Why is Sand Casting Used?
Sand casting is a time-honored manufacturing process that has been employed for thousands of years, and it continues to be a prevalent method in modern metalworking. Despite the emergence of advanced technologies and materials, sand casting remains popular for various reasons. This article explores the advantages of sand casting, its applications, and why it is such a preferred method in the foundry industry.
At its core, sand casting involves creating a mold from a mixture of sand, clay, and water. The mold cavity is formed by packing this mixture around a pattern, which is a replica of the desired object. Once the mold is ready and the pattern is removed, molten metal is poured into the cavity to create the final product. This simple yet effective process offers several unique benefits.
Why is Sand Casting Used?
Cost-effectiveness is another significant advantage of sand casting. Compared to other casting methods, such as die casting, sand casting requires lower initial setup costs. The materials for the molds are relatively inexpensive, and the process doesn’t necessitate complex machinery for production. This affordability makes sand casting an attractive option for small businesses and startups looking to minimize production costs while maximizing efficiency.
why is sand casting used
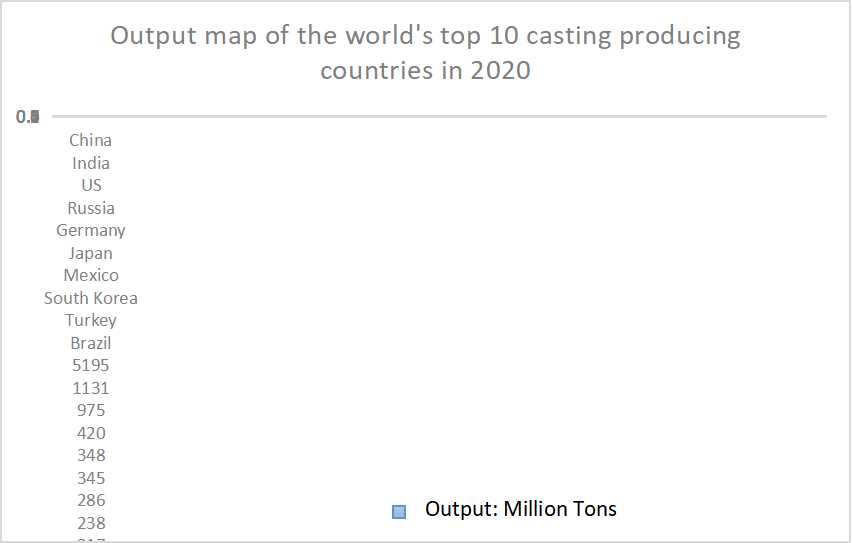
Additionally, sand casting allows for the production of large components. Many metalworking techniques struggle with larger sizes due to limitations in mold-making and shaping. However, sand casting can easily create large molds, enabling the casting of heavy machinery parts and large sculptures. This capability is particularly advantageous for industries like aerospace and automotive, where large and complex components are often required.
The sand casting process also provides a forgiving environment for design modifications. Unlike techniques such as die casting, which require precise molds that are costly and time-consuming to alter, sand molds can be quickly adjusted. This flexibility facilitates rapid prototyping and experimentation, allowing designers and engineers to tweak their designs without incurring significant additional costs or delays.
Moreover, the sand casting process is environmentally friendly. The materials used, primarily sand, can be recycled after casting and reused for the next batch. The ability to recycle sand reduces waste and minimizes the environmental impact of the manufacturing process. This sustainability aspect is becoming increasingly important as global industries strive to reduce their carbon footprints and promote eco-friendly practices.
Another compelling reason for the continued use of sand casting is the fine surface finish and dimensional accuracy that can be achieved. While sand casting may not always match the precision of other casting processes at smaller scales, advancements in sand mold technologies have significantly improved the surface quality of cast parts. For many applications, the finish provided by sand casting is more than adequate, ensuring functionality and aesthetic appeal.
In conclusion, sand casting remains a preferred method in metalworking due to its versatility, cost-effectiveness, ability to produce large components, flexibility in design, environmental sustainability, and adequate surface finish. As industries evolve and advance technologically, sand casting proves its enduring relevance by adapting to new needs and challenges. Whether for creating intricate sculptures or vital machine components, sand casting continues to play a crucial role in the manufacturing landscape, showcasing its importance and practicality in an ever-changing world. This venerable technique not only bridges the gap between traditional and modern manufacturing but also reinforces the timeless principle that sometimes the simplest methods yield the most beneficial results.
Post time:Жов . 05, 2024 00:12
Next:Techniques for Effective Wet Sanding of Resin Projects