Understanding Resin Sand Characteristics, Applications, and Advantages
Resin sand, a crucial material in modern foundry practices, has garnered attention due to its exceptional properties and versatility. This innovative sand type is primarily a mixture of silica sand and a resin binder, which provides unique features that enhance casting quality and efficiency. In this article, we will delve into the characteristics, applications, advantages, and challenges associated with resin sand in foundry operations.
Characteristics of Resin Sand
The standout feature of resin sand lies in its composition. Typically, the silica sand is treated with a thermosetting resin, most commonly phenolic or furan resins. This binding agent plays a pivotal role in enhancing the sand’s cohesiveness, allowing it to maintain its shape during the casting process. Additionally, resin sand exhibits low thermal expansion, which minimizes defects in the final cast products. This property makes it an excellent choice for producing intricate shapes and designs that require a high degree of dimensional accuracy.
Another notable characteristic is the rapid curing time. The chemical reaction initiated by the addition of a curing agent allows the sand to harden quickly, reducing the time required for mold preparation. This efficiency is particularly advantageous in high-production environments, where time and precision are crucial.
Applications of Resin Sand
Resin sand is widely used across various industries, including automotive, aerospace, and general manufacturing. Its ability to produce high-quality castings with smooth surface finishes makes it particularly popular in sectors that require precision components. For instance, manufacturers of engine blocks and cylinder heads rely on resin sand to achieve the complex geometries and tight tolerances necessary for optimal performance.
Furthermore, resin sand is also employed in investment casting and shell molding processes. In these applications, the sand is used to create molds that can withstand high temperatures, allowing for the casting of materials such as aluminum, iron, and steel. This versatility opens up a wide range of possibilities for manufacturers seeking to optimize their production capabilities.
Advantages of Resin Sand
resin sand
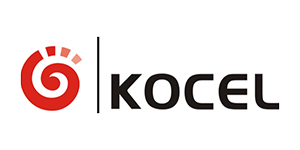
One of the primary advantages of resin sand is its superior surface finish compared to traditional green sand casting. The smoothness of the mold surface translates into a reduced need for extensive machining of the final product, which can significantly lower production costs and time.
Moreover, the mechanical properties of castings produced using resin sand are exceptional. The molds provide excellent dimensional stability, resulting in reduced variability in the final cast parts. This predictability is invaluable for industries where precision is paramount, as it ensures that the components fit together seamlessly without the need for costly adjustments.
Another benefit is the environmental aspect. Unlike some traditional binding agents, many resins used in resin sand systems are non-toxic and produce less airborne dust during handling. This characteristic aligns with the increasing emphasis on sustainable manufacturing practices and workplace safety.
Challenges of Resin Sand
Despite its many advantages, the use of resin sand is not without challenges. One significant drawback is the cost. The raw materials and processing methods for resin sand can be more expensive compared to conventional sand systems. For smaller foundries with tight budgets, this might present a barrier to adoption.
Additionally, the disposal and recycling of used resin sand can pose environmental concerns. The resins used may require specific disposal methods to prevent pollution, which necessitates additional operational considerations for foundries aiming to maintain compliance with environmental regulations.
Conclusion
In conclusion, resin sand stands out as a transformative material in the foundry industry. Its unique characteristics, combined with broad applications and notable advantages, make it an attractive choice for manufacturers aiming to improve casting quality and efficiency. While challenges related to cost and environmental impact exist, the benefits of resin sand often outweigh these drawbacks, reinforcing its status as a key player in modern manufacturing processes. As technology progresses, it is likely that continued innovations will further enhance the efficiency and sustainability of resin sand applications in the foundry sector.
Post time:Dek . 13, 2024 11:58
Next:3d printed sand