The Role of Sand in Sand Casting
Sand casting is one of the oldest and most versatile metal casting processes still widely used today. The process involves creating a mold from sand, which is then used to form components made from metals. An essential element of this technique is the type of sand used, which greatly influences the quality of the final product as well as the overall efficiency of the casting process.
Composition of Sand
The primary type of sand used in sand casting is silica sand, composed mainly of silica (SiO₂). Silica sand is favored for its high melting point and ability to withstand the high temperatures associated with molten metal. However, other types of sand can also be used, including olivine sand, zircon sand, and chromite sand. Each type brings unique properties suitable for specific applications. For example, olivine sand is known for its thermal stability, while zircon sand offers excellent hardness and resistance to thermal shock.
Types of Sand Casting Molds
The sand used in sand casting is typically mixed with a binding agent, such as clay, to create a moldable material. The two most common methods of sand molding are green sand and dry sand. Green sand is a mixture of sand, clay, and water, creating a mold that is moist and can retain its shape during the casting process. This method is popular because it is inexpensive and easy to work with. Dry sand, on the other hand, is baked to harden it before use, making it suitable for creating more intricate shapes and ensuring better surface finished parts.
Importance of Sand Quality
sand used in sand casting
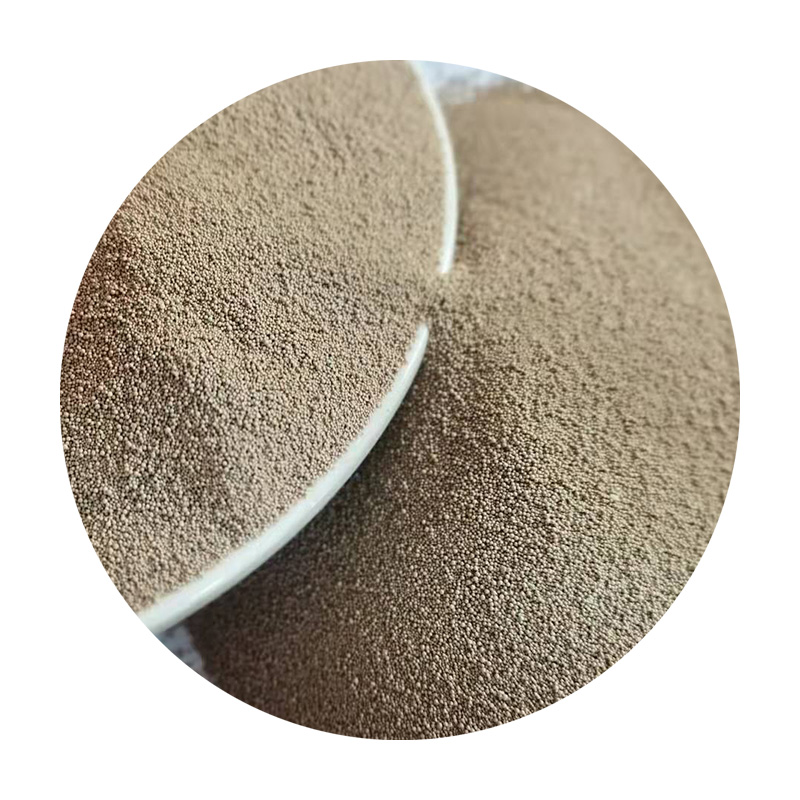
The quality of sand plays a crucial role in determining the reliability of sand casting processes. Factors such as grain size, shape, and distribution can significantly affect the mold's strength and permeability. Ideally, the sand grains should be rounded as this enhances the flow of the sand during the molding process while also contributing to a better surface finish on the final cast product. Moreover, the sand should be free from impurities, as contaminants can lead to defects in the cast product and affect the physical properties of the metal.
Recycling and Environmental Considerations
One of the advantages of using sand in casting is its recyclability. Once the metal has cooled and solidified, the sand can be extracted, cleaned, and reused for subsequent castings. This not only reduces waste but also lowers the cost associated with new sand procurement. However, it is vital to monitor sand quality as it can degrade over time due to the repeated thermal cycles and mechanical stresses during the casting process.
Challenges in Sand Casting
Despite its advantages, sand casting is not without challenges. The risk of sand sticking to the cast product, known as sand burn-on, can compromise the surface quality. Additionally, the moisture content in green sand must be carefully controlled; too much moisture can lead to gas defects, while too little can cause cracks in the mold. Another challenge is achieving precise dimensional tolerances, which can be harder to attain compared to other casting methods.
Conclusion
In summary, sand plays an integral role in the sand casting process, not merely as a mold material but as a factor that influences the quality, efficiency, and feasibility of production. Understanding the properties of different types of sand, alongside managing its quality and recyclability, is crucial for optimizing casting processes. As industries continue to advance, innovations in sand and binder technology may further enhance the capabilities and sustainability of sand casting, solidifying its importance in metal manufacturing for years to come.
Post time:Вер . 28, 2024 14:47
Next:wet sand 3d print