Steps of Sand Casting A Comprehensive Guide
Sand casting, also known as sand mold casting, is one of the most widely used metal casting processes. It is known for its versatility and ability to produce complex shapes. This article outlines the key steps involved in the sand casting process, from preparation to finishing.
Step 1 Pattern Making
The first step in sand casting is creating a pattern, which is a replica of the desired product. Patterns are typically made from materials such as wood, metal, or plastic, and they can be made using various techniques such as CNC machining or 3D printing. The pattern must be precise, as it serves as a template that defines the shape and dimensions of the final casting. The pattern also includes allowances for shrinkage and machining, ensuring that the final product meets specifications.
Step 2 Molding
Once the pattern is ready, the next step is creating the mold. This involves compacting a mixture of sand, clay, and water around the pattern. The sand mixture is often referred to as green sand. The mold consists of two halves the cope (top half) and the drag (bottom half). The pattern is placed in a molding box, and sand is packed around it to create a cavity that reflects the shape of the pattern. Once the sand is compacted, the mold is separated, and the pattern is removed, leaving a negative impression.
Step 3 Core Making
In some cases, internal cavities or complex geometries are needed in the final casting. This is where cores come into play. Cores are made from sand mixtures that are bound together using adhesives or binders. These are placed in the mold cavity to create the required internal features. The core must be carefully positioned to ensure it will remain stable during the pouring of metal.
Step 4 Melting the Metal
After the mold is prepared, the next step is to melt the metal that will be cast. The metal is typically heated in a furnace to reach its liquid state. The choice of metal depends on the specific application and may include aluminum, cast iron, steel, or bronze. It's crucial to monitor the temperature to ensure the metal is fully melted and homogeneous, as any impurities can affect the final product quality.
steps of sand casting
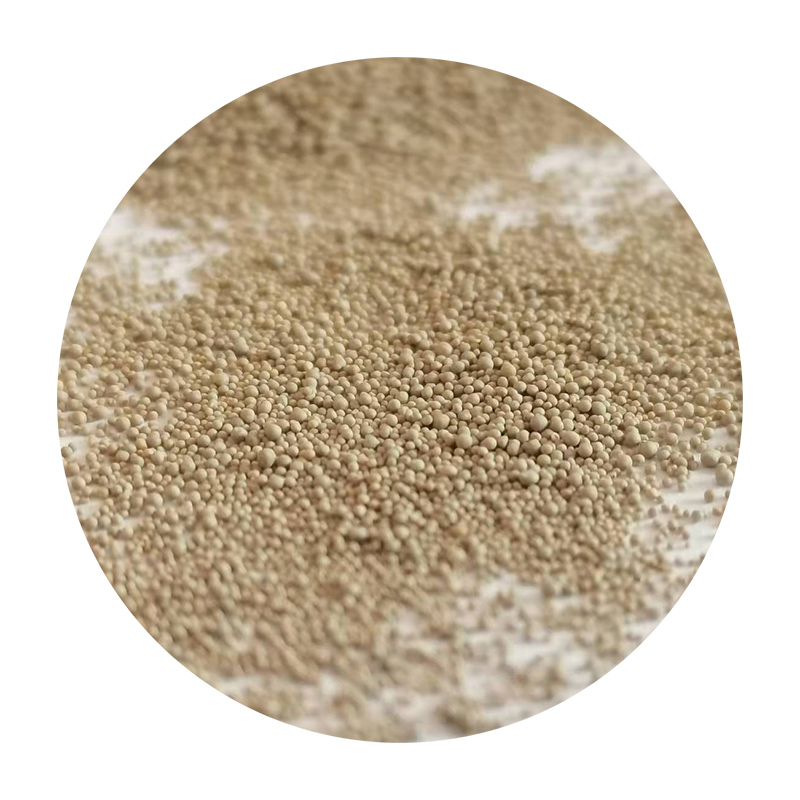
Step 5 Pouring
With the metal melted, it is time to pour it into the mold. The pouring process must be performed carefully to avoid introducing air bubbles or imperfections. The molten metal is poured through a pouring cup and down a sprue, which directs the flow into the mold cavity. Proper pouring techniques are essential to fill the mold completely without causing turbulence that could lead to defects.
Step 6 Cooling
Once the mold is filled, the metal needs time to cool and solidify. The cooling time varies depending on the type and thickness of the metal cast. During this step, the metal transitions from a liquid to a solid state, taking the shape of the mold. It is crucial to allow the metal to cool evenly to avoid warping or cracking.
Step 7 Mold Removal
After the metal has solidified, the next step is to remove the mold. This involves breaking away the sand mold, exposing the newly cast part. The remaining sand can often be reused, making sand casting an environmentally friendly process. Care must be taken during this step to avoid damaging the cast part.
Step 8 Cleaning and Finishing
The final step in the sand casting process is cleaning and finishing the casting. This may involve removing any excess material, such as risers and gates, and cleaning the surface to remove sand residues. Depending on the application, additional finishing processes such as machining, grinding, or polishing may be necessary to achieve the desired surface finish and dimensional accuracy.
Conclusion
Sand casting is a reliable and cost-effective method for producing metal parts with complex shapes. Understanding the steps involved—pattern making, molding, core making, melting, pouring, cooling, mold removal, and finishing—can help manufacturers optimize the process and produce high-quality castings. With advancements in technology, sand casting continues to evolve, offering even greater precision and efficiency for various industrial applications.
Post time:Лис . 06, 2024 19:39
Next:Understanding the Characteristics and Uses of Gold Sand in Nature and Industry