Stainless Steel Sand Casting Foundry An Overview
Stainless steel sand casting has emerged as a crucial technique in the manufacturing industry, known for its versatility, durability, and cost-effectiveness. This method involves using sand molds to form complex shapes, which are then filled with molten stainless steel to create high-quality components. With the growing demand for stainless steel products in various sectors, from aerospace to automotive, the significance of stainless steel sand casting foundries has never been more pronounced.
Stainless steel is an alloy known for its corrosion resistance, strength, and aesthetic appeal. The unique properties of stainless steel make it ideal for applications that require durability and hygiene, such as food processing equipment, medical devices, and architectural features. When it comes to sand casting, the use of stainless steel presents specific advantages, including the ability to create complex geometries and structural integrity.
The sand casting process begins with creating a mold from fine sand mixed with a bind agent. The mold is designed based on the specifications of the final product, allowing for intricate designs that might be difficult to achieve with other manufacturing methods. One of the primary benefits of sand casting is its flexibility in producing both small and large batches, making it suitable for a wide range of projects.
stainless steel sand casting foundry
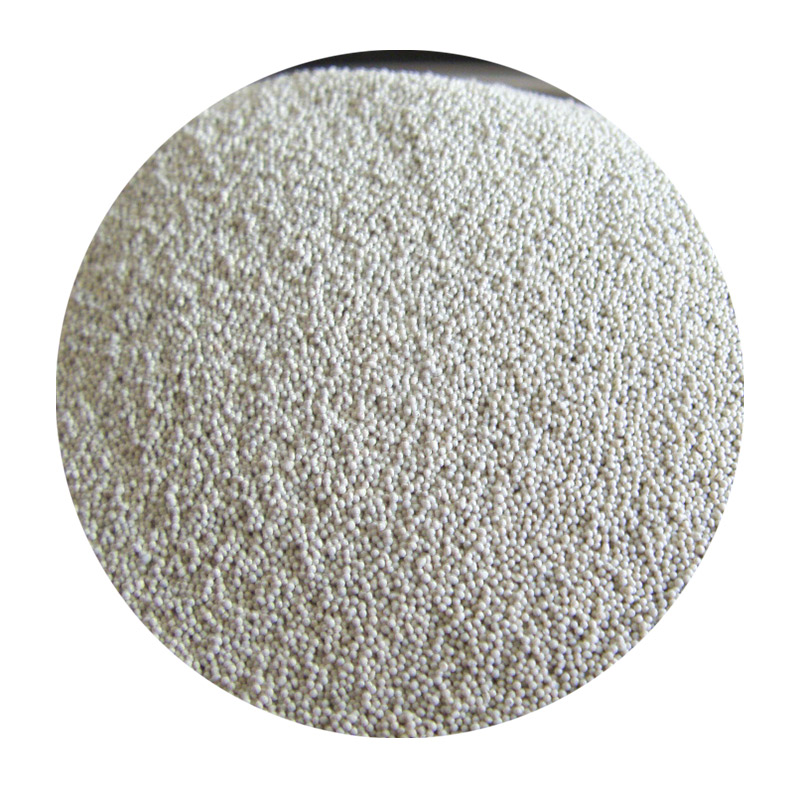
Once the mold is prepared, molten stainless steel is poured into the cavity. The pouring process must be carefully controlled to prevent defects such as air pockets or uneven surfaces. After the metal solidifies, the sand mold is broken away, revealing the cast stainless steel component. The casting may then undergo several finishing processes, including grinding, polishing, and machining, to meet specific tolerances and surface finishes required by the customer.
Quality control is paramount in a stainless steel sand casting foundry. Rigorous testing methods, such as X-ray inspections and tensile strength evaluations, are employed to ensure that the castings meet industry standards and customer specifications. Furthermore, advances in technology, including 3D printing of molds and computer-aided design (CAD), are enhancing the precision and efficiency of the sand casting process.
The economic advantages of utilizing stainless steel sand casting are significant. Compared to other manufacturing techniques, such as die casting, sand casting requires much lower upfront investment in tooling, making it an attractive option for both startups and established manufacturers. Additionally, the recycling potential of stainless steel enhances its sustainability credentials, aligning with growing environmental concerns in the industry.
In conclusion, the stainless steel sand casting foundry plays an essential role in the production of high-quality components across various sectors. Its ability to handle complex shapes, coupled with the durability and resistance properties of stainless steel, ensures that manufacturers can meet the demands of modern applications. As technology continues to evolve, the future of stainless steel sand casting looks promising, poised to provide innovative solutions for a range of industries.
Post time:Noy . 04, 2024 11:22
Next:Exploring the Potential of Sand 3D Printing for Innovative Applications and Sustainable Solutions