Applications of Sand Casting Process
Sand casting, one of the oldest and most widely used metal casting processes, involves creating a mold from sand and using it to shape molten metal. Its adaptability, cost-effectiveness, and ability to produce complex shapes make it a preferred method in various industries. This article explores the diverse applications of the sand casting process.
One of the primary applications of sand casting is in the manufacturing of automotive components. The automotive industry relies heavily on sand casting for producing engine blocks, cylinder heads, and transmission cases. These components require high strength and durability, which sand-cast metals can provide. Since vehicles require numerous parts, the ability of sand casting to create large quantities of intricate designs makes it an invaluable manufacturing method.
In addition to automotive manufacturing, the aerospace industry also benefits from sand casting. Critical components such as turbine housings, brackets, and engine mounts are often produced using this technique. The aerospace industry demands precision and reliability, and sand casting allows for the creation of lightweight yet robust parts that can withstand extreme conditions. Furthermore, the process enables the production of complex geometries that are often necessary for modern aircraft designs.
The construction industry frequently utilizes sand casting for creating architectural features and reinforcement structures. Items such as decorative elements, beams, and brackets can be efficiently manufactured through this method. The flexibility of sand casting permits the creation of custom designs that meet specific architectural requirements, making it a popular choice for builders and architects alike.
applications of sand casting process
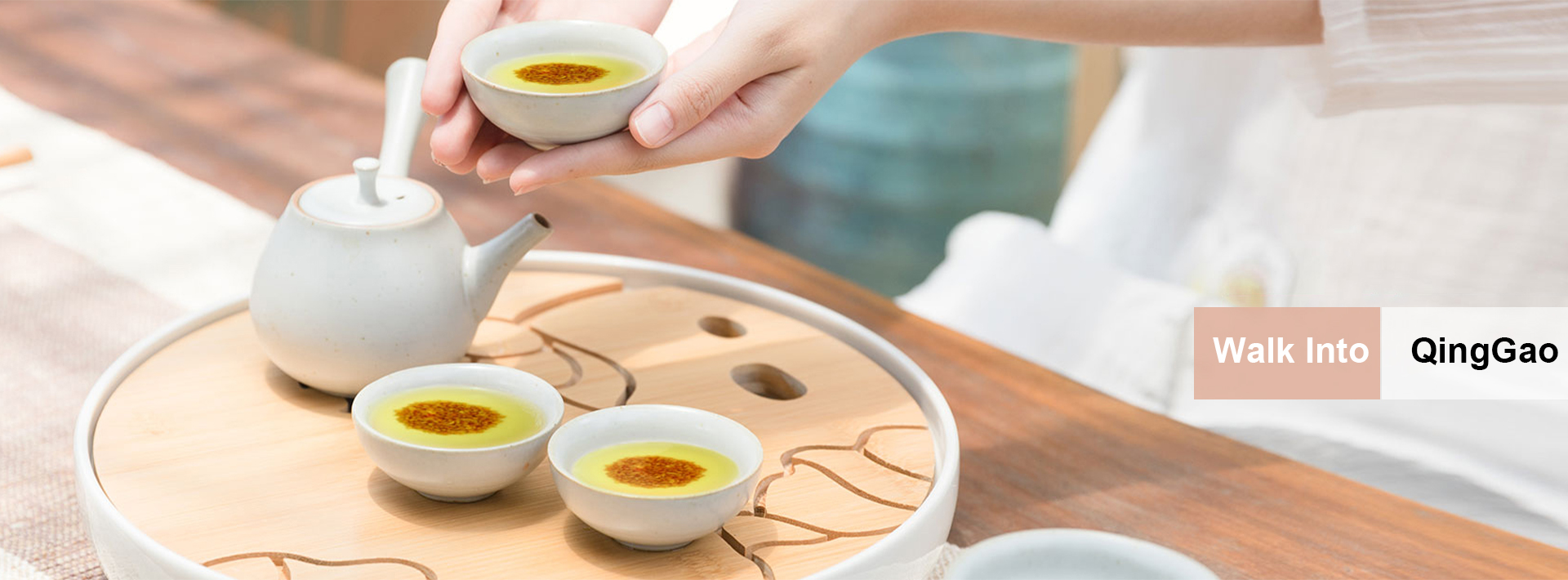
Moreover, sand casting is prevalent in the production of artistic objects and sculptures. Artists and sculptors appreciate the ability of sand casting to reproduce fine details and create larger-than-life pieces. The versatility of sand allows for various surface finishes, enabling artists to achieve the desired aesthetic effects in their work.
Electrical and electronic industries also exploit the benefits of sand casting for manufacturing enclosures and housings for various devices. These components require precise dimensions and the ability to dissipate heat efficiently. Sand casting meets these demands, providing lightweight, durable, and thermally conductive solutions for electrical applications.
Additionally, the energy sector employs sand casting for producing critical equipment components such as pumps, valves, and turbine parts. These components often operate in high-stress environments, where reliability and resilience are paramount. Sand casting's ability to deliver large, robust components with complex geometries makes it a preferred choice in this field.
In summary, the sand casting process has a broad range of applications across various industries, including automotive, aerospace, construction, art, electronics, and energy. Its combination of cost-efficiency, versatility, and capability to produce intricate designs ensures that sand casting remains an essential method for manufacturing in today’s industrial landscape. As technologies advance, its role is likely to evolve further, providing innovative solutions to emerging challenges in manufacturing and design.
Post time:اکتوبر . 15, 2024 05:06
Next:sand castings manufacturer