Understanding the Materials Used in Sand Casting
Sand casting is one of the oldest and most widely used manufacturing processes, particularly for producing complex metal parts. Its adaptability and cost-effectiveness have made it a popular choice across various industries, including automotive, aerospace, and artistic applications. This article will explore the primary materials used in sand casting and their roles in achieving high-quality castings.
1. Sand
The fundamental material in sand casting is, of course, sand itself. The type of sand used is typically a mixture of silica (SiO2), clay, and water, which ensures that the mold maintains its shape during the casting process. The most common type of sand used is green sand, which is a mixture of silica sand, clay, and moisture. The clay acts as a binder, giving the mold its strength, while water helps to activate the clay, allowing it to form a stable structure.
Another type of sand used is silica sand, which is pure silica without clay or other additives. Silica sand has excellent thermal properties, allowing it to withstand the high temperatures associated with molten metals. However, silica sand is often used more in investment casting or other processes where a finer finish is required.
2. Binder Materials
Binders play a crucial role in sand casting by enhancing the cohesiveness of the sand particles. In green sand, clay serves as the primary binder. However, in some advanced processes, chemical binders such as phenolic urethanes, furan, or thermosetting resins may be used. These chemicals improve the strength and durability of the mold, allowing for finer details and reducing defects in the final casting. The choice of binder can significantly influence the performance of the mold, including its ability to withstand the thermal shock during pouring.
3. Metal Alloys
Metal alloys are the most critical consumable materials in the sand casting process. The selection of metal depends on the specific requirements of the application, including strength, weight, corrosion resistance, and thermal properties. Common alloys used in sand casting include aluminum, iron, bronze, and magnesium.
- Aluminum Alloys These are lightweight and have excellent corrosion resistance
. They are often used in automotive and aerospace applications due to their strength-to-weight ratio.what materials are used in sand casting
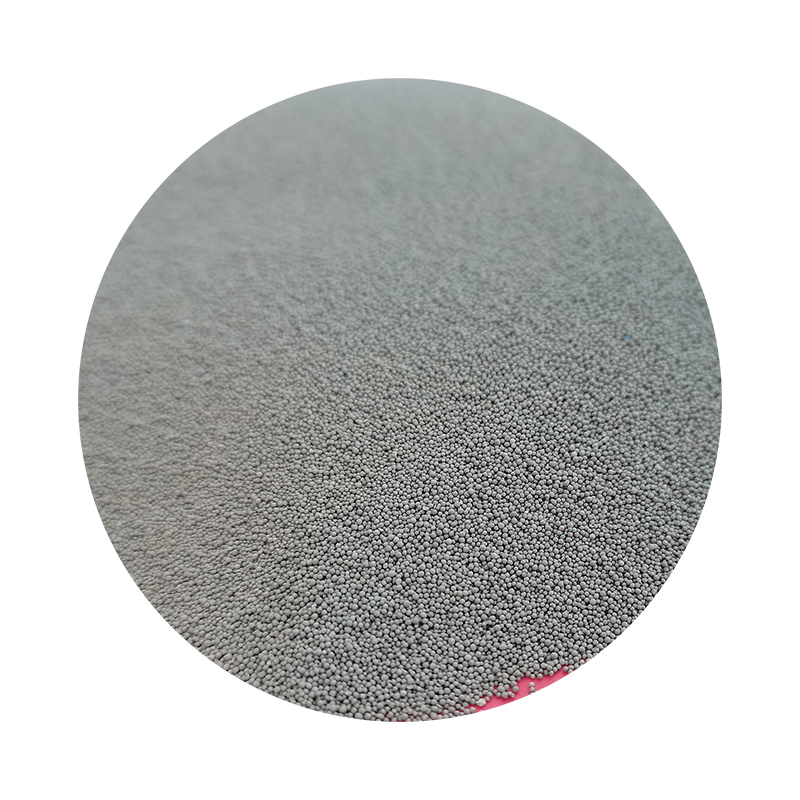
- Iron Alloys Cast iron is traditional in sand casting due to its excellent castability and strength. Gray iron, ductile iron, and malleable iron are frequently used, depending on the desired mechanical properties.
- Bronze Alloys Known for their high resistance to corrosion and wear, bronze alloys are often used in marine and architectural applications.
- Magnesium Alloys These are the lightest structural metals available and are used in applications that require significant weight savings, such as in aerospace components.
4. Coatings
Coatings are used to enhance the quality of the cast and to protect the mold from the molten metal. They help reduce the occurrence of defects such as sand inclusions or surface imperfections. Common coatings include graphite, which provides a lubricating effect, and other refractory materials that can improve thermal stability. These coatings can enhance the surface finish and dimensional accuracy of the casting.
5. Additives
Finally, various additives can be included in the sand mixture to modify characteristics such as permeability, strength, and moisture retention. Common additives include sodium silicate, which improves dimensional stability, and various drying agents to control moisture levels.
Conclusion
In conclusion, understanding the materials used in sand casting is integral to producing high-quality castings. From the choice of sand and binder materials to the selection of metal alloys and coatings, each component plays a vital role in the overall success of the casting process. The versatility of sand casting, combined with the appropriate selection of materials, enables manufacturers to create a wide range of products tailored to specific needs, making it an essential process in modern manufacturing. As industry demands evolve, the continued innovation in materials will further enhance the capabilities and applications of sand casting.
Post time:نومبر . 25, 2024 15:16
Next:Specification Guidelines for Resin Coated Sand Applications in Industries