Understanding Sand Casting and Its Materials
Sand casting is one of the oldest and most widely used methods of metal casting. It involves pouring liquid metal into a mold made of sand, where it solidifies and takes the shape of the mold. This process is favored for its simplicity, cost-effectiveness, and versatility in producing intricate shapes. A pivotal component in sand casting is the sand itself, with various types of sand being utilized for different casting needs.
The Role of Sand in Casting
In sand casting, the sand serves as the primary mold material. It must possess certain properties to be effective, including grain size, shape, and permeability. The most commonly used sand is silicon dioxide, or silica sand, which has excellent thermal stability and can withstand the high temperatures of molten metal. The sand is typically mixed with a binder to form a cohesive mold that can hold its shape during the casting process.
One of the most popular binders used in sand casting is clay, which helps bind the sand grains together. The type and amount of clay can affect the hardness and strength of the mold. Other additives, such as water and chemicals, may also be included to enhance the mold's properties, such as improving its ability to hold fine details and preventing cracking during the cooling process.
Types of Sand for Casting
While silica sand is predominant, other types of sand can also be used in specific applications. For instance, olivine sand is sometimes preferred for its lower thermal expansion and better resistance to metal penetration. This can be particularly advantageous when casting non-ferrous metals. Alternatively, zircon sand is used for high-temperature applications due to its superior thermal properties and lower thermal expansion rate.
sand casting sand
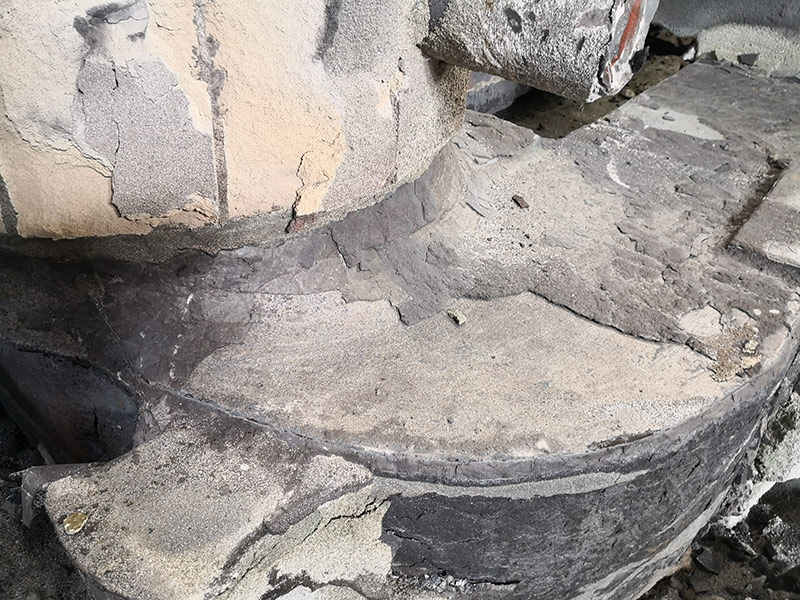
Reclaiming used sand is an essential aspect of modern sand casting. Recyclable sand can be cleaned and reused for multiple casting cycles, reducing waste and lowering production costs. Efficient recycling practices have led to advancements in the sustainability of casting operations, which is an increasingly important factor in manufacturing.
Advantages of Sand Casting
The versatility of sand casting allows for the production of a wide variety of shapes and sizes, from small intricate components to large heavy parts. This method can accommodate various metal alloys, including iron, aluminum, and bronze, making it adaptable to diverse industries, such as automotive, aerospace, and art.
One of the key advantages of sand casting is its relatively low cost, especially for low-volume production. The materials required for sand molds are inexpensive, and the process can be carried out in both small-scale workshops and large industrial facilities.
Conclusion
In summary, sand casting is a crucial manufacturing process that relies heavily on the properties and types of sand used. The choice of sand and binders impacts the quality and characteristics of the final product, making it essential for manufacturers to select the appropriate materials for their specific needs. As the industry continues to evolve, innovations in sand casting materials and techniques will further enhance the efficiency and sustainability of this time-honored method of metal formation.
Post time:نومبر . 04, 2024 09:48
Next:lost-foam casting