The Sand Casting Process A Comprehensive Overview
Sand casting, also known as sand mold casting, is one of the most widely utilized casting processes in manufacturing. This versatile method is especially favored for its ability to produce complex shapes using a wide range of metals. The process relies on sand as the key molding material and has been in use for centuries, dating back to ancient civilizations where simple metalwork was essential for toolmaking and art.
The sand casting process begins with creating a mold. A two-part mold is typically made from coarse, granular sand mixed with a binding agent, often clay, and water. This mixture forms a durable and heat-resistant mold that can withstand the high temperatures of molten metal. The first step involves creating a pattern that is an exact replica of the final product. The pattern is usually made from metal, plastic, or wood, and it is often oversized to accommodate for the shrinkage that occurs as the metal cools.
Once the pattern is ready, it is placed in a sand mixture to form the mold. The sand is compacted around the pattern, ensuring that every detail is captured. After the sand has been adequately compacted, the pattern is removed, leaving a cavity in the shape of the intended final product. This cavity is where the molten metal will be poured.
The next step involves preparing the molten metal, which must be heated to a temperature sufficient for it to flow easily into the mold. Common metals used in sand casting include aluminum, steel, iron, and brass. The choice of metal depends on the desired properties of the final product, including strength and corrosion resistance.
sand casting process
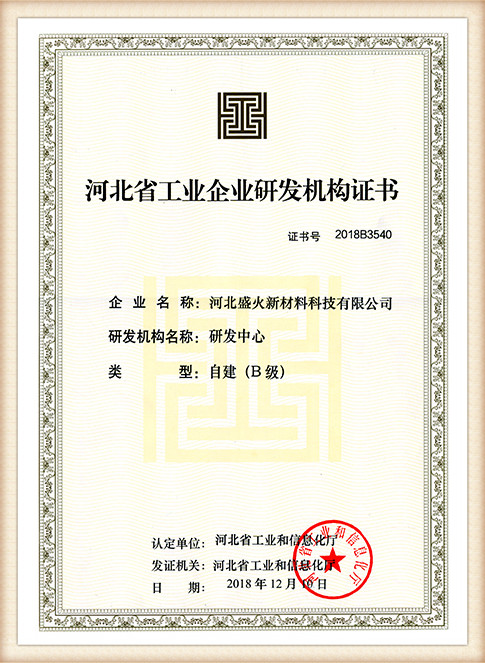
Once the metal reaches its optimal temperature, it is poured into the mold through a gating system. This system is designed to allow the molten metal to flow smoothly while minimizing turbulence to prevent defects. The metal fills the cavity in the mold, and the cooling process begins. It is crucial to monitor the cooling time closely, as it affects the mechanical properties and surface finish of the casting.
After the metal has cooled and solidified, the next phase involves breaking away the sand mold to reveal the cast part. This is often done with vibratory shakeout machines or manually, depending on the scale of production. The cast components typically require finishing processes, such as grinding or machining, to achieve the required specifications and surface quality.
Sand casting is renowned for its flexibility, allowing the production of small to large parts, and its cost-effectiveness, particularly for low to medium volume manufacturing. Despite advancements in modern manufacturing techniques, sand casting remains a cornerstone of industry, valued for its ability to create intricate designs and durable components. Applications range from automotive and aerospace parts to decorative items and art sculptures, demonstrating the process's remarkable adaptability and enduring relevance in the manufacturing world.
In summary, sand casting is an essential process in the realm of metalworking that combines artistry with engineering, making it a vital method for producing diverse and complex metal components.
Post time:نومبر . 05, 2024 00:39
Next:materials used for sand casting