Understanding Sand Casting Technique
Sand casting, also known as sand mold casting, is a widely utilized method in manufacturing that can produce a variety of metal parts. This technique has been in existence for centuries and continues to be a critical process in the foundry industry due to its versatility, cost-effectiveness, and ability to produce intricate designs.
Fundamentals of Sand Casting
The sand casting process involves creating a mold from a mixture of sand and a binding agent, typically clay, which has the ability to retain its shape. The basic steps of sand casting include pattern making, mold preparation, pouring, solidification, and finishing.
1. Pattern Making The first step in sand casting is to create a pattern of the desired object. This pattern, which can be made from materials such as wood, metal, or plastic, is a replica of the final product. It is essential for the pattern to include allowances for shrinkage and the finishing processes.
2. Mold Preparation Once the pattern is ready, it is pressed into a sand mixture to form a mold. The sand is typically mixed with a binding agent to enhance its cohesiveness. After making the mold, the pattern is removed, leaving a cavity that corresponds to the object to be cast. This process can be performed using either a single-part or multi-part mold, depending on the complexity of the object.
3. Pouring After preparing the mold, molten metal is poured into the cavity. The choice of metal generally depends on the application and can range from aluminum, cast iron, to bronze. Care must be taken to ensure that the metal is at the optimal pouring temperature so as to avoid defects such as cold shuts or porosity.
4. Solidification Once the molten metal is poured into the mold, it begins to cool and solidify. The cooling rate can vary based on several factors, including the type of metal used and the thickness of the cast. Proper cooling is essential to prevent defects and ensure the mechanical properties of the final product.
5. Finishing After the metal has solidified, the mold is broken away to reveal the casting. The cast part often requires additional finishing processes, such as grinding, sanding, and machining, to achieve the desired surface finish and dimensions.
sand casting technique
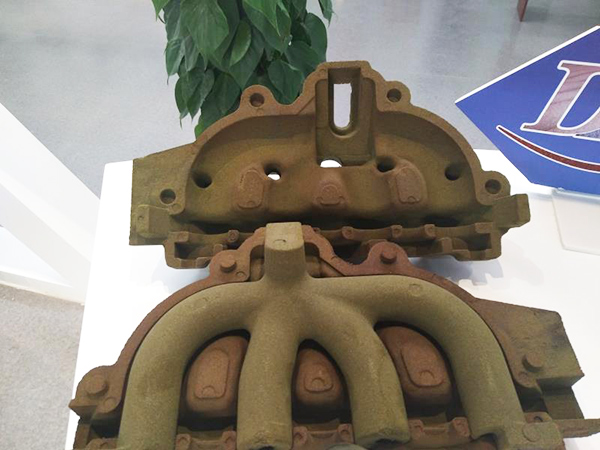
Advantages of Sand Casting
One of the most significant advantages of sand casting is its adaptability. This method can accommodate a wide range of metals and alloys, making it suitable for various applications across industries, including automotive, aerospace, and machinery. It is particularly effective for producing large or complex geometric shapes that would be difficult or impossible to achieve with other manufacturing methods.
Additionally, sand casting is cost-effective for both small and large production runs. The materials used for the sand molds are relatively inexpensive compared to those required for other types of molds. Moreover, the molding sand can often be reused, which further reduces operational costs.
Challenges in Sand Casting
Despite its benefits, sand casting also presents several challenges. The quality of the final product can be influenced by the mold's integrity, and the presence of sand inclusions or gas porosity can lead to defects in the casting. Additionally, the finishing process can be time-consuming and may add to the overall cost of production.
Furthermore, while sand casting is versatile, it may not be suitable for high-precision parts where tight tolerances are required. In such cases, processes like investment casting or die casting might be more appropriate.
Conclusion
In summary, sand casting is a fundamental manufacturing technique that has stood the test of time due to its effectiveness and versatility. It allows for the production of complex parts in various materials, catering to diverse industrial needs. While it does have its limitations, ongoing advancements in technology and materials continue to enhance the quality and efficiency of sand casting, ensuring its relevance in modern manufacturing practices. Whether used in mass production or small-scale applications, sand casting remains an invaluable method in the world of metallurgy and manufacturing.
Post time:دسمبر . 19, 2024 20:38
Next:sand cast iron