Sand Casting of Stainless Steel An Overview
Sand casting is one of the oldest and most versatile metalworking processes available, utilized extensively for manufacturing complex components across various industries. When it comes to stainless steel, sand casting offers unique advantages that make it a preferred choice in producing durable and intricate parts.
What is Sand Casting?
Sand casting involves creating a mold from sand, which is then used to shape molten metal. The process begins with the creation of a pattern, which resembles the final product in shape and size. This pattern is inserted into a sand mixture, typically composed of silica sand, clay, and water, creating a negative impression. After removing the pattern, the mold is ready for the molten stainless steel. The steel is then poured into the mold cavity, allowed to cool and solidify, and then the mold is broken away to reveal the finished component.
Advantages of Using Stainless Steel
Stainless steel is renowned for its excellent corrosion resistance, high strength-to-weight ratio, and aesthetic appeal. When combined with sand casting, these properties are effectively harnessed. Stainless steel parts produced through sand casting exhibit superior durability and can withstand extreme environments, which is particularly beneficial in industries like aerospace, automotive, and marine applications.
Another significant advantage is the ability to produce large and complex shapes. The flexibility of sand casting allows manufacturers to create intricate designs that would be difficult or impossible to achieve with other manufacturing methods. This capability is especially important for custom components that require precise specifications.
sand casting stainless steel
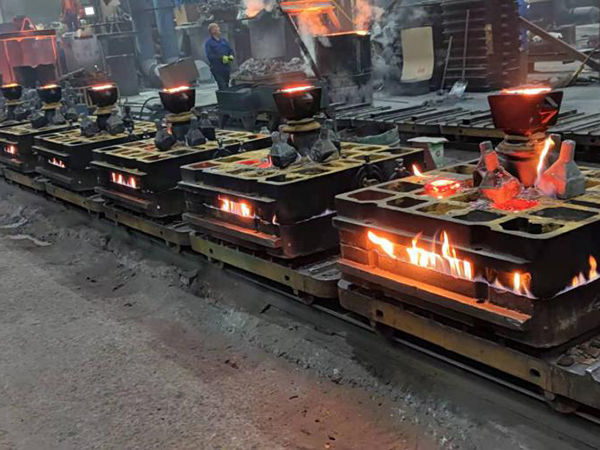
Applications of Sand Cast Stainless Steel
Sand cast stainless steel components are used in various applications, including pumps, valves, automotive parts, and machinery components. For example, many manufacturers prefer sand-cast stainless steel for pump housings and impellers because of their ability to resist corrosion and maintain structural integrity under high pressure and temperature conditions.
In addition, industries requiring high-performance components that can withstand harsh environments, such as oil and gas, often rely on sand-cast stainless steel due to its robustness and reliability. The versatility and adaptability of this casting method also allow for low-volume production runs without significant changes to tooling.
Challenges and Considerations
While sand casting of stainless steel has numerous benefits, it is not without challenges. Controlling the cooling rate is crucial to prevent defects such as warping or cracking. Additionally, ensuring the right composition of the sand mixture is essential for achieving the desired surface finish and structural properties. Manufacturers must also be mindful of the potential for gas entrapment in the mold, which can affect the integrity of the final product.
Conclusion
In summary, sand casting stainless steel is a valuable manufacturing technique that offers numerous advantages, including cost-effectiveness, design flexibility, and excellent material properties. Its applications span various industries, making it an indispensable process for creating high-quality components that meet demanding specifications. As technology continues to advance, the future of sand casting in stainless steel production looks promising, paving the way for even more innovative applications.
Post time:Noy . 19, 2024 23:46
Next:foundry sand properties