The Foundry Sand Casting Process A Comprehensive Overview
Sand casting is one of the oldest and most widely used metal casting processes in manufacturing. It involves creating a mold from sand, which is then filled with molten metal to produce a desired shape. The foundry sand casting process is known for its versatility, cost-effectiveness, and ability to produce complex geometries, making it a preferred choice in various industries, including automotive, aerospace, and machinery.
Understanding the Basics of Sand Casting
The fundamental principle of sand casting is quite straightforward. It begins with a pattern, which is a replica of the object to be cast. This pattern can be made from various materials such as wood, metal, or plastic. The pattern is then placed into a molding material, typically a mixture of sand and a binding agent, to create a mold. Once the sand has been packed tightly around the pattern, it is removed, leaving a cavity in the shape of the pattern.
There are two primary types of sand molds green sand molds and dry sand molds. Green sand molds use moist sand, while dry sand molds are baked in an oven to harden them before casting. Each type has its advantages, with green sand being more common due to its ease of use and cost-effectiveness.
The Process Steps
1. Pattern Making The first step in the sand casting process is creating a pattern. Precision in the patterning is crucial since any imperfections will be reflected in the final casted product.
2. Mold Preparation Once the pattern is ready, the next step is to prepare the sand mold. This involves mixing silica sand with a binding agent (usually clay) and water. The mixture is packed around the pattern to form two halves of the mold, known as the cope (top half) and the drag (bottom half).
3. Mold Assembly After the sand has been sufficiently compacted around the pattern, the two halves of the mold are carefully assembled. The mold may include additional features such as risers and vents to allow for proper filling and escape of gases during the pouring of molten metal.
foundry sand casting process
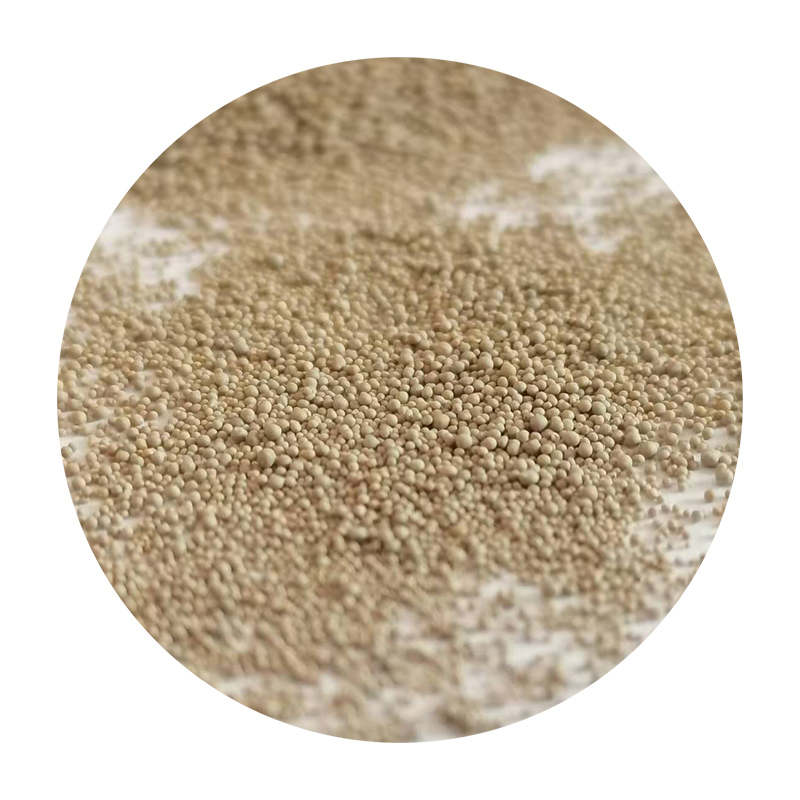
4. Melting Metal The next step involves melting the desired metal. Common metals used in sand casting include aluminum, iron, and bronze. The molten metal reaches high temperatures and is poured into the mold.
5. Pouring Once the metal is melted, it is carefully poured into the prepared mold cavities. This step must be executed with precision to ensure that the mold is filled without creating defects such as air pockets.
6. Cooling After pouring, the molten metal is allowed to cool and solidify within the mold. The cooling time varies based on the type of metal and the complexity of the casting.
7. Mold Removal and Finishing Once the metal has cooled sufficiently, the sand mold is broken away to reveal the cast part. Any remaining sand is removed, and the casting undergoes finishing processes, which may include grinding, sanding, or machining to achieve the desired surface finish and dimensions.
Advantages of Sand Casting
The sand casting process offers numerous advantages. It is highly adaptable to different metal types and casting shapes, making it suitable for small to large production runs. The process can accommodate complex geometries that might be challenging to produce with other methods. Moreover, the materials used in sand casting are relatively inexpensive, leading to lower overall production costs.
Conclusion
In summary, the foundry sand casting process is a foundational manufacturing technique esteemed for its simplicity, versatility, and cost-effectiveness. By understanding each step, from pattern making to the final finishing, manufacturers can harness the full potential of this method to produce high-quality cast items across various industries. As technology advances, the sand casting process continues to evolve, integrating new materials and techniques to enhance its efficiency and effectiveness in modern manufacturing contexts.
Post time:دسمبر . 05, 2024 02:42
Next:Understanding the Process and Benefits of Sand Casting in Metal Manufacturing