Rapid Sand Casting An Innovation in Metal Casting Technology
Rapid sand casting has emerged as a revolutionary technique in the field of metal casting, combining traditional sand casting methods with the latest advancements in technology. This innovative approach allows for faster production times, reduced costs, and improved design flexibility, making it ideal for industries requiring high-quality metal components, such as automotive, aerospace, and consumer goods.
Understanding Sand Casting
Sand casting is one of the oldest and most widely used casting processes. It involves creating a mold from sand to form an object by pouring molten metal into the mold cavity. Traditional sand casting, while effective, can be time-consuming due to the long waiting periods for the mold to be produced and the need for meticulous finishing processes post-casting. Rapid sand casting addresses these limitations by streamlining the mold-making process.
The Process of Rapid Sand Casting
The rapid sand casting process typically begins with the creation of a 3D computer model of the desired component. This 3D model is then used to create a mold through advanced techniques such as 3D printing or CNC machining. 3D printing, in particular, allows for highly intricate mold designs that would be difficult or impossible to achieve using traditional methods.
Once the mold is created, molten metal is poured into the sand mold, allowing it to take shape as it cools and solidifies. The speed of the mold production and the casting process significantly reduces the overall lead time, enabling manufacturers to respond quickly to market demands and prototype development.
Advantages of Rapid Sand Casting
1. Speed One of the most significant advantages of rapid sand casting is the reduction in time required to produce both molds and castings. This acceleration allows companies to shorten their product development cycles and bring products to market more quickly.
rapid sand casting
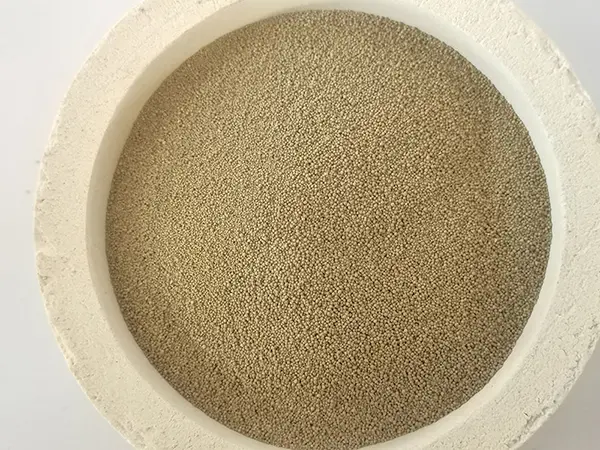
2. Cost-effectiveness The streamlined process results in lower production costs. Reduced lead times mean that manufacturers can save on labor and materials, making rapid sand casting a cost-effective solution for both small and large production runs.
3. Design Flexibility Rapid sand casting allows for greater design freedom. Complex geometries that were once difficult to produce can now be easily achieved, enabling designers to innovate without the constraints imposed by traditional casting methods.
4. Reduced Waste The precision of 3D printing and modern machining techniques can result in less waste material compared to traditional sand casting processes. This not only contributes to environmental sustainability but also results in additional cost savings.
5. Improved Quality The ability to produce molds quickly and with high accuracy leads to improved surface finishes and dimensional accuracy in the final cast product. This is particularly important in industries where high-performance components are critical.
Applications of Rapid Sand Casting
Rapid sand casting is particularly beneficial in several applications. In the automotive industry, it allows for the rapid prototyping of engine components, brackets, and housings. In aerospace, where weight and precision are crucial, rapid sand casting can generate components that meet rigorous safety and performance standards. Furthermore, the consumer goods industry increasingly relies on rapid sand casting for producing unique and custom designs that cater to specific consumer preferences.
Conclusion
In conclusion, rapid sand casting represents a significant advancement in the metal casting industry. It merges traditional techniques with modern technology, resulting in faster production, cost savings, and enhanced design possibilities. As industries continue to evolve, the methods used to produce components must also adapt. Rapid sand casting stands at the forefront of this change, providing manufacturers with the tools necessary to thrive in a competitive marketplace. With its numerous advantages, it is poised to become a fundamental technique for the future of manufacturing.
Post time:دسمبر . 20, 2024 22:52
Next:sanding for 3d printing