additionally, the minimization of material waste during the printing process leads to a more environmentally friendly approach, aligning with the growing demand for sustainable manufacturing practices.
3d printed sand casting
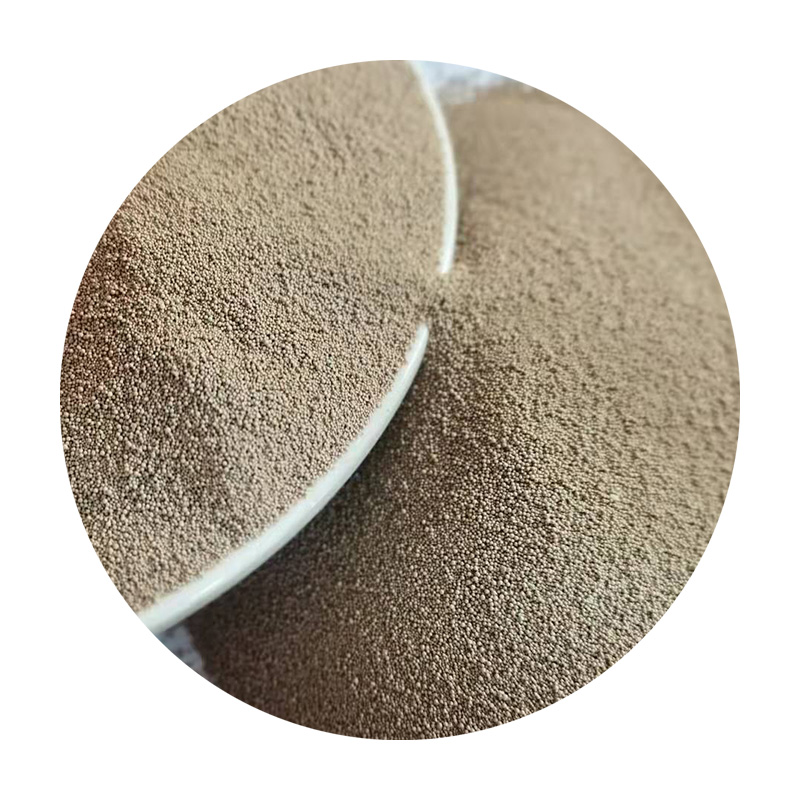
One of the most exciting aspects of 3D printed sand casting is its design capabilities. The complexity and intricacy that can be achieved are far beyond what traditional methods allow. Designers are no longer constrained by the limitations of traditional mold-making, as 3D printing enables the creation of complex geometries that were previously impossible. This opens up a new world of possibilities for product innovation, allowing engineers to experiment with shapes and structures that can enhance functionality and performance.
Moreover, the flexibility offered by 3D printing means that manufacturers can quickly pivot to meet changing market demands. If a design needs to be altered or updated, producing a new mold takes a fraction of the time compared to traditional methods. This agility in production can give companies a competitive edge, enabling them to respond more effectively to customer needs.
The adoption of 3D printed sand casting has not been without challenges, however. The initial investment in 3D printing technology and training can be substantial. Additionally, the quality control of printed molds is critical to ensure that the final castings meet industry standards. Nonetheless, as technology continues to advance and the costs associated with 3D printers decrease, these barriers are likely to diminish.
In conclusion, 3D printed sand casting represents a significant leap forward in manufacturing technology. By merging the benefits of traditional sand casting with the innovations of 3D printing, manufacturers can enjoy faster production times, cost savings, and greater design freedom. As industries increasingly recognize the advantages of this approach, it is poised to redefine the future of casting and metal component manufacturing, leading to more efficient and innovative production processes. Embracing this technology could very well be the key to staying competitive in an ever-evolving marketplace.
Post time:Th11 . 08, 2024 04:39
Next:Innovative Sand Casting Solutions from Leading Manufacturers in the Industry Today