Steps in Sand Casting A Comprehensive Overview
Sand casting is a widely used manufacturing process that allows for the production of metal parts with complex geometries. It is particularly popular in industries that require the production of heavy components, such as automotive, aerospace, and machinery. This article will detail the essential steps involved in sand casting, providing insights into each phase of the process.
Step 1 Pattern Making
The process begins with the creation of a pattern, which is a replica of the final product. The pattern is typically made from materials like wood, metal, or plastic and is slightly larger than the final item to account for shrinkage during the cooling of metal. This step is crucial as the pattern determines the shape and accuracy of the final casting. Patterns can be single-piece or multi-piece, depending on the complexity of the part being produced.
Step 2 Core Making
In many cases, especially with hollow parts, cores are used to create internal voids. Cores are usually made of sand bonded with a resin or other materials to withstand the molten metal. The cores are placed in the mold to form the internal shapes before pouring the metal. This step requires precision to ensure that the cores fit well within the mold and maintain their shape during the casting process.
Step 3 Mold Preparation
The next step involves preparing the mold. The pattern is placed in a flask, which is a container that holds the molding material. Sand mixed with a binder is packed around the pattern to create the mold. This sand mixture is compacted to ensure it holds the shape of the pattern. Once the sand is set, the pattern is carefully removed, leaving a cavity that mirrors the pattern's shape. In the case of two-part molds, the process is replicated for the second half.
Step 4 Pouring the Metal
steps in sand casting
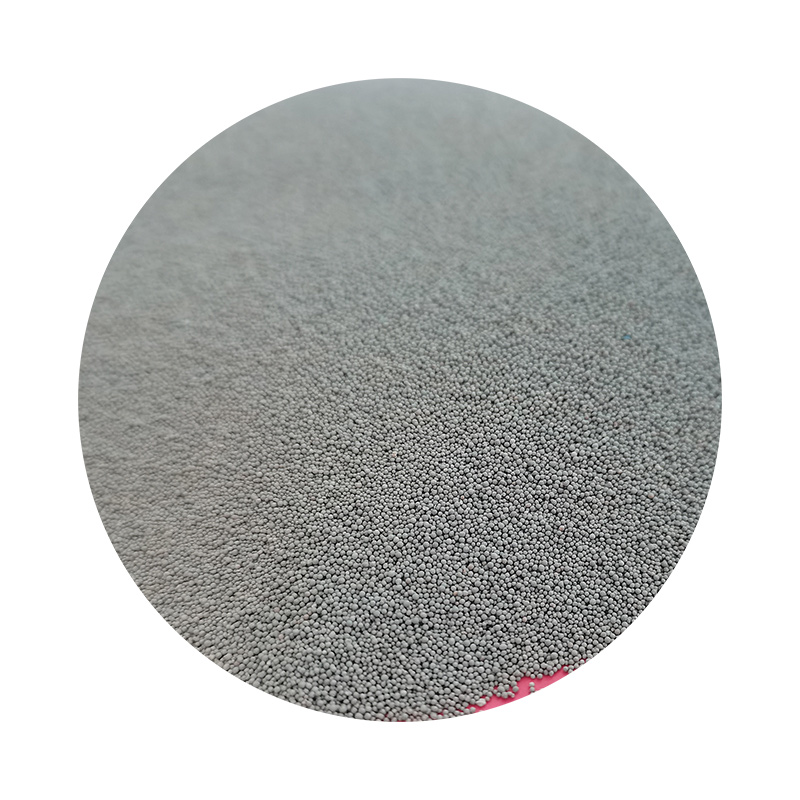
With the mold ready, the molten metal is prepared for pouring. The metal is heated in a furnace until it reaches a liquid state, typically between 1200°C and 1500°C, depending on the alloy. Once the metal is sufficiently heated, it is carefully poured into the mold cavity through a pouring basin and down into the sprue. This step requires precision and control to avoid defects such as spills or gas pockets.
Step 5 Cooling and Solidification
After pouring, the metal is allowed to cool and solidify. The cooling rate varies depending on the metal and thickness of the casting. It is vital to allow adequate time for the metal to fully solidify before proceeding to the next step, as removing the casting too early can result in deformation or fractures.
Step 6 Mold Removal and Cleaning
Once the metal has cooled and solidified, the mold is dismantled to reveal the cast part. This is done carefully to avoid damaging the newly formed casting. The casting typically has sand and residual materials attached, which must be cleaned off. This can involve sandblasting, grinding, or other cleaning methods to achieve the desired surface finish.
Step 7 Finishing Operations
The final step in the sand casting process involves various finishing operations. These can include machining, polishing, and surface treatments to enhance the properties of the casting. The finished part is then inspected for quality assurance to ensure it meets the specified dimensions and tolerances.
In conclusion, sand casting is a versatile and efficient method for producing metal parts. Each step in the process, from pattern making to finishing operations, plays a crucial role in ensuring the final product is of high quality and meets the requirements of the intended application. With its ability to produce intricate designs and accommodate various materials, sand casting remains a fundamental technique in the manufacturing industry.
Post time:Лис . 10, 2024 05:40
Next:Resin Sand Casting Techniques for Improved Casting Quality and Efficiency