The Art and Science of Cast Iron Sand Casting
Cast iron sand casting is a fascinating process that combines art and engineering to create intricate metal objects used in various industries. This traditional casting method has been adopted over centuries due to its versatility, cost-effectiveness, and ability to produce complex shapes with a high degree of accuracy. As we delve deeper into this topic, we will explore the history, process, advantages, and applications of cast iron sand casting.
A Brief History
The roots of sand casting can be traced back to ancient civilizations, where artisans would mold molten metals using sand mixed with various binders to create tools, weapons, and decorative items. Cast iron, a durable and versatile alloy primarily made of iron and carbon, emerged during the Iron Age and has since been used for countless applications, including machinery, cookware, and art. The combination of cast iron and sand casting has become a hallmark of industrial production, particularly during the Industrial Revolution when the demand for durable and intricate metal parts surged.
The Sand Casting Process
The process of cast iron sand casting involves several steps
1. Pattern Creation The first step in sand casting is creating a pattern, which is a replica of the object to be cast. Patterns can be made from various materials, including wood, plastic, or metal, and are designed with allowances for shrinkage and machining.
2. Molding The next step involves creating a mold from the pattern. Sand is mixed with a binding agent (such as clay) and then packed around the pattern to form a mold. The pattern is removed, leaving a cavity in the shape of the object. The molding process can be done either manually or with machines, depending on the scale of production.
3. Melting and Pouring Once the mold is ready, cast iron is melted in a furnace at high temperatures, usually exceeding 1400°C (2550°F). After melting, the molten iron is poured into the mold cavity through a gating system. The pouring process requires precision to avoid defects such as air pockets or uneven filling.
4. Cooling After pouring, the molten iron cools and solidifies inside the mold. The cooling time can vary depending on the thickness and complexity of the casting. Proper cooling is crucial to ensure the mechanical properties and quality of the final product.
5. Finishing Once the cast iron has cooled and solidified, the mold is broken away to reveal the casting. Additional finishing processes, such as grinding, machining, and surface treatment, may be performed to achieve the desired dimensions and surface finish.
cast iron sand casting
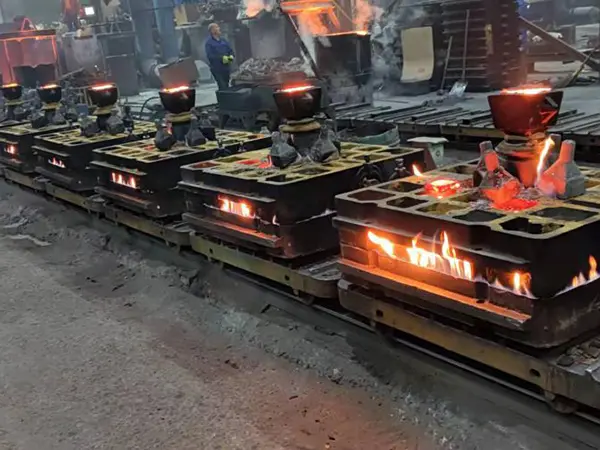
Advantages of Cast Iron Sand Casting
Cast iron sand casting offers numerous benefits
- Cost-Effectiveness The materials used for sand molds are relatively inexpensive, making it a cost-effective option for producing a wide range of parts, especially in bulk.
- Flexibility Sand casting is highly adaptable and can accommodate complex shapes and sizes, making it suitable for creating diverse products, from small components to large machine parts.
- Durability Cast iron is known for its excellent wear resistance, high tensile strength, and ability to withstand high temperatures, making it ideal for applications in various industries, such as automotive and construction.
- Recyclability Unused or scrap sand from the casting process can be recycled, contributing to a more sustainable production cycle.
Applications of Cast Iron Sand Casting
The applications of cast iron sand casting are vast and varied. In the automotive industry, it is commonly used to produce engine blocks, transmission cases, and various other components. In construction, cast iron is often utilized for pipes, manhole covers, and heavy machinery parts. Additionally, the versatility of sand casting allows for the creation of intricate decorative items, such as sculptures and architectural elements.
Conclusion
In conclusion, cast iron sand casting stands as a testament to the enduring synergy between traditional craftsmanship and modern engineering. Its rich history, efficient process, and wide range of applications make it an indispensable method in the manufacturing world. As technology continues to evolve, the fundamental principles of sand casting remain relevant, ensuring that this age-old technique will continue to thrive for years to come.
Post time:نومبر . 05, 2024 06:36
Next:sand casting cost