The Role of Sand Casting Foundries in Modern Manufacturing
Sand casting is one of the most prevalent manufacturing processes in the world, known for its versatility and cost-effectiveness. Sand casting foundries play a pivotal role in a variety of industries, including automotive, aerospace, marine, and even art. This article will explore the significance of sand casting foundries, the sand casting process, their benefits, and the challenges they face in today's rapidly evolving manufacturing landscape.
Understanding the Sand Casting Process
The sand casting process begins with the creation of a mold. Typically, the mold is made from a mixture of sand and a binding agent, which can be silica sand, clay, or resin. The foundry crafts two halves of the mold, which are then assembled. Once the mold is ready, molten metal is poured into the cavity, filling it to create the desired shape. After the metal has cooled and solidified, the mold is broken away, revealing the finished casting.
Benefits of Sand Casting Foundries
1. Cost-Effectiveness One of the most significant advantages of sand casting is its low cost relative to other manufacturing processes. The materials used are inexpensive, and the production of molds does not require the extensive tooling that methods such as die casting necessitate. This makes sand casting particularly advantageous for low to medium production volumes.
2. Design Flexibility Sand casting allows for the creation of complex shapes that might be challenging to achieve with other techniques. This flexibility enables engineers and designers to innovate and create components tailored to specific requirements without significant redesign costs.
3. Material Compatibility Sand casting can work with a wide range of metals, including aluminum, bronze, iron, and steel. This versatility opens up opportunities for various applications across multiple industries, enhancing the foundries' adaptability.
4. Large Part Production Sand casting is particularly suitable for producing large parts, such as engine blocks and housings. The ability to create sizable components without the risks of thermal distortion is a critical advantage for many industries.
sand casting foundries
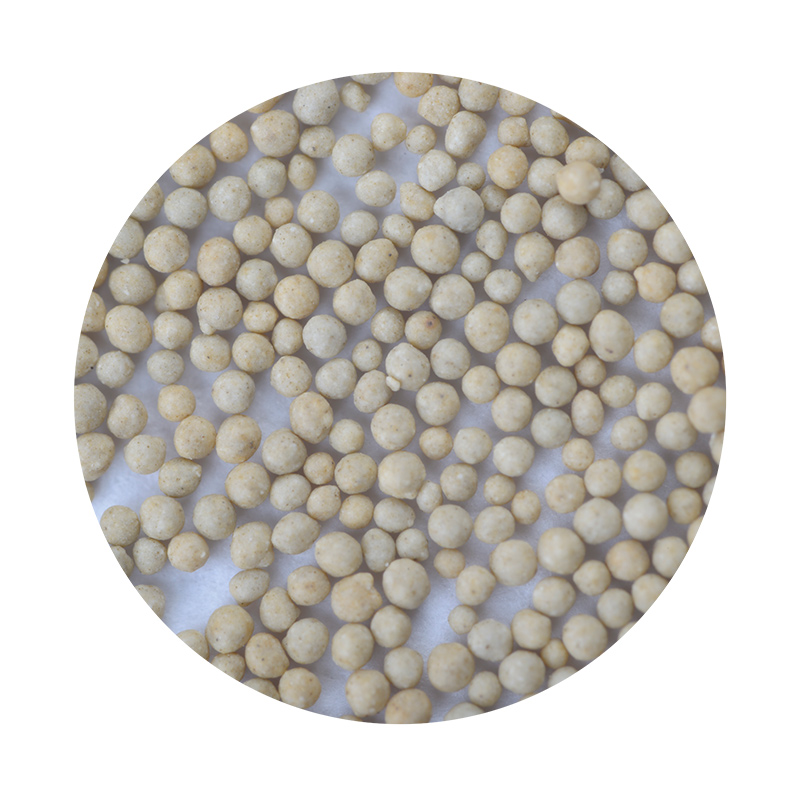
Challenges Facing Sand Casting Foundries
While there are numerous benefits to sand casting foundries, they also face several challenges in a fast-paced manufacturing environment
1. Environmental Regulations Modern foundries are subjected to strict environmental regulations concerning emissions and waste disposal. The process can produce silica dust and other pollutants, necessitating the need for advanced filtration and venting systems. Compliance with these regulations can lead to increased operational costs.
2. Labor Intensive The sand casting process can be labor-intensive, requiring skilled workers for molding and quality control. There is a growing concern about the availability of skilled labor in the industry as the workforce ages and younger generations turn towards more technology-focused careers.
3. Quality Control Achieving consistent quality in sand casting can be challenging. Factors such as moisture content in sand, the temperature of the molten metal, and cooling rates can affect the final product's properties. Implementing rigorous quality control measures is essential to producing high-quality castings.
4. Competition from Advanced Manufacturing Technologies As industries invest more in automation and advanced manufacturing technologies like 3D printing and precision machining, traditional sand casting foundries may struggle to compete. However, many foundries are adapting by integrating new technologies into their processes to enhance efficiency and maintain competitiveness.
Conclusion
In summary, sand casting foundries play an essential role in modern manufacturing. Their ability to produce complex, cost-effective components using a variety of materials ensures their continued relevance in various industries. However, to thrive in today's competitive landscape, these foundries must adapt to challenges such as environmental regulations, labor shortages, and emerging technologies. By embracing innovation and investing in workforce development, sand casting foundries can continue to serve as a backbone for manufacturing and contribute to the advancement of modern industrial practices.
Post time:Noy . 25, 2024 14:51
Next:Sanding Techniques for Achieving Smooth Finishes on Glazed Ceramics