Why Sand Casting is Preferred in Manufacturing
Sand casting is a versatile and widely used manufacturing process that has stood the test of time, being employed for centuries across various industries. It involves creating a mold from a sand mixture, pouring molten metal into the mold cavity, and allowing it to solidify into the desired shape. Despite the advancements in modern manufacturing processes, sand casting remains a preferred choice for numerous applications. Here are several reasons why sand casting is favored in the industry.
1. Cost-Effectiveness
One of the most significant advantages of sand casting is its cost-effectiveness. The materials required for sand molds, typically sand, clay, and water, are inexpensive and readily available, making the overall production costs lower compared to other casting methods. Additionally, this process does not require expensive tooling, which can be a substantial financial barrier in industries seeking to produce large volumes. This economic advantage makes sand casting particularly appealing for small to medium-sized enterprises and projects with limited budgets.
2. Flexibility in Design
Sand casting offers remarkable flexibility in terms of design and size. It can accommodate a wide range of shapes, from simple to highly complex geometries. Unlike other casting processes that may require highly specialized equipment for each specific part, sand casting can be easily adapted to create different designs by merely changing the mold. This allows manufacturers to produce one-off designs or small production runs without incurring high costs or extensive lead times.
3. Ability to Handle Large Castings
Sand casting is particularly advantageous when dealing with larger components. Many other casting methods struggle with size limitations, but sand casting can produce sizeable and heavy parts with relative ease. This capacity makes sand casting the preferred method for industries producing components like engine blocks, frames, and propellers, where size is often a crucial factor.
4. Excellent Surface Finish and Tolerance Control
why sand casting is preferred
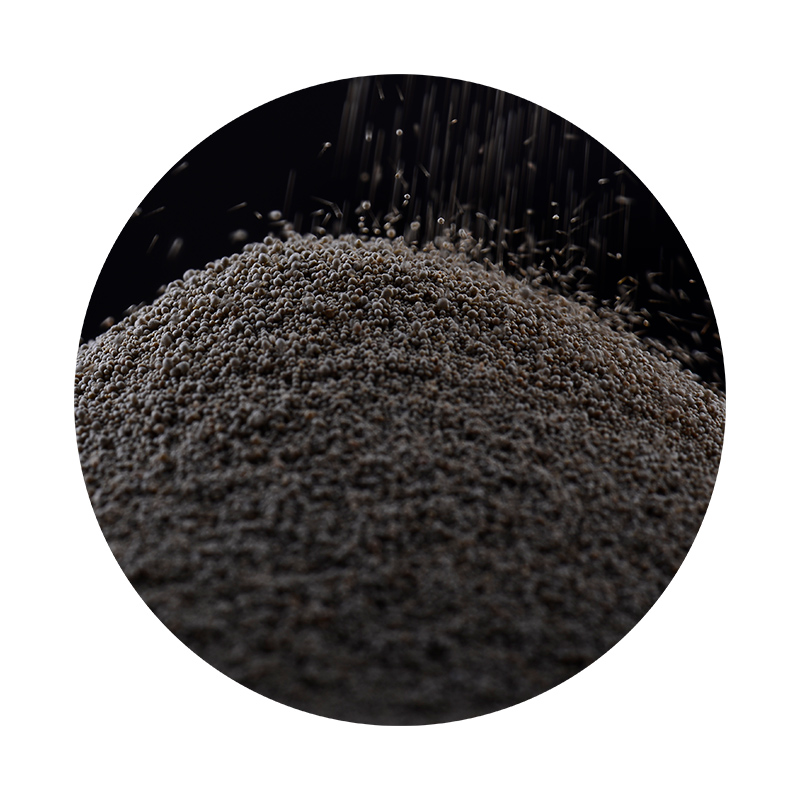
While some may perceive sand casting as less refined, advancements in technology and techniques have led to improved surface finish and tolerances. By using specific sand types and additives, manufacturers can achieve smoother finishes and more precise dimensions. Moreover, secondary operations such as machining can further enhance the final product's surface quality. This balance between precision and cost is often difficult to achieve with other casting processes.
5. Compatibility with Various Metals
Sand casting is compatible with a wide range of metal alloys, including ferrous and non-ferrous metals. This adaptability makes it suitable for various industries, from automotive to aerospace, where different materials are required based on performance specifications. The ability to cast in diverse materials allows manufacturers to meet the unique demands of their products without being limited to specific processes or equipment.
6. Easy to Scale Production
Sand casting can be easily scaled up for mass production while still maintaining efficiency for low-volume runs. Once a pattern is created, multiple molds can be produced quickly, allowing for the efficient manufacturing of identical parts. This scalability is particularly beneficial for industries that may experience fluctuating demands, enabling them to ramp up or down without significant downtime or investment in new technology.
7. Environmentally Friendly
Additionally, sand casting is relatively environmentally friendly. The sand used in the process can be reused multiple times, reducing waste and the demand for new materials. Modern foundries are increasingly implementing sustainable practices, such as recycling sand and managing waste by-products, which further mitigates the environmental impact of manufacturing processes.
In conclusion, sand casting remains a preferred method in manufacturing for numerous reasons, ranging from cost-effectiveness and design flexibility to its ability to produce large components with excellent surface finish. As industries continue to evolve, sand casting is positioned to adapt and remain relevant, making it a cornerstone of modern manufacturing practices. Its versatility and practicality ensure that it will continue to play a vital role in meeting the demands of various applications in the years to come.
Post time:Вер . 29, 2024 03:35
Next:Top Sand Casting Suppliers for High-Quality Metal Components and Solutions