The Role of Foundry Sands in Metal Casting
Foundry sands are a crucial component in the metal casting industry, serving as a primary material for creating molds used in the production of various metal components. These sands are typically made from silica, which is abundant and possesses properties that make it ideal for high-temperature applications encountered in foundries. The use of foundry sands plays a significant role in achieving high-quality castings, ensuring both the integrity and precision of the finished metal products.
One of the main characteristics of foundry sands is their ability to withstand extreme temperatures. When molten metal is poured into a mold, the temperature can reach as high as 1,600 degrees Celsius. Foundry sands possess high thermal stability, allowing them to endure these conditions without compromising their structural integrity. This thermal resistance is crucial for preventing mold deformation, which can lead to defects in the final cast product.
In addition to thermal stability, foundry sands exhibit excellent permeability
. This property allows gases produced during the casting process to escape through the sand mold, thereby preventing defects such as blowholes and gas pockets in the casting. This permeability is a vital factor in achieving clean, defect-free castings, making foundry sands a preferred choice for metal foundries around the world.foundry sands
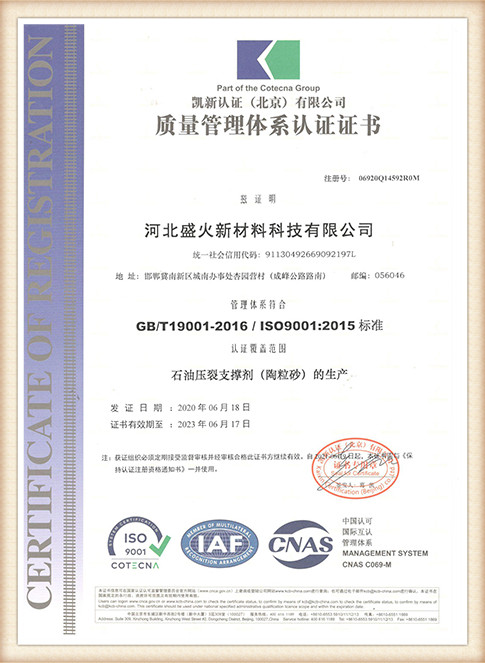
Moreover, foundry sands are typically reusable, which contributes to cost efficiency in the casting process. Once the casting is complete, the sand can be reclaimed, treated, and reused for multiple casting cycles. This not only reduces waste but also minimizes the demand for raw materials, aligning with sustainable manufacturing practices. As industries seek to reduce their environmental impact, the reuse of foundry sands plays a pivotal role in promoting sustainability in the metal casting sector.
The environmental implications of foundry sands extend beyond their reusability. Modern foundry operations often implement technologies to reduce dust and emissions related to sand handling and casting processes. Innovations in sand treatment facilities enhance the quality and durability of foundry sands, further contributing to operational efficiency. Additionally, the development of synthetic sands presents an alternative to traditional natural sands, offering tailored properties that can improve casting performance while reducing reliance on non-renewable resources.
Another aspect of foundry sands is their contribution to the overall quality of castings. The right grade of foundry sand can significantly influence the surface finish and precision of the final product. Different applications may require specific sand characteristics, such as grain size or shape, which can be customized to meet the needs of various casting processes. This adaptability ensures that foundries can produce a wide range of components, from intricate mechanical parts to large industrial components.
In conclusion, foundry sands are an indispensable element of the metal casting industry. Their ability to withstand high temperatures, excellent permeability, reusability, and adaptability make them essential for producing high-quality castings. As innovation continues to evolve within the industry, the role of foundry sands will remain pivotal, supporting both operational efficiency and sustainable practices in metal manufacturing. As the demand for cast metal products grows across various sectors, understanding and optimizing the use of foundry sands will be key to the continued success of foundries worldwide.
Post time:ستمبر . 15, 2024 19:53
Next:sand casting alloys