Understanding the Components of Sand Casting
Sand casting, an ancient metal forming technique, continues to play a vital role in modern manufacturing due to its versatility and cost-effectiveness. The process involves creating a mold from sand into which molten metal is poured to produce various metal components. The fundamental components of sand casting encompass the pattern, core, mold, sand, and binder, among others. Each of these elements plays a critical role in ensuring the quality and accuracy of the final casting.
1. Pattern
The pattern is a replica of the desired finished product and is one of the first components in the sand casting process. Patterns are typically made from materials such as wood, metal, or plastic. When designing a pattern, engineers must consider the shrinkage that occurs as metal cools, as well as allowances for machining. Additionally, the design of the pattern must facilitate easy removal from the mold, which may involve considerations for draft angles and undercuts.
2. Core
Cores are used to create internal features and cavities in a casting. They are usually made of sand that is bonded together with a core binder. The core is inserted into the mold cavity before the molten metal is poured. Effective core design is essential to ensure that the molten metal flows around it and does not alter the intended shape of the external mold. Cores must also be able to withstand the high temperatures of the molten metal without breaking down.
3. Mold
The mold is the container that shapes the molten metal as it cools. In sand casting, the mold is formed from a mixture of sand and binder, which gives it the ability to hold the desired shape. There are two primary types of molds the single-use mold and the reusable mold. Single-use molds, as the name suggests, are made for one casting only, while reusable molds can be used multiple times, which is beneficial for mass production.
components of sand casting
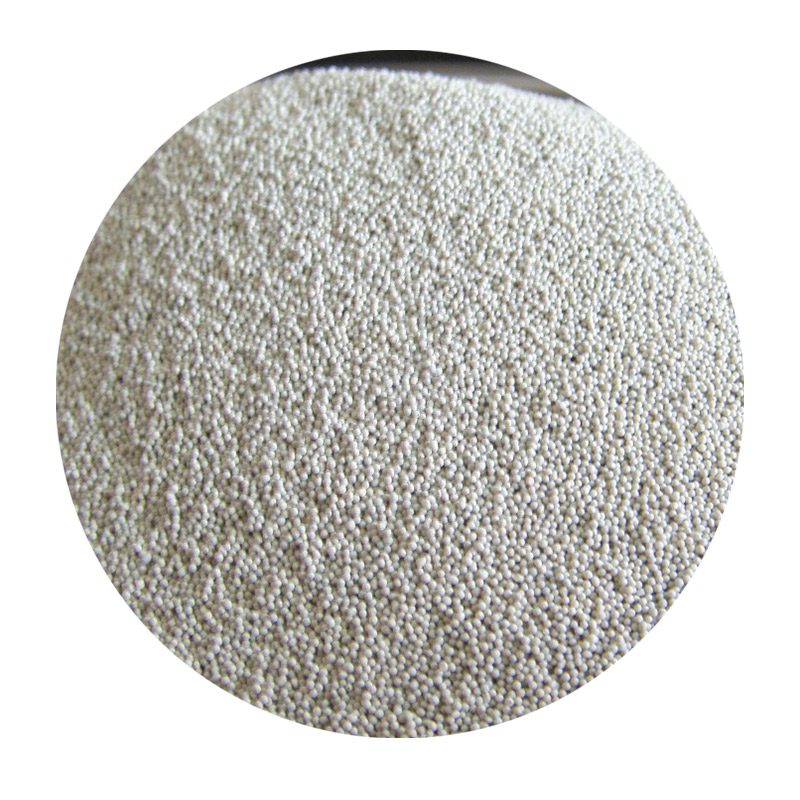
4. Sand
Sand is a critical component in sand casting, serving as the primary material for molds. The choice of sand affects the casting's surface finish, dimensional accuracy, and strength. The most commonly used sand for casting is silica sand due to its excellent heat resistance and availability. The grain size and shape of the sand can also influence the overall quality of the casting. Finer sands yield smoother finishes but may have lower strength compared to coarser sands.
5. Binder
Binders are substances added to sand to enhance its cohesiveness, allowing it to retain shape and form more effectively during the mold-making process. Common binders include clay, resin, and sodium silicate. The choice of binder significantly affects the mold’s strength, permeability, and the final casting’s surface finish. For instance, resin-bonded sands provide superior bonding strength and can handle intricate detailing better than traditional clay-bonded sands.
6. Other Components
In addition to the primary elements mentioned, several other components are essential in the sand casting process. These include the gating system, which directs the flow of molten metal into the mold; risers that allow for the escape of gases and provide additional metal to compensate for shrinkage; and chillers, which can be used to control the cooling rate of certain areas of the casting.
Conclusion
In conclusion, sand casting is a multifaceted process that relies on various components to produce high-quality metal parts. The interplay between the pattern, core, mold, sand, and binder determines the success of a casting operation. By understanding these essential components, engineers and manufacturers can optimize the sand casting process to yield better performance and precision in their final products. As technology evolves, ongoing innovations in materials and techniques promise to enhance the capabilities and applications of sand casting, ensuring its relevance in the manufacturing world for years to come.
Post time:دسمبر . 19, 2024 19:25
Next:foundry sand properties