Understanding Sand Casting A Comprehensive Overview
Sand casting is one of the oldest and most widely used metal casting processes in the manufacturing industry. This method, also known as sand mold casting, involves creating a mold from sand and then pouring molten metal into that mold to produce a variety of metal parts and components. The simplicity and versatility of sand casting make it an attractive option for manufacturers across different sectors.
The Process of Sand Casting
The sand casting process begins with the preparation of the mold. The mold consists of two halves, typically made from a mixture of sand, clay, and water. This mixture gives the mold its ability to hold shape and withstand the high temperatures of molten metal. The core ingredient, sand, is chosen for its properties; it should have good strength, permeability, and the ability to retain shape when compacted.
The first step is to create a pattern, which is a replica of the final product. Patterns are usually crafted from metal, wood, or plastic and are slightly larger than the final part due to the shrinkage that occurs when the metal cools. The pattern is used to imprint the shape into the sand mix, which forms the mold.
Once the pattern is inserted into the sand, the sand is compacted around it, creating the mold cavity. The two halves of the mold are then assembled, making sure to align any necessary sprue and riser systems. The sprue allows the molten metal to enter the mold, while risers serve as reservoirs that help accommodate the shrinkage of the metal as it solidifies.
After the mold is prepared, it is heated using a furnace, and the chosen metal is melted until it reaches its liquid state. Common metals used in sand casting include iron, aluminum, and bronze. Once the metal is molten, it is poured into the mold through the sprue. Care must be taken to control the pouring temperature and speed to avoid defects in the casting.
The final step is to allow the metal to cool and solidify, which can take anywhere from several minutes to hours, depending on the size of the casting. After the casting has cooled, the mold is broken away to reveal the finished part. The process of removing the excess sand and any adhering material is called shakeout.
sand casting description
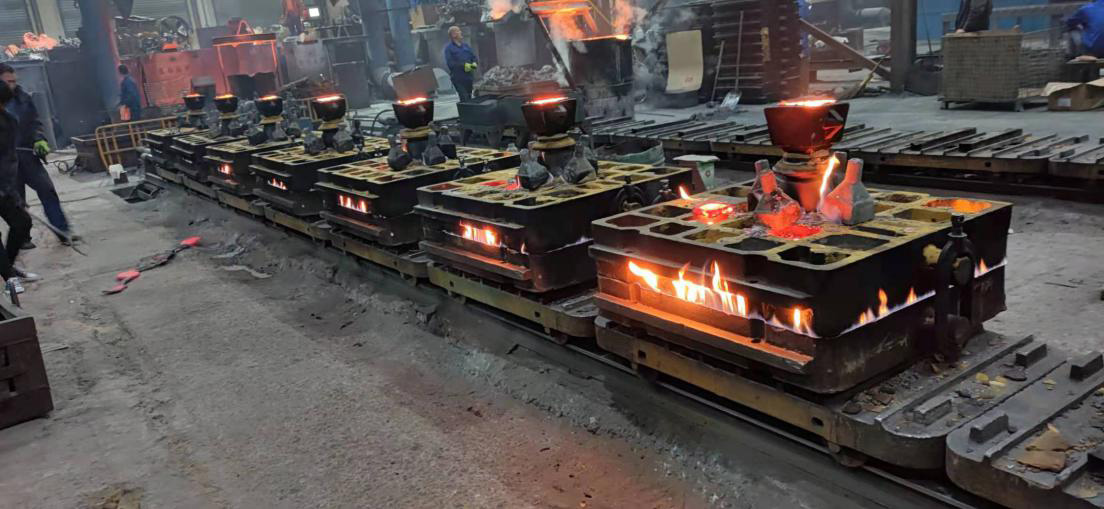
Advantages of Sand Casting
One of the primary advantages of sand casting is its ability to produce complex shapes that would be difficult or impossible to achieve with other methods. The materials used in sand casting are also inexpensive and readily available, making it a cost-effective choice for both small and large production runs.
Sand casting is highly versatile and can accommodate a broad range of metal types and part sizes. Additionally, it is suitable for both ferrous and non-ferrous metals, allowing manufacturers to select the right material for their specific application.
Limitations of Sand Casting
Despite its many benefits, sand casting has some limitations. The surface finish of sand cast parts is generally rougher compared to those produced by other methods like die casting or investment casting. This may require additional machining processes to achieve the desired surface quality.
Moreover, the dimensional tolerance of sand castings is typically less precise, which may not be acceptable for certain high-precision applications. It is essential for manufacturers to weigh these factors when deciding on the casting process.
Conclusion
Sand casting remains a vital method in the manufacturing landscape, especially for creating large machined components and intricate shapes at a relatively low cost. Understanding the intricacies of the sand casting process allows manufacturers to harness its full potential and produce high-quality components that meet their specific needs. As technology progresses and new innovations emerge within the industry, sand casting will continue to evolve, demonstrating its enduring value.
Post time:نومبر . 30, 2024 09:40
Next:Golden Sands Properties Available for Purchase